Este manual de instrucciones pretende ser una guía para el manejo de la RFlex Extreme. Para garantizar un rendimiento óptimo de su soldadora, siga exactamente las recomendaciones y especificaciones.
Índice
- Capítulo 1. Uso previsto Uso previsto
- Capítulo 2: Señales de seguridad y pictogramas
- Capítulo 3. Datos técnicos Datos técnicos
- Capítulo 4. Descripción técnica Descripción técnica
- Capítulo 5. Montaje e instalación Montaje e instalación
- Capítulo 6. Funcionamiento Operación
- Capítulo 7: Selección de los parámetros de soldadura
- Capítulo 8. Mantenimiento Mantenimiento
- Capítulo 9:
Salud y seguridad en el trabajo
- Capítulo 10. Documentación eléctrica Documentación eléctrica
- Capítulo 11: Documentación neumática
- Capítulo 12: Instrucciones generales
- Capítulo 13: Apéndices
- Capítulo 14. Documentos adicionales de la máquina Documentos adicionales de la máquina
Para obtener más información técnica sobre esta máquina, llame a nuestro Centro de resoluciones al 1-855-888-WELD o envíe un correo electrónico a service@weldmaster.com.
1.0 Visión general de la máquina/uso previsto
La soldadora RF RFlex es una máquina diseñada para soldar grandes superficies estructurales, como membranas, cubiertas de lona, tiendas de campaña, estructuras tensadas, vallas publicitarias y otros tejidos técnicos de PVC/PU. Además, la máquina está equipada con la tecnología avanzada gracias a la cual se puede mejorar la eficiencia y la calidad de la producción.
Además, el uso del generador de RF (27,12 MHz) permite al operador ajustar el flujo de potencia sin problemas, lo que garantiza también la estabilización de los parámetros y la eficiencia de la soldadura adecuada (soldaduras lineales hasta la longitud de 1200 mm). La colocación del panel de control en el brazo extensible móvil facilita el trabajo del operario. Todas las máquinas son seguras para los operadores y fueron construidas de acuerdo con los estrictos requisitos de las directivas CE aplicables.
Además, se pueden soldar en la máquina dos o más capas de los materiales de pérdida dieléctrica artificial y, en particular, como los fabricados a partir de cloruro de polivinilo (PVC, PA, PU) o de poliuretano, poliamida y poliéster, por no hablar de los fabricados a partir de mezclas de los ingredientes mencionados.
Por último, la aplicación de la solución técnica basada en el prensado neumático contra los materiales soldados permite que las capas queden unidas de forma permanente cuando se enfrían, aunque la forma de la soldadura depende del electrodo elegido.
LAS CARACTERÍSTICAS MÁS IMPORTANTES DE LA MÁQUINA:
- el mantenimiento rutinario de la máquina es muy sencillo;
- el prensado puede ajustarse con precisión;
- el fabricante instaló el botón de emergencia en el panel de control;
- la máquina está equipada con la columna luminosa de señalización para aumentar la seguridad del operador cuando la máquina está encendida;
- el operador puede programar y controlar el ciclo de trabajo de la máquina gracias al panel táctil HMI;
- la herramienta de programación permite al operario introducir en el sistema parámetros como: el tiempo y la potencia de soldadura junto con el tiempo de enfriamiento;
- mediante el panel HMI instalado en la máquina, el operario puede guardar muchos programas de soldadura para distintos tipos de materiales, por no hablar de los que se utilizan para trabajar con distintos tipos de electrodos;
- Para mayor comodidad del operario, la máquina está equipada con un portaelectrodos especialmente diseñado para cambiar rápidamente el electrodo de soldadura;
- la máquina está equipada con el electrodo de puesta a tierra adicional para proteger al usuario contra el aumento del nivel de radiación HF no ionizante emitida por la máquina;
- ZTG HF AutoTuning System™: la máquina está equipada con el sistema de control automático de la potencia de salida para aumentar la seguridad del operador;
- ZTG SafeDOWN™ - la máquina se suministra con el sistema que debe proteger eficazmente al operador contra el electrodo cuando se está bajando;
- ZTG Flash™ - otro sistema de la máquina que se supone que protege el electrodo y la materia prima que se está soldando de los posibles daños causados por un paso de arco;
- Todas las máquinas han recibido los certificados de conformidad CE
TECNOLOGÍA DE ALTA FRECUENCIA:
La soldadura de alta frecuencia, conocida como soldadura por radiofrecuencia (RF) o dieléctrica, es el proceso de fusión de materiales mediante la aplicación de energía de radiofrecuencia a la zona que se va a unir. La soldadura resultante puede ser tan fuerte como los materiales originales.
La soldadura HF se basa en determinadas propiedades del material a soldar para provocar la generación de calor en un campo eléctrico que alterna rápidamente. Esto significa que sólo algunos materiales pueden soldarse con esta técnica. El proceso consiste en someter las piezas que se van a unir a un campo electromagnético de alta frecuencia (normalmente 27,12 MHz), que se aplica normalmente entre dos barras metálicas. Estas barras también actúan como aplicadores de presión durante el calentamiento y el enfriamiento. El campo eléctrico dinámico hace oscilar las moléculas de los termoplásticos polares. Dependiendo de su geometría y momento dipolar, estas moléculas pueden traducir parte de este movimiento oscilatorio en energía térmica y provocar el calentamiento del material. Una medida de esta interacción es el factor de pérdida, que depende de la temperatura y la frecuencia.
El cloruro de polivinilo (PVC) y los poliuretanos son los termoplásticos más comunes que se sueldan mediante el proceso de RF. Es posible soldar por RF otros polímeros, incluidos nylon, PET, PET-G, A-PET, EVA y algunas resinas ABS, pero se requieren condiciones especiales; por ejemplo, el nylon y el PET son soldables si se utilizan barras de soldadura precalentadas además de la potencia de RF.
La soldadura por HF no suele ser adecuada para PTFE, policarbonato, poliestireno, polietileno o polipropileno. Sin embargo, debido a las inminentes restricciones en el uso del PVC, se ha desarrollado un grado especial de poliolefina que sí puede soldarse por RF.
La función principal de la soldadura HF es formar una junta en dos o más espesores de chapa. Existen varias funciones opcionales. La herramienta de soldadura puede grabarse o perfilarse para dar a toda la zona soldada un aspecto decorativo o puede incorporar una técnica de gofrado para colocar letras, logotipos o efectos decorativos en los elementos soldados. Al incorporar un filo de corte adyacente a la superficie de soldadura, el proceso puede soldar y cortar simultáneamente un material. El filo de corte comprime el plástico caliente lo suficiente como para permitir arrancar el material sobrante, de ahí que este proceso se conozca a menudo como soldadura por desgarro.
ATENCIÓN: El fabricante no se hace responsable de los daños o lesiones derivados de un uso inadecuado de esta máquina.
ATENCIÓN: Para utilizar la máquina de forma óptima y segura, lea atentamente y siga todas las instrucciones incluidas en este Manual de Operación y Mantenimiento.
ATENCIÓN: Todos los operarios, formados en seguridad operacional, procedimientos de operación y riesgo de la máquina de soldar, así como los cualificados para operar la máquina de soldar, deberán, por parte del Contratista, firmar, con su firma legible, el formulario adjunto.
ATENCIÓN: La máquina de soldar de alta frecuencia ha sido diseñada y fabricada en una versión no apta para personas discapacitadas. Cuando la máquina vaya a ser manejada por personas discapacitadas, deberá ser adaptada adecuadamente previa consulta con el fabricante.
2.0 Señales de seguridad y pictogramas
2.1 Información general
Para utilizar la soldadora de forma óptima y segura, lea atentamente y siga todas las instrucciones incluidas en este Manual de Operación y Mantenimiento, también en particular toda la información y señales de advertencia, prohibición, restricción y orden.
Sobre la base de la información incluida en este Manual de Operación y Mantenimiento, el Cliente debe elaborar Manuales de Puesto de Trabajo para los empleados.
El Cliente es plena, legal y materialmente responsable de todos y cada uno de los sucesos que resulten de un conocimiento insuficiente de este Manual de Operación y Mantenimiento o del incumplimiento de los principios de la Seguridad y Salud en el Trabajo.

ATENCIÓN: Antes de iniciar cualquier trabajo de cualquier persona que opere la máquina de soldadura HF es obligatorio familiarizarse con el Manual de Operación y Mantenimiento subsiguiente.
ATENCIÓN: Cualquier receptor o persona autorizada por el receptor sobre la base del presente Manual de Operación y Mantenimiento y la característica adecuada de la producción-tecnología es obligatorio debido emitir MANUAL DE MANDO DE TRABAJO para los operarios.
ATENCIÓN: La máquina de soldadura de alta frecuencia puede ser operada SOLO por trabajadores que hayan sido formados en el mantenimiento del aparato y en SEGURIDAD INDUSTRIAL con especial consideración del posible riesgo procedente de la máquina.
ATENCIÓN: Durante toda la vida útil de la máquina, el Fabricante del dispositivo sugiere al Comprador utilizar el personal de servicio capacitado proporcionado por el Fabricante o cualquier equipo de servicio autorizado por el Fabricante.
ATENCIÓN: El fabricante recomienda encarecidamente instalar la máquina de soldar sólo en un entorno industrial.
ATENCIÓN: La máquina debe estar correctamente nivelada y debe tener lugar fijo de una operación.
ATENCIÓN: La manipulación descuidada de la máquina durante el transporte (traslado) puede provocar lesiones graves o accidentes.
ATENCIÓN: El generador es alimentado por la tensión peligrosa para la vida de la red eléctrica 3 x480 VAC; 50 Hz. El dispositivo tiene el alto voltaje hasta 8000 VDC. Todas las actividades de servicio o prevención sólo pueden ser ejecutadas por el personal capacitado con la autoridad requerida por la ley.
ATENCIÓN: Es necesario que el Comprador se encargue de la correcta ejecución y del control periódico de prevención de la instalación de protección contra descargas eléctricas para cada aparato que esté en uso. Toda la responsabilidad en esta materia recae sobre el Comprador.
ATENCIÓN: La tensión de la lámpara debe ser la misma que se especifica en la ficha técnica del producto - es posible ajustarla mediante derivaciones en el primario del transformador de incandescencia.
ATENCIÓN: La lámpara debe precalentarse durante aproximadamente una hora después de la instalación.
ATENCIÓN: Cualquier trabajo dentro de la zona de la unidad de prensado activo de la prensa, es decir, la sustitución del dispositivo puede ser ejecutado con medidas de precaución especiales sólo por el equipo de servicio capacitado.
ATENCIÓN: La parada de emergencia de la máquina es posible en cualquier momento pulsando la tecla EMERGENCIA Botón STOP (el botón rojo sobre fondo amarillo).
ATENCIÓN: El entorno de trabajo de la máquina, el suelo y los soportes y asideros manuales deben estar siempre limpios y libres de cualquier tipo de contaminación, grasa o barro, para reducir al mínimo posible el riesgo de resbalones o caídas.
PRECAUCIÓN: Desenchufe la máquina antes de retirar cualquier panel de acceso o abrir las puertas. Todos los protectores y paneles de acceso deben estar en su lugar antes de operar esta máquina.
ATENCIÓN: La temperatura del electrodo es de hasta 100 °C. Por lo tanto, cuando se toca uno puede ser quemado.
ATENCIÓN: La lámpara contiene metales de tierras raras y óxidos metálicos de tierras raras que son altamente tóxicos. En caso de rotura, la lámpara debe eliminarse con sumo cuidado y con la ayuda de especializado servicios.
ATENCIÓN: La máquina de soldadura de alta frecuencia es una fuente de radiación electromagnética no iónica. Después de la instalación de la máquina en el lugar del comprador, la medición de la radiación no iónica se debe hacer. Las mediciones de radiación deben ser realizadas por una empresa autorizada.
ATENCIÓN: La máquina de soldadura de alta frecuencia debe trabajar en un lugar de trabajo firme, ya que la transposición requiere una nueva medición de la intensidad de la radiación no iónica..
ATENCIÓN: Está prohibido que las personas con marcapasos implantado permanezcan en la zona de radiación activa..
ATENCIÓN: El fabricante sugiere no emplear a ninguna mujer embarazada o en período de lactancia en la zona de radiación no iónica activa..
ATENCIÓN: Limpie el filtro de aire de la instalación neumática al menos una vez al mes.


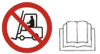

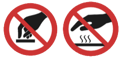



























3.0 Datos técnicos
Tipo deype |
ZDW-15-K |
Materiales de soldadura |
PVC, tejidos recubiertos de PVC |
Alimentación |
3 x 480 V; 50 Hz |
Controlador PLC |
Delta |
Tensión de control |
24 VDC |
Capacidad instalada |
22 kVA |
Potencia de salida en HF |
15 kW |
Ajuste de la capacidad de salida |
manual/autotuner |
Corte principal |
40 A; con retraso |
Frecuencia de funcionamiento |
27,12 MHz |
Estabilidad de frecuencia |
+/- 0,6 % |
Sistema antiflash, ZEMAT TG |
sensor ARC de sensibilidad ultrarrápida |
Consumo de aire comprimido |
70 nl/ciclo |
Presión de aire comprimido |
0,4-0,8 MPa |
Longitud máx. del electrodo |
1200 mm |
Tamaño de la mesa de trabajo |
1620 x 820 mm |
Tamaño de la placa de presión |
1200 x 50 mm |
Carrera del actuador |
~ 150mm |
Accionamiento del electrodo de presión |
neumático |
Accionamiento del electrodo de tierra |
neumático |
Fuerza de presión (máx.) |
1200 kG |
Lámpara del generador |
ITL 12-1 |
Refrigerante |
aire |
Peso de la máquina |
~ 1100 kg |
Dimensiones |
VER ANEXOS |
4.0 Descripción técnica
El elemento principal de la soldadora de alta frecuencia ZDW-15-K es la estructura portante fabricada con chapas y perfiles de acero soldados. Todas las demás partes de la máquina están montadas sobre dicha estructura. La estructura portante puede dividirse en dos partes básicas:
- La trasera donde se encuentra el generador de alta frecuencia junto con el transformador de ánodo y la caja de interruptores. Esta parte está encerrada en los escudos desmontables protegidos por el interruptor-llave de final de carrera.
Se supone que los escudos aplicados junto con los interruptores-llaves minimizan la emisión de radiación no ionizante. Queda terminantemente PROHIBIDO utilizar la soldadora sin los protectores.
-
La primera es la llamada zona de soldadura, donde se encuentra la mesa de trabajo en la que el operario coloca el material durante el proceso de soldadura. La soldadura se realiza por el electrodo que se presiona contra la mesa de trabajo forrada con la almohadilla aislante (el divisor en forma de la placa de aluminio forrada con la almohadilla aislante también se puede poner en uso con el fin de evitar cualquier daño a la mesa de trabajo). El electrodo se fija en el soporte automático que está sujeto al vástago del pistón del actuador. La parte superior del portaelectrodo se fija a la construcción de la máquina con ayuda de finas chapas de latón (masa). El portaelectrodo de soldadura está equipado con la pinza automática que se controla con la ayuda del panel táctil HMI. Gracias a la pinza automática, el operario puede cambiar el electrodo sin utilizar herramientas. El electrodo se fija a la salida del generador de alta frecuencia con ayuda de la chapa (como guía de ondas). La zona de soldadura está protegida de la radiación no ionizante por el electrodo de puesta a tierra móvil que se presiona contra la mesa durante el procedimiento de soldadura y, como resultado, se crea una especie de condensador que se supone que limita la radiación no ionizante.
Se supone que los escudos aplicados junto con los interruptores-llaves minimizan la emisión de radiación no ionizante. Queda terminantemente PROHIBIDO utilizar la soldadora sin los protectores.
La máquina hace pleno uso de los siguientes sistemas:
- EL CONTROL UNO formado por el PLC con el panel táctil HMI, los mandos e indicadores situados en el panel de control principal fijado al brazo extensible y otros aparatos eléctricos y electrónicos instalados en esta máquina; y
- EL AIRE COMP RIMIDO UNO compuesto principalmente por el conjunto de preparación de aire comprimido que incluye: las válvulas de distribución y los actuadores neumáticos; y
- EL GENERADOR consiste en un generador autoexcitado de alta frecuencia de constantes de desintegración que consta principalmente del circuito LC de alto factor Q ajustado en 27,30MHz. El sistema consiste también en el tubo de onda viajera, el transformador del ánodo, el transformador del filamento y el sistema de enfriamiento del tubo;
El portaelectrodos de soldadura está equipado con un sistema de agarre automático controlado desde el panel táctil HMI. Permite sustituir los electrodos sin necesidad de herramientas.
Se supone que los escudos aplicados junto con los interruptores-llaves minimizan la emisión de radiación no ionizante. Queda terminantemente PROHIBIDO utilizar la soldadora sin los protectores.
La máquina lleva incorporado un sistema (ZTG AntyCRUSH) diseñado para proteger las manos de los operarios contra el aplastamiento. Cuando una mano o cualquier objeto con una altura diferente de la altura del material soldado se coloca debajo del electrodo de soldadura, el electrodo se tira automáticamente hacia arriba durante la fase de prensado.
Se supone que los escudos aplicados junto con los interruptores-llaves minimizan la emisión de radiación no ionizante. Queda terminantemente PROHIBIDO utilizar la soldadora sin los protectores.
Además, hay indicadores láser instalados en el chasis de la máquina para facilitar el posicionamiento del material soldado en la mesa de trabajo.
Las piezas básicas de la máquina:
- La columna luminosa de señalización;
- El panel táctil HMII;
- Los mandos e indicadores situados en el panel de control principal;
- La pinza portaelectrodos;
- La mesa de trabajo;
- Los interruptores de pedal;
- La estructura portante;
- El kit de preparación de aire comprimido;
- El tornillo de ajuste con cuya ayuda el electrodo debe ajustarse paralelamente a la mesa de trabajo;
- Finas láminas de latón (masa) con ayuda de las cuales se fija la parte superior del electrodo a la construcción de la máquina;
- Electrodo de soldadura;
- Electrodo de puesta a tierra.
5.0 Montaje e instalación
5.1 Información y señales de restricciones e imperativos
El Fabricante proporciona un embalaje adecuado de la máquina para el momento del transporte. El tipo y la durabilidad del embalaje se adaptan a la distancia y al medio de transporte y, en consecuencia, al riesgo potencial de daños durante el transporte. El Fabricante sugiere que cada Cliente utilice los medios de transporte y el personal de servicio técnico del Fabricante.
El almacenamiento de la máquina no implica ningún requisito particular, aparte de un entorno de almacenamiento adecuado.
El local de almacenamiento debe garantizar una protección suficiente contra los factores meteorológicos, debe ser lo más seco posible y tener un nivel de humedad aceptable (inferior al 70%). También es necesario garantizar una protección adecuada contra la corrosión, sobre todo en lo que respecta a los componentes metálicos que no están pintados por razones técnicas.
Si la máquina se suministra en una caja y se envuelve en plástico que genera una atmósfera anticorrosiva, la máquina debe permanecer envuelta y embalada durante todo el periodo de almacenamiento.
A efectos de protección contra la humedad, se recomienda no almacenar la máquina directamente sobre el suelo del almacén, sino sobre palés.
La lámpara del generador (triodo) es un componente que requiere especial atención y manipulación en todas las fases, incluido el almacenamiento. La lámpara debe almacenarse en su embalaje original, en posición vertical, con el ánodo dirigido hacia arriba o hacia abajo, en una habitación seca. La lámpara es un componente de alto vacío, metálico y cerámico, que es extremadamente frágil y no se puede golpear ni dejar caer ni siquiera desde poca altura.
Golpear, dejar caer, sacudir o inclinar la lámpara durante un tiempo prolongado puede y suele provocar daños permanentes e irreversibles en la lámpara. En particular, el filamento de la lámpara - cátodo puede romperse, lo que en la mayoría de los casos extremos puede provocar cortocircuitos internos o la rotura de la lámpara.
ATENCIÓN: El fabricante sugiere no emplear a ninguna mujer embarazada o en período de lactancia en la zona de radiación no iónica activa..
Las disposiciones anteriores tienen por objeto instruir y advertir a todas las personas y servicios que puedan tener contacto con esta unidad acerca de su alta vulnerabilidad a todos los impulsos y golpes. Al mismo tiempo, no se aceptará ninguna reclamación relacionada con los daños permanentes descritos anteriormente en el curso del procedimiento de reclamación.
También hay que destacar que la lámpara del generador es un componente muy caro.
En caso de duda, se recomienda consultar al personal especializado del Fabricante.
5.2 Transporte de la máquina
El responsable del transporte y de la instalación de la máquina en la sede del ordenante deberá determinarse en el momento de la firma del contrato y, a más tardar, después de la prueba de recepción final de la máquina en la sede del fabricante, antes de la entrega del aparato al ordenante.
ATENCIÓN: Una manipulación descuidada del aparato durante el transporte / traslado puede provocar lesiones graves o accidentes.
SE PROHÍBE el montaje, desmontaje o transporte de la máquina por parte de personal sin la cualificación adecuada o sin estar familiarizado con los requisitos de seguridad descritos en el presente Manual de Operación y Mantenimiento. Tales acciones pueden causar accidentes o daños materiales.
Teniendo en cuenta el carácter específico del aparato, el Fabricante sugiere que cada Ordenante utilice los medios de transporte y el personal de servicio técnico del Fabricante.
El tubo de alimentación debe desmontarse antes de cualquier transporte o movimiento.
La lámpara debe transportarse o moverse siempre en el embalaje original del fabricante, en posición vertical, con el ánodo dirigido hacia arriba o hacia abajo, sin golpear ni sacudir la lámpara.
ATENCIÓN: La máquina debe transportarse en posición vertical.
Debido a su tamaño y estructura, la máquina requiere el desmontaje y desconexión de algunos componentes y unidades para el momento del transporte o mudanza. Es necesario desmontar componentes y herramientas frágiles y costosas (que deben transportarse en un maletín aparte). Es absolutamente necesario desmontar la lámpara del generador.
La máquina debe trasladarse utilizando dispositivos de elevación -grúas, carretillas elevadoras, transpaletas- con una capacidad de elevación suficiente que permita el transporte seguro del generador, mientras que las personas que manejen dichos dispositivos de elevación deben tener todas las licencias y cualificaciones válidas exigidas por la ley.
Todos los componentes de la máquina que puedan resultar dañados durante el transporte (si no se utiliza una caja de embalaje de alta durabilidad) o por dispositivos de elevación o desplazamiento deben asegurarse adecuadamente (siempre que se desmonten y embalen por separado).
Para garantizar una posición estable del dispositivo, es muy importante asegurar una protección adecuada de la máquina durante el tiempo de transporte largo (cinturones de seguridad, pernos de anclaje), así como protección y asistencia durante el transporte in situ.
Si la máquina no está equipada con los herrajes adecuados, es posible utilizar cualquier otro orificio o elemento disponible de suficiente durabilidad para garantizar que el generador y otras partes de la máquina estén correctamente equilibrados y estabilizados.
El peso de la máquina (unos 1.100 kg) debe tenerse muy en cuenta a la hora de planificar el transporte.
5.3 Instalación en el lugar de funcionamiento
Dependiendo del grado de complejidad de la máquina, la instalación en el lugar de operación debe ser realizada por el personal del Ordenante, habiendo leído este Manual de Operación y Mantenimiento o personal de servicio técnico del Fabricante, en cooperación con el personal del Ordenante.
Recuerde que la colocación e instalación adecuadas de la máquina de soldar son vitales para garantizar su funcionamiento óptimo, así como la comodidad y seguridad del operario en el entorno del aparato.
El Ordenante es responsable de la preparación del lugar para la instalación del dispositivo, la disponibilidad y preparación de las conexiones eléctricas y la realización de los requisitos particulares del diseño técnico y las pruebas de aceptación técnica que aprueban todo el generador para su uso.
El Fabricante proporcionará al Ordenante todas las instrucciones e información necesarias al respecto.
ATENCIÓN: Asegúrese de que el suelo / la superficie / los cimientos sobre los que se va a colocar la máquina tienen suficiente durabilidad, teniendo en cuenta el peso, la superficie y la distribución del peso de la máquina en sus puntos de apoyo (normalmente las patas).
ATENCIÓN: El dispositivo debe estar correctamente nivelado y debe tener lugar fijo de una operación.
El lugar óptimo de funcionamiento de la máquina de soldadura de alta frecuencia es la superficie de hormigón no cubierta o cubierta con una capa muy fina de material no conductor.
La superficie debe hacerse de acuerdo con el diseño particular siguiendo las normas de construcción y seguridad, así como siguiendo los requisitos relativos a las posiciones paralelas, perpendiculares y planas.
ATENCIÓN: El Ordenante es el único responsable de la realización de las condiciones mencionadas.
Tras la ubicación de la máquina de soldar en el lugar elegido, es necesario nivelar la máquina, comprobar su estado técnico y eliminar todos y cada uno de los defectos que se hayan podido producir durante el transporte. A continuación, desembalar, colocar, nivelar y fijar el generador. La lámpara del generador de alta frecuencia debe montarse al final del proceso de instalación. Esta tarea debe realizarse con especial atención, tanto al montar la lámpara en el zócalo/base como al conectar los contactos eléctricos de la lámpara. Conecte los conectores de la consola de control a las tomas debidamente marcadas de la prensa. Se recomienda que la instalación de la máquina después del transporte se realice bajo la supervisión directa de un representante del fabricante.
ATENCIÓN: Si las tareas antes mencionadas son realizadas por un representante del Cliente, las mismas deben ser realizadas estrictamente de acuerdo con la descripción contenida en este Manual de Operación y Mantenimiento y/o instrucciones proporcionadas por el fabricante durante la prueba de aceptación técnica.
Debido al campo magnético generado, no deben colocarse objetos metálicos de gran tamaño cerca de la máquina. La máquina puede afectar al funcionamiento de dispositivos electrónicos (radio, televisores, ordenadores) situados cerca de la máquina, como resultado de la alta sensibilidad de entrada de los dispositivos mencionados. El lugar óptimo de funcionamiento de la máquina es la superficie de hormigón no cubierta o cubierta con una capa muy fina de material no conductor.
5.4 Instalación en el lugar de funcionamiento
5.4.1 Instalación en el lugar de funcionamiento
ATENCIÓN: El fabricante recomienda encarecidamente instalar la máquina sólo en entornos industriales.
La máquina objeto de este Manual de Operación y Mantenimiento ha sido diseñada y fabricada para trabajar en el entorno industrial para el procesamiento de cintas transportadoras.
Las condiciones específicas de funcionamiento de los dispositivos, es decir, la elevada humedad del aire, las altas temperaturas, el vapor y el polvo, han sido tenidas en cuenta por los diseñadores de la máquina y no afectan a su funcionamiento, sino que determinan requisitos más estrictos relativos a la ejecución de los programas preventivos.
La máquina no puede ser utilizada en atmósferas potencialmente explosivas, atmósferas muy polvorientas, ambientes con alta humedad y/o alta temperatura y presencia de vapores agresivos (ácidos, básicos, orgánicos o inorgánicos, con impacto potencial o factualmente corrosivo).
La temperatura del ambiente de trabajo debe oscilar entre +10º C y +40º C y la humedad relativa: entre 30% y 90%. No se permite la condensación de humedad atmosférica ni de sustancias agresivas en la superficie de la máquina (ni en ninguno de sus componentes).
Se requiere que la amplitud de temperatura a largo plazo durante el día en la sala de operaciones del generador no supere los 10º C y en el caso de humedad relativa: 10%.
La cláusula anterior no se aplica a los medios o sustancias utilizados para el engrase, conservación o sustancias no agresivas utilizadas en el curso de la producción / funcionamiento del dispositivo.
ATENCIÓN: Si existe una gran diferencia entre la temperatura exterior y la temperatura de la habitación donde está instalada la máquina, el aparato debe ponerse en marcha transcurridas 24 horas desde su montaje en la habitación.
5.4.2 Iluminación
Los requisitos relativos a la intensidad luminosa mínima establecen que, en la zona de funcionamiento horizontal, la iluminancia que puede aceptarse en las habitaciones en las que las personas permanecen durante un tiempo prolongado, independientemente de que se realicen actividades visuales, debe ser de 300 lx.
En el caso de actividades visuales cuyo nivel de dificultad sea superior a la media y cuando se requiera una gran comodidad de visión, así como cuando la mayoría de los operadores tengan más de 40 años, la intensidad luminosa requerida deberá ser superior a la mínima, es decir, al menos 500 lx.
5.4.3 Ruido
La máquina no genera ruido de un nivel que requiera el uso de medios o dispositivos de protección del personal.
No obstante, hay que tener en cuenta que cada entorno de trabajo tiene sus propias emisiones sonoras, que pueden repercutir en el nivel de ruido emitido por la máquina durante su funcionamiento.
5.5 Parámetros de conexión
5.5.1 Energía eléctrica
Conexión: 3 x 480V; 50Hz (3P+N+PE), protección contra sobrecorriente con propiedades retardadas. La instalación del Cliente debe garantizar medidas de protección contra descargas eléctricas conformes a la norma EN 60204-1:2001.
ATENCIÓN: Compruebe siempre la tensión del filamento después de instalar el tubo; consulte los datos técnicos del tubo.
5.5.2 Aire comprimido
Presión: 0,4 - 0,8 MPa, clase de limpieza exigida según ISO8573-1 4-4-4, consumo: 70 nl por ciclo.
ATENCIÓN: Si la presión en el sistema del usuario final es superior a 0,8 MPa, debe reducirse a unos 0,6 MPa con una válvula reductora montada en la conexión de la máquina de soldar.
5.6 Parámetros de conexión
Dependiendo de la complejidad del sistema y de las cualificaciones y licencias de los empleados, la conexión de la máquina de soldar en el lugar de su funcionamiento la realizan personas seleccionadas por el Ordenante o trabajadores del servicio técnico del Fabricante, en colaboración con el personal del Ordenante, por un precio adicional o de forma gratuita, lo que siempre se acuerda antes de la entrega de la máquina al Ordenante desde el lugar del Fabricante.
Siempre es necesario comprobar si todas las conexiones se han realizado de acuerdo con la documentación del aparato.
Hay que señalar que las tareas mencionadas requieren una cualificación adecuada del personal, incluidas las licencias pertinentes expedidas por los organismos competentes.
Se aplica tanto a las cualificaciones especializadas como a los cursos de formación finalizados y válidos en materia de salud y seguridad en el trabajo, incluidos en particular los riesgos que entrañan esas tareas.
6.0 Funcionamiento
6.1 Preparación de la máquina para el funcionamiento - Primera puesta en marcha
ATENCIÓN: Para utilizar la máquina de forma óptima y segura, lea atentamente y siga todas las instrucciones incluidas en este Manual de Operación y Mantenimiento.
ESTÁ PROHIBIDO ejecutar cualquier trabajo en la máquina de soldar por personas sin estar previamente formadas en el servicio de máquinas de alta frecuencia y normas de Seguridad Industrial con la especial consideración del posible riesgo procedente de la máquina.
Siempre que se hayan cumplido todos los requisitos de instalación y se hayan realizado las tareas descritas en el punto 5, estamos preparados para poner en marcha la máquina de soldar por primera vez en el entorno de producción del centro del ordenante.
ATENCIÓN: La primera puesta en marcha de la máquina debe realizarse en presencia y bajo la supervisión de los representantes del Fabricante.
6.2 Requisitos de funcionamiento - Instrucciones y directrices generales
Todos los ajustes y la calibración necesarios para el correcto funcionamiento de los parámetros del dispositivo han sido realizados por el Fabricante durante los procedimientos de montaje y pruebas internas. La conformidad general con los requisitos técnicos contractuales y el correcto funcionamiento de la máquina se confirman durante la aceptación técnica que tiene lugar en las instalaciones del Fabricante, en presencia de un representante del Ordenante y utilizando materias primas originales entregadas por el Ordenante para las pruebas.
ATENCIÓN: Debido a las propiedades específicas de los aparatos que emiten energía de alta frecuencia, es necesario realizar determinadas mediciones en el lugar de funcionamiento del aparato en el emplazamiento del Ordenante. Por la misma razón, es muy importante que el aparato tenga un lugar fijo de funcionamiento.
ANTES DE LA OPERACIÓN ES ABSOLUTAMENTE NECESARIO CONTROLAR:
- Eficacia de las medidas de protección contra descargas eléctricas;
- Tensión de alimentación - valor y corrección de la conexión de las fases;
- Sentido de giro del motor (si procede);
- Tensión de la lámpara de filamento incandescente;
ATENCIÓN: La tensión de la lámpara debe ser la misma que se especifica en la ficha técnica del producto - es posible ajustarla mediante derivaciones en el primario del transformador de incandescencia.
ATENCIÓN: Debido al carácter específico del dispositivo, siempre es necesario advertir e informar al personal sobre la alta tensión de alimentación del ánodo de la lámpara y el riesgo potencial de descarga eléctrica mortal por corriente eléctrica de la tensión de hasta 8000 VDC.
ATENCIÓN: La lámpara debe precalentarse durante aproximadamente una hora después de la instalación.
- Posición del soporte a la base de la mesa de trabajo;
- Emisión de campo electromagnético - después del ajuste de los parámetros de soldadura, durante el proceso de soldadura;
ATENCIÓN: La máquina de soldadura de alta frecuencia es una fuente de radiación electromagnética no iónica. Después de la instalación de la máquina en el lugar del comprador, la medición de la radiación no iónica se debe hacer. Las mediciones de radiación deben ser realizadas por una empresa autorizada.
ATENCIÓN: La máquina debe trabajar en un lugar de trabajo firme, ya que la transposición requiere una nueva medición de la intensidad de la radiación no iónica.
ATENCIÓN: Está prohibido que las personas con marcapasos implantado permanezcan en la zona de radiación no iónica activa.
ATENCIÓN: El Fabricante sugiere no emplear a ninguna mujer embarazada o en período de lactancia en la zona de radiación no iónica activa.
IMPORTANTE: Si los circuitos de alta tensión se han conectado accidentalmente al desconectar el ánodo o la lámpara del generador está defectuosa, los condensadores del filtro de alta tensión deben descargarse cortocircuitándolos con la carcasa durante muy poco tiempo.
ATENCIÓN: Todas las actividades durante la puesta en marcha y las mediciones, cuando el nivel de seguridad es más bajo (pantallas de protección abiertas, interruptores de llave bloqueados), deben llevar el menor tiempo posible, y el nivel de seguridad de funcionamiento completo de la máquina debe garantizarse lo más rápidamente posible.
ATENCIÓN: Todas las actividades de control y medición deben realizarse después de comprobar si los interruptores para el ajuste de la tensión anódica están en posición 0 - OFF (no se aplica a la medición de la emisión del campo electromagnético).
ATENCIÓN: Todas las actividades de control y medición deben ser realizadas exclusivamente por personal autorizado.
SIEMPRE ESTÁ PROHIBIDO iniciar el proceso de soldadura, es decir, encender la alta tensión de la lámpara, que inicia la tensión de alta frecuencia en el soporte aislado del electrodo, cuando el nivel de seguridad del funcionamiento del aparato es reducido.
La máquina está adaptada para trabajar en ciclo automático. El modo automático es el modo de funcionamiento estándar del aparato durante el proceso de producción.
La máquina de soldadura de alta frecuencia permite el funcionamiento en modo manual para realizar ajustes.
Los operarios de las máquinas deben llevar siempre ropa de trabajo estándar y calzado antideslizante.
El entorno de trabajo del aparato, el suelo y los soportes y asideros manuales deben estar siempre limpios y exentos de cualquier tipo de contaminación, grasa o barro, para reducir al mínimo posible el riesgo de resbalones o caídas.
No utilice nunca la máquina de trabajo sin los elementos de protección fijos o móviles. Compruebe periódicamente si todas las pantallas de protección y todos los demás elementos de protección están bien montados y funcionan correctamente.
Sólo las personas autorizadas, debidamente formadas en el manejo de la máquina y en Prevención de Riesgos Laborales, pueden tener contacto directo con la máquina.
Cada operador del aparato debe ser instruido sobre las funciones de los elementos de protección de la máquina y su correcta utilización.
En la zona que rodea el aparato (aproximadamente 1,5 m alrededor del generador y la prensa) no puede haber objetos que puedan interferir en el funcionamiento del aparato. Esta zona debe mantenerse limpia y disponer de una iluminación adecuada.
No utilice nunca los manipuladores de la máquina ni los tubos flexibles como soportes. Recuerde que cualquier movimiento accidental del manipulador del aparato puede iniciar accidentalmente el proceso de soldadura, cambiar parámetros o incluso provocar el fallo de la máquina o dañar sus herramientas.
ESTÁ OBLIGADO a informar al supervisor y/o al personal de tráfico sobre todos y cada uno de los casos de funcionamiento incorrecto del dispositivo.
6.3 Controles e indicadores a disposición del operador
Todos los mandos e indicadores de la soldadora se encuentran fácilmente en su construcción o en su pupitre de control. Antes de ponerse manos a la obra, el operario de la máquina debe familiarizarse con la disposición de los mandos e indicadores de la máquina, así como con las funciones que controlan.
A continuación se adjunta la lista completa de los controles e indicadores mencionados a disposición del operador:
- INTERRUPTOR PRINCIPAL - un interruptor (Fig.3) diseñado para conectar o desconectar el suministro eléctrico. 1-ON significa que el interruptor está encendido, mientras que la posición 0-OFF significa que el interruptor está apagado.
- PANEL HMI - el panel sensible al tacto (Fig.5) debe utilizarse para cambiar los parámetros de ajuste de la máquina y se supone que se convierte en una fuente fiable de información sobre el estado actual de la máquina de soldar. Consulte el capítulo 5 para obtener más información sobre el procedimiento de mantenimiento del panel táctil.
- POWER - indicador que parpadea en blanco cuando la máquina está conectada a la red eléctrica (Fig.5).
- RESTART - el pulsador azul (Fig.5) que debe utilizarse para reiniciar el sistema de control y protección de la máquina siempre que aparezca el mensaje de alarma en el panel HMI.
- HF OFF/ON - un interruptor con el que se puede liberar o retener la corriente de AF (cuando está en OFF significa que no se puede realizar la soldadura HF)
En lo que respecta al procedimiento de soldadura estándar, el HF OFF/ON debe estar en EN posición.Cuando el interruptor HF OFF/ON se coloca en la posición OFF significa que el ciclo de trabajo se puede realizar sin liberar la corriente HF.
- ELECTRODO ARRIBA/ABAJO - un joystick con ayuda del cual se puede subir o bajar el electrodo (Fig.5).
- HF - cuando el indicador parpadea en amarillo significa que el proceso de soldadura HF está activado (Fig.5).
- STOP HF - el pulsador rojo (Fig.5) sirve para desconectar el proceso de soldadura de alta frecuencia.
- START HF - el pulsador rojo (Fig.5) se utiliza para activar el proceso de soldadura de alta frecuencia.
- PARADA DE EMERGENCIA - el pulsador rojo con forma de seta (Fig.5) es un botón que sólo debe pulsarse cuando sea necesario detener inmediatamente las funciones de la máquina o cuando algo relacionado con las funciones de la máquina o el entorno del operario suponga una amenaza para la producción o la seguridad.
El botón de PARADA DE EMERGENCIA no debe utilizarse en exceso, se supone que sólo debe utilizarse en caso de emergencia.
- CORRIENTE DE ÁNODO - el amperímetro del panel (Fig.5) se supone que indica el valor de la intensidad de corriente en el circuito del ánodo La y debe permitir al operario realizar la inspección visual del proceso de soldadura (Las características a plena carga del generador).
- PRESIÓN - manómetro (Fig. 6) se supone que indica el nivel de presión del aire comprimido en el sistema neumático con la ayuda del cual se presiona el electrodo contra la mesa.
- AJUSTE DE PRESIÓN - el botón de ajuste manual de una válvula reductora de presión (fig. 6) es un botón que sirve para ajustar el nivel de presión en el sistema neumático con ayuda del cual se presiona el electrodo contra la mesa. (Tire de la perilla y: una vuelta a la derecha - el nivel de presión debe subir, y una vuelta a la izquierda - el nivel de presión debe bajar);
El nivel de presión del sistema neumático con cuya ayuda se presiona el electrodo contra la mesa nunca supera el nivel de presión que propulsa la máquina.
14. SISTEMA DE PREPARACIÓN DE AIRE COMPRIMIDO - consiste en:
- El terminal de aire comprimido al que debe conectarse la manguera de aire comprimido. La manguera debe suministrar al sistema aire comprimido de 0,4 a 0,8 MPa;
- La válvula de cierre de aire comprimido de accionamiento manual (para abrir la válvula - gírela hacia la izquierda y colóquela en la posición ON; un giro hacia la derecha - la posición OFF - la válvula está cerrada);
- La válvula reductora de presión de accionamiento manual es una válvula que se utiliza para ajustar la presión en el sistema neumático de la máquina (tire de la válvula hacia arriba y gírela: una vuelta a la derecha - mayor presión, una vuelta a la izquierda - menor presión), la presión nominal de funcionamiento de la máquina asciende a 0,6 MPa;
El nivel de presión del sistema neumático nunca supera el nivel de presión que propulsa la máquina.
- El filtro de aire comprimido junto con el mecanismo de liberación del agua de condensación;
- El manómetro que indica el nivel de presión en el sistema de aire comprimido de la máquina;
- El color rojo indica fallo y al mismo tiempo debe aparecer el mensaje de alarma en el panel táctil de la HMI.
Los masajes de alarma se borran y la luz roja de la columna luminosa de señalización deja de parpadear cuando se pulsa el botón botón RESTART. En caso de que los esfuerzos hayan sido en vano y el mensaje de alarma no se haya borrado al pulsar el botón RESTART, puede significar que la causa del fallo aún no se ha eliminado. Para más información sobre los mensajes de alarma, véase el capítulo 0.
- El color naranja indica que la soldadora de alta frecuencia comienza a funcionar.
- El color verde indica que la máquina está lista para trabajar.
Fig.9. Las teclas del interruptor de pedal:,
17. ELECTRODO ABAJO - un interruptor-llave de pie es una herramienta utilizada para bajar el electrodo.

El procedimiento de ajuste adecuado del sistema de control de altura:
- Coloque el electrodo elegido en el soporte y cierre la HMI Soporte → Opciones → Electrodo → Cerrado,
- Coloque el material en la mesa de trabajo, como para soldar,
- Baje el soporte con el electrodo sobre el material (de forma que el electrodo sólo toque el material sin añadir ninguna fuerza de presión) y déjelo,
- Aflojar dos tornillos de apriete que sujetan el final de carrera y cuando estén sueltos, mover el final de carrera de tal manera que su rodillo debe estar en el indicador de altura del electrodo (Fig.9), luego desenroscar los tornillos de apriete que sujetaban el final de carrera.
- Levante el soporte del electrodo hasta su posición superior,
- Baje el soporte del electrodo, presiónelo contra el material y compruebe si el rodillo interruptor se detiene en el indicador de altura del electrodo. Si se pone en práctica el sistema de protección contra el apriete y, como resultado, el electrodo se eleva hasta su posición superior, significa que es necesario reajustar la posición inferior del interruptor de fin de carrera.
¡ATENCIÓN! Queda terminantemente prohibida la manipulación con el final de carrera que indica la posición inferior del electrodo excluyendo la citada anteriormente. La inobservancia de la advertencia del fabricante puede provocar una avería grave de la máquina y, como consecuencia, graves lesiones corporales.
Fig.10. Final de carrera que indica la posición inferior del electrodo.
6.5 Programación y manejo del panel táctil HMI
¡ATENCIÓN! Cada valor del parámetro representado en los gráficos de este manual se toma al azar y debe ser ignorado por el operador de la máquina. Los valores de los parámetros deben derivarse de la experiencia práctica del usuario, ya que pueden variar profundamente en función del tipo de material soldado o de la instrumentación implementada.
En el panel HMI, todos los valores editables de los parámetros se muestran sobre un fondo de color blanco. Para visualizar un parámetro, el usuario debe pulsar su valor y, como resultado, se abrirá el teclado en pantalla. Los datos pueden guardarse pulsando la tecla Intro.
6.5.1 Conexión a la fuente de alimentación
Poco después de conectar la máquina a una fuente de alimentación, en la pantalla de la HMI aparece una ventana de alarma con el siguiente mensaje:
PARADA DE EMERGENCIA
De acuerdo con esta situación, la máquina necesita ser reiniciada por lo que se debe pulsar la tecla azul RESTART . A continuación hay que esperar 30 segundos hasta que la máquina esté lista para trabajar y entre en modo de espera que conocemos por los siguientes hechos: un indicador luminoso en la columna de señalización luminosa parpadea en verde y la barra de progreso visualizada en la ventana principal de la HMI parpadea en verde. En caso de que el mensaje de alarma no desaparezca de la pantalla de la HMI, consulte el capítulo 0.
6.5.2 Mensajes de alarma
Cuando se produce un fallo en la máquina o cuando se activa uno de los sistemas de protección o cuando se detectan otras anomalías en el funcionamiento de la máquina, se muestra uno de los mensajes de alarma en el panel táctil de la HMI. Todos los mensajes de alarma se borran con la ayuda de la tecla RESTART .
Los tipos de masajes con alarma:
PARADA DE EMERGENCIA - este tipo de mensaje se muestra cuando:
- la máquina está encendida - el circuito de seguridad de la máquina debe comprobarse siempre que se pulse la tecla RESTART,
- se ha pulsado el botón rojo de PARADA DE EMERGENCIA con cabeza de seta y se ha atascado. Es necesario desatascarlo girando su cabeza hacia la derecha.
- uno de los escudos fue retirado - los escudos están equipados con los interruptores de llave que se encienden por sí mismos sólo si los escudos están debidamente colocados y apretados,
COMPRUEBE EL CIRCUITO DE REARME DEL RELÉ DE SEGURIDAD - significa que probablemente se ha dañado el circuito de seguridad de la máquina. En tal caso, póngase en contacto con el servicio técnico del fabricante.
AVERÍA DE LA VÁLVULA DE SEGURIDAD - significa que se ha producido una irregularidad en la acción de la válvula que eleva el electrodo a su posición superior, como en el caso de una avería. En tal caso, debe ponerse en contacto con el servicio del fabricante.
PRESIÓN DE AIRE BAJA EN LOS CILINDROS DE SOPORTE - significa que la presión de aire en los servomotores de soporte del electrodo es demasiado baja, lo que puede provocar un descenso rápido del electrodo y que éste golpee el banco. Es necesario ajustar la presión del aire comprimido en el circuito de estos servomotores.
PARÁMETROS DE SOLDADURA NO ALCANZADOS - el software de control de la máquina incluye un algoritmo que comprueba si cada soldadura parcial se ha realizado correctamente. Si durante la soldadura no se han alcanzado los parámetros establecidos o si se ha detenido la soldadura antes de finalizar la tarea, se mostrará el mensaje anterior. A continuación, se comprobará la calidad de la soldadura y, si no es satisfactoria, deberá repetirse la tarea.
TEMPERATURA DEL ELECTRODO - este mensaje indica que se ha superado la temperatura máxima admisible del electrodo (80oC) - la máquina se desactivará en modo de emergencia. Debe esperar a que el electrodo se enfríe y comprobar entonces si el ajuste de temperatura del regulador de temperatura es demasiado alto. Otra posibilidad es que se haya averiado el circuito de calentamiento del electrodo. En tal caso, deberá ponerse en contacto con el servicio técnico del fabricante.
TEMPERATURA DEL TUBO - este tipo de masaje significa que no existe la refrigeración del tubo de onda viajera o que se produce un fallo en el sistema de refrigeración y se muestra cuando:
- los fusibles que deben proteger el circuito de alimentación del ventilador que debe enfriar el tubo de ondas viajeras están desconectados;
- el contactor que se supone que activa el ventilador que debe enfriar el tubo está apagado o dañado;
- el sistema de protección térmica del tubo se pone en funcionamiento, lo que significa que el tubo de ondas viajeras se ha calentado a una temperatura demasiado alta y, como resultado, se ha desoldado la chaveta de la banda del tubo que estaba conectada al interruptor de fin de carrera mediante un cordón.
Fig.11. El sistema de protección térmica del tubo.
- Se suelda una chaveta a la banda del tubo con la ayuda de una soldadura de punto de fusión mucho más bajo que aquel en el que el tubo se sobrecalentó (se dañó). Si la temperatura de la lámpara aumenta demasiado, la chaveta se saldrá de la banda y, como resultado, se disparará el interruptor de límite, al mismo tiempo que aparecerá el mensaje de alarma y se cortará el suministro de energía para el resplandor del tubo. Entonces deberá eliminarse la causa del sobrecalentamiento.
¡ATENCIÓN! El cable no debe sujetarse a ninguna otra parte de la máquina, salvo a la chaveta de la banda que se ha atornillado al tubo. La inobservancia de la advertencia citada puede ocasionar el bloqueo del final de carrera, lo que puede provocar el sobrecalentamiento del tubo de la onda viajera y, como consecuencia de ello, su deterioro.
If the cotter pin gets separated from the band than the band should be taken off from the tube, the pin should be soldered to the band with the standard solder used in electronic engineering (Melting point < 190oC) para que la pieza reparada pudiera volver a fijarse al tubo.
El sobrecalentamiento del tubo puede ser causado por:
- la suciedad encontrada en el generador o en el radiador tubular;
- el fallo del ventilador de refrigeración del tubo o el fallo del sistema de alimentación del ventilador;
- la obstrucción de los orificios de ventilación de la máquina o por la excesiva cantidad de tierra recogida por los filtros instalados en los orificios de ventilación;
- la temperatura ambiente excesiva.
ANTIFLASH - este tipo de masaje significa que el sistema de protección contra un arco-sobre durante la soldadura se disparó - debido a este mensaje asegúrese de que ni la almohadilla aislante, material soldado ni el electrodo de soldadura no habían sido dañados.
SOBRECARGA DE ÁNODO - este mensaje significa que se ha superado el límite de elevación de ánodo, por lo que es necesario ajustar los parámetros que se aplican a la potencia liberada en la soldadura.
SOBRECARGA DE RED - este mensaje significa que se ha superado el límite de subida de red, por lo que es necesario ajustar los parámetros que se aplican a la potencia liberada en soldadura.
PRESIÓN DE AIRE BAJA - este mensaje significa que hay falta de presión de aire o que el nivel de presión de aire es demasiado bajo en el sistema neumático. Asegúrese de que la manguera que suministra el aire comprimido está conectada a la máquina o de que el nivel de aire comprimido es adecuado y, a continuación, con la ayuda del regulador de la válvula reductora de presión que se puede encontrar en el sistema de preparación de aire comprimido, ajuste la presión en la máquina al nivel adecuado.POSICIÓN DEL CONDENSADOR DE ARRANQUE NO ALCANZADA - el mensaje aparecerá si los condensadores no alcanzan la posición preestablecida en 30 segundos. Compruebe el accionamiento de los condensadores.
EL ELECTRODO NO ESTÁ EN LA POSICIÓN INFERIOR - se visualizará un mensaje de alarma si se pulsa el botón START y el electrodo no está en la posición inferior. Baje el electrodo.En la parte superior de la pantalla táctil de la HMI hay un menú con el que el usuario puede elegir una de las cinco ventanas virtuales principales, a saber:
- Pantalla principal
- Base de datos de recetas
- Ajuste de potencia
- Gráfico de trabajo
- Menú de servicio
6.5.4 Pantalla principal
Fig.12. Pantalla principal.
Receta - bajo este nombre se puede encontrar un grupo de parámetros que se aplican al ciclo de trabajo. Una vez establecidos los parámetros de soldadura para el tipo concreto de producto derivados de la experiencia práctica (los valores de los parámetros dependen en gran medida del tamaño de la soldadura, el tamaño del material soldado y la forma del electrodo), deben introducirse en el sistema y guardarse con el nombre de la receta.
Además, junto al nombre de cada parámetro aparecen dos valores en la pantalla de la HMI. El primero (sobre fondo azul) es el valor del parámetro de funcionamiento actual visualizado en tiempo real, el segundo (sobre fondo blanco) es el valor ajustado procedente de la receta de producción o de los datos del operador.
En caso de necesidad, el operador siempre puede pulsar el dígito sobre el fondo blanco y cambiar su valor. El valor del parámetro de funcionamiento actual se actualizará de inmediato, aunque el cambio no afectará a la receta ejecutada.
Para guardar en una receta los cambios realizados en la pantalla principal, pulse el botón GUARDAR RECETA para copiar los parámetros de la pantalla principal en la barra Editar receta de la ventana Base de datos de recetas. Los parámetros copiados pueden guardarse como una nueva receta utilizando el botón Crear nueva o pueden utilizarse para actualizar una receta existente utilizando el botón Actualizar.
Nombre: - El nombre de la receta ejecutada a efectos de producción.
Potencia inicial – this parameter indicates the position (capacity) of the output capacitor found in the generator; the anode current intensity in the initial phase of high frequency weld strongly depends on the value of this parameter. (Parameter expressed in percentage values, where 0% indicates the lowest level of capacity - the lowest level of anode current intensity and 100% indicates the highest level of capacity - the highest level of anode current intensity.)
El valor del parámetro Potencia inicial y el valor de la corriente anódica (potencia liberada en el material) no dependen linealmente, por lo que deben tomarse las medidas de precaución adecuadas al ajustar los valores de este parámetro.
El valor actual del parámetro Potencia inicial y el valor del parámetro Ajuste son iguales entre sí sólo en la fase inicial del procedimiento de soldadura. Cuando se inicia el procedimiento, la posición del condensador de salida se ajusta automáticamente para alcanzar la potencia de funcionamiento.
Potencia de funcionamiento - este parámetro indica la corriente de ánodo Ia utilizada para soldar. (Parámetro expresado en valores de amperios que van de 0 a 4 A.)
Los valores en color verde en la escala del medidor de corriente anódica indican los valores aceptables de la corriente anódica Ia.
Cuando se inicia el procedimiento de soldadura, el condensador de salida (potencia inicial) se ajusta automáticamente para alcanzar la potencia de funcionamiento.
Tiempo de retardo - este parámetro indica el tiempo durante el cual el electrodo se ha adherido al material soldado antes de iniciarse la soldadura. (Parámetro expresado en segundos con valores comprendidos entre 0 y 99 s).
Tiempo de soldadura - este parámetro significa el tiempo que tarda la máquina en procesar la soldadura de alta frecuencia. (Parámetro expresado en valores de segundos que van de 0 a 99 s .)
Tiempo de enfriamiento - este parámetro indica el tiempo en el que el electrodo ha sido presionado contra el material soldado tras finalizar la soldadura - el material se enfría al ser presionado contra la mesa. (Parámetro expresado en segundos valores que van de 0 a 99 s .).
Nivel de potencia - es el ajuste principal de la potencia de la máquina; el ajuste se realiza modificando la tensión del ánodo Ua en el rango de 1 a 6, donde 1 es potencia baja y 6 es potencia máxima:
0 - el transformador de ánodo está desconectado;
1 - Ua = 3,4kV;
2 - Ua = 3,95kV;
3 - Ua = 4,75kV;
4 - Ua = 5,87kV;
5 - Ua = 6,85kV;
6 - Ua = 8,2kV;
¡ATENCIÓN! Es importante recordar que a pesar de que los parámetros arriba mencionados pueden ser guardados bajo el nombre de la receta en el panel táctil HMI también existen otros dos parámetros como son: PRESIÓN y TEMPERATURA DEL ELECTRODO que deben ser ajustados manualmente.
Los parámetros de la receta que aparecen en el recuadro amarillo (AJUSTE MANUAL) son sólo una información para el operador que, mientras lee los parámetros en la pantalla táctil, debe cambiar manualmente los ajustes en el lateral de la máquina. El cambio de este ajuste en la pantalla no afecta a los ajustes de la máquina.
PRESIÓN - el parámetro indica la presión del aire comprimido en el sistema neumático de sujeción del electrodo expresada en bares; el parámetro determina la fuerza descendente del electrodo en relación con el material durante la soldadura.
Opciones:
Electrodo Abierto / Cerrado
Un candado abierto sobre fondo rojo indica que el electrodo de soldadura no estaba cerrado en su soporte, al pulsar el candado gris cerrado el soporte quedará cerrado.
Cuando el portaelectrodos está abierto es posible el cambio de electrodo todas las demás funciones no están disponibles.
Además, cuando parpadea el mensaje ATENCIÓN, ELECTRODO ABIERTO, también significa que el portaelectrodos está abierto.
Un candado cerrado sobre fondo verde indica que el electrodo de soldadura está cerrado en su soporte, al pulsar sobre el candado gris abierto el soporte estará abierto.
¡ATENCIÓN! El portaelectrodos no debe cerrarse sin un electrodo en su interior.
¡ATENCIÓN! El portaelectrodos no debe cerrarse sin un electrodo en su interior.
Luz apagada/encendida
Una lámpara que no brilla sobre el fondo rojo indica que la iluminación de la mesa de trabajo en la zona de soldadura está apagada, al pulsar la lámpara que brilla en gris, la iluminación se encenderá.
Una lámpara encendida sobre el fondo verde indica que la iluminación de la mesa de trabajo en la zona de soldadura está encendida; al pulsar la lámpara gris, la iluminación se apagará.
Modo de trabajo Corriente/Hora
Un circuito eléctrico sobre fondo verde indica que la máquina trabaja en el modo de soldadura de tipo corriente, pulsar el reloj gris significa que la máquina entrará en el modo de soldadura de tipo tiempo. El modo de soldadura de tipo corriente significa que el contador de la máquina empieza a contar el tiempo de soldadura de alta frecuencia que se introdujo en el parámetro Tiempo de soldadura tan pronto como la máquina obtiene el valor apropiado de la corriente del ánodo, que debe ser superior o igual al valor introducido en el parámetro Corriente de trabajo. Dicho de otro modo, en el modo de soldadura de tipo corriente el tiempo de soldadura es igual a la suma del valor del tiempo que la máquina tarda en producir la corriente anódica (el valor introducido en el parámetro Corriente de trabajo) y el valor del tiempo introducido en el parámetro Tiempo de soldadura.
Si la máquina no consigue producir la potencia de funcionamiento en 25 segundos, el ciclo de trabajo se interrumpirá.
A reloj sobre fondo verde indica que la máquina trabaja en el modo de soldadura de tipo tiempo, pulsando el circuito eléctrico gris significa que la máquina entrará en el modo de soldadura de tipo corriente. El modo de soldadura de tipo tiempo significa que el tiempo de soldadura de alta frecuencia es igual al valor introducido en el parámetro de la receta bajo el nombre de Tiempo de soldadura.
Cabe señalar que en el modo de soldadura de tipo de tiempo, el ciclo de trabajo puede ser ejecutado incluso si la máquina no logró producir la potencia de funcionamiento como resultado la soldadura lograda puede ser de fuerza irregular.
el pulsador min indica que la máquina está trabajando en modo de regulación automática limitada del condensador de salida; presionando el pulsador max se pasa al modo de regulación automática completa del condensador de salida. La modalidad min significa que, durante la soldadura, el condensador de salida se regula sólo cuando la corriente anódica supera el valor introducido en el parámetro Power max .
el pulsador max indica que la máquina trabaja en modo de regulación automática total del condensador de salida; el pulsador min la pone en modo de regulación automática limitada del condensador. El modo max significa que, durante la soldadura, el condensador de salida se ajusta automáticamente para que la corriente anódica se sitúe en el nivel establecido en el parámetro Potencia de funcionamiento.
Ciclos realizados: - significa el contador de los ciclos de soldadura ejecutados en la máquina. Si el operario mantiene pulsada la tecla Reiniciar contador durante 3 segundos, el contador se reiniciará.
MENSAJES DE ALARMA INDICANDO: NO LISTO PARA INICIAR CICLO DE SOLDADURA:
ATENCIÓN, ELECTRODO ABIERTO - indica que el mango del electrodo está abierto. Instale correctamente el electrodo de soldadura y cierre el asa: HMI → Pantalla principal→ Electrodo → cerrado .
NO LISTO - indica que la máquina no se ha reiniciado correctamente y que no se ha producido un arranque de 30 segundos. Pulse el botón RESTART en el panel de control.
6.5.5 Base de datos de recetas
Fig.13. Base de datos de recetas.
Todas las recetas guardadas en la tarjeta de memoria de la IHM se listan en forma de gráfico. Cada fila contiene una receta y cada columna contiene uno de los parámetros de la receta. La descripción detallada de los parámetros se ha citado en el capítulo anterior. El gráfico puede contener un número ilimitado de recetas. Debajo de la tabla hay una fila titulada Editar receta (con fondo blanco) que se utiliza para editar y crear recetas.
NUEVA RECETA
Para crear una nueva receta, rellene todas las casillas de la fila Editar receta y pulse la tecla Crear nueva . El sistema debería añadir la receta recién creada a la lista existente y mostrarla en la nueva fila del gráfico.
Para guardar los cambios realizados en una receta mediante la función Pantalla principal, pulse el botón GUARDAR RECETA para copiar los parámetros de la pantalla principal en la barra Editar receta de la ventana Base de datos de recetas. Los parámetros copiados pueden guardarse como una nueva receta utilizando el botón Crear nueva o pueden utilizarse para actualizar una receta existente utilizando el botón Actualizar.
EDICIÓN DE RECETAS
Para editar una receta, haga clic en el nombre de la receta en la lista de recetas (la receta seleccionada se resaltará en amarillo y se mostrará en la fila Editar receta ). Para cambiar el valor de un parámetro en la fila Editar receta, haga clic en el recuadro blanco e introduzca un nuevo valor. Una vez completado el procedimiento de edición, hay que pulsar la tecla Actualizar y como resultado los cambios introducidos en la receta indicada serán aceptados, guardados y almacenados.
PROCEDIMIENTO DE SUPRESIÓN
Para borrar una receta, haga clic en el nombre de la receta de la lista de recetas (la receta seleccionada debe aparecer resaltada en amarillo en la fila Editar receta ) y pulse Borrar.
PROCEDIMIENTO DE SELECCIÓN DE RECETAS
Para llevar a cabo el procedimiento de selección de recetas para la producción, seleccione de la lista de recetas la receta con los valores requeridos para el ciclo de trabajo (la receta seleccionada debe resaltarse en amarillo y mostrarse en la fila Editar receta ) y, a continuación, haga clic en la tecla Cargar para producción. Como resultado, la receta se cargará en el sistema y se preparará para su uso en la producción actual con sus parámetros mostrados en la ventana de la pantalla principal.
PROCEDIMIENTO DE CLASIFICACIÓN
Las recetas utilizadas para la producción se enumeran por orden alfabético. La barra de desplazamiento vertical que permite al operador visualizar el gráfico con mayor fluidez aparecerá en la parte derecha del gráfico cuando entre en el sistema un mayor número de recetas. El sistema permite al operador ordenar las recetas por nombre o por cada valor de un parámetro (de forma ascendente o descendente). Para realizar una ordenación, busque una fila de cuadros negros que deben mostrarse en la parte superior del gráfico y haga clic una vez en un cuadro negro situado precisamente sobre una columna con datos que se supone que deben ordenarse. (Si hace clic dos veces, cambiará la dirección de la ordenación).
6.5.6 Ajuste de la potencia
Fig.14. Ajuste de potencia.
Hay dos indicadores en la ventana:
Corriente anódica: indicador de la intensidad de corriente anódica. Indica la intensidad de corriente del ánodo La que debe ser igual a la intensidad de corriente del medidor analógico que se encuentra en el panel de control.
CAPACITADOR - una herramienta que indica la posición del condensador de salida (dentro del rango de 0 a 100%). Con la ayuda de esta herramienta se puede ajustar el nivel adecuado de potencia - por regla general, cuanto mayor sea la capacidad, mayor será la corriente del ánodo La.
Un grupo de teclas bajo el indicador se utiliza para el ajuste del condensador anódico. El ajuste se puede realizar de dos maneras:
AUTO - antes de soldar, el condensador se ajusta automáticamente a la posición correspondiente a los valores inscritos en el parámetro Potencia inicial. Cuando se ejecuta el procedimiento de soldadura, la posición del condensador se ajusta automáticamente para que el nivel de intensidad de corriente del ánodo La pueda aumentar hasta el valor inscrito en el parámetro Potencia de funcionamiento.
Seleccione el modo de ajuste AUTO durante los ciclos de trabajo estándar realizados por la máquina. El modo MANUAL se utiliza para los procedimientos de prueba.
MANUAL - todo el procedimiento de ajuste del condensador se realiza a mano, cuando surge la necesidad el operador puede cambiar la posición del condensador con la ayuda de las teclas "+" o "-" y al mismo tiempo se ajusta la intensidad de la corriente anódica.
6.5.7 Gráfico de trabajo
Fig.15. Gráfico de trabajo.
La pantalla muestra un gráfico que ilustra los cambios en la posición del condensador de salida (línea azul) y los cambios en la corriente del ánodo (línea roja) durante el ciclo de soldadura.
El gráfico muestra los datos registrados en el pasado. A la derecha hay una tabla con los datos, mientras que cada fecha corresponde a un día laborable de la máquina. Para ver los datos de un día determinado, seleccione la fecha correspondiente.
Todos los datos se registran en la memoria del panel HMI. Por cada día de trabajo de la máquina, se guarda un archivo con el nombre de la fecha correspondiente. Es posible copiar los archivos de historial de la memoria del panel táctil a un dispositivo USB y ver los archivos en Excel (véase la sección 6.5.9).
6.5.8 Menú Servicio
Fig.16. Menú Servicio.
En esta ventana se muestran los siguientes datos de origen estadístico:
Recuento de ciclos: es el número total de ciclos de trabajo desde que la máquina se ha encendido por primera vez.
Tiempo de trabajo: es el tiempo total de trabajo de la máquina,
Antiflash - este valor indica cuántas veces, desde el día en que se fabricó la máquina, se activó el sistema de protección contra el arco eléctrico.
Alarma de sobrecarga del án odo - este valor indica cuántas veces, desde el día en que se fabricó la máquina, se superó el nivel máximo de intensidad de corriente en el circuito del ánodo y, en consecuencia, cuántas veces se activó el mecanismo de protección contra la sobrecarga del ánodo.
Alarma de sobrecarga de red - este valor indica cuántas veces, desde el día en que se fabricó la máquina, se superó el nivel máximo de intensidad de corriente en el circuito de red durante la soldadura y, en consecuencia, cuántas veces se activó el mecanismo de protección contra la sobrecarga de red.
Alarma de temperatura del tubo : este valor indica cuántas veces, desde el día en que se fabricó la máquina, se activó automáticamente el sistema de protección térmica del tubo.
Los parámetros enumerados a continuación sólo están disponibles para los técnicos de servicio del fabricante, por lo que se requiere una contraseña para editarlos.
Potencia máxima = Potencia de funcionamiento + - este parámetro indica el valor máximo de intensidad de corriente que puede superar el valor de Límite de potencia de funcionamiento para iniciar el procedimiento automático de descenso de corriente anódica realizado por el condensador de salida (parámetro expresado en valores de amperios dentro del rango de 0 a 1A).
Tiempo de retardo de presión - este valor indica el tiempo que transcurre desde el momento en que se dispara el final de carrera inferior (que indica la posición inferior del electrodo) hasta el momento en que se presiona el electrodo contra el material con toda su fuerza.
Tiempo de apertura de la prensa - este valor indica el tiempo que consume el electrodo para alcanzar su posición superior. La duración del tiempo es un valor ajustable y se corresponde en gran medida con el ajuste de altura del electrodo, lo que significa que el electrodo necesita muy poco tiempo para alcanzar un nivel de altura ligeramente insignificante y consume considerablemente más tiempo cuando se supone que debe llegar más alto.
El botón Historial de alar mas - abre la pantalla que muestra el historial guardado de las alarmas que se han producido en la máquina en el último año. El historial de alarmas se guarda en la memoria del panel HMI. El historial de alarmas de cada día se guarda como un archivo con el nombre EL data, por ejemplo EL_20131122. Es posible copiar los archivos del historial desde la memoria del panel táctil a un dispositivo USB y visualizar los archivos en Excel (véase el apartado 6.5.9).
Los mensajes de alarma suelen guardarse en el idioma seleccionado en el menú de servicio.
Luces de control que muestran el estado de los sensores de la máquina (Sensores):
Electrodo abajo - la luz de control, encendida, señala que el final de carrera que indica la posición del electrodo inferior está conectado;
Presionando - la luz de control, apagada, señala que el electrodo ha encontrado resistencia al bajar (por ejemplo, está presionado contra el banco) y el interruptor de fin de carrera se apaga;
6.5.9 Datos archivados en la memoria del panel táctil de la IHM- Inserte un dispositivo de memoria USB en el puerto del panel táctil HMI.
- En la pantalla del panel HMI aparecerá una ventana, pulse Cargar.
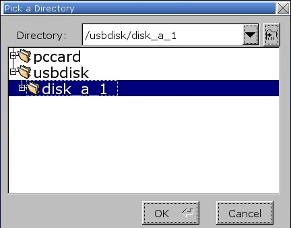
4. Abra la carpeta"usbdisk", seleccione la carpeta"disk_a_1" y pulse Aceptar.
- registro de datos" →"trend" - la carpeta"trend" contiene archivos con registros de los parámetros de trabajo de la máquina. Cada día se guarda un archivo bajo la fecha correspondiente. Para leer los datos históricos, inserte la memoria USB en el ordenador y, a continuación, en la carpeta "TREND", haga doble clic en el archivo deseado para generar un archivo en formato xls (Excel) con el fin de ver claramente el historial de funcionamiento de la máquina o generar un gráfico para un día determinado. Para generar archivos xls, se necesita el programa gratuito EasyBuider Pro, que puede descargarse de la página web del fabricante del panel HMI: http://www.weintek.com/.
- "eventlog" - la carpeta"eventlog" contiene archivos con registros del historial de alarmas que se han producido durante el funcionamiento de la máquina. El historial de alarmas de cada día se guarda como un archivo denominado EL_data, por ejemplo EL_20131122. Para leer los datos históricos, inserte la memoria USB en el ordenador y, a continuación, haga doble clic en el archivo deseado para generar un archivo en formato xls (Excel) con el fin de ver claramente el historial de alarmas de un día determinado. Para generar archivos xls, se requiere el programa de software gratuito EasyBuider Pro, que debe descargarse de la página web del fabricante del panel HMI: http://www.weintek.com/.
- "recipe" - la carpeta"recipe" contiene dos archivos con recetas copiadas del panel HMI: "db" y"recipe_a.rcp". Los archivos pueden utilizarse como copia de seguridad de las recetas o para guardar las recetas en otro panel táctil HMI. También es posible editar las recetas en el ordenador.
Para editar las recetas, se requiere el programa de software gratuito EasyBuider Pro, que debe descargarse de la página web del fabricante del panel HMI: http://www.weintek.com/.
- Inserte la memoria USB -con las recetas copiadas- en el ordenador y abra el Gestor de Utilidades En la sección Conversión de Datos , elija la aplicación Editor de Bases de Datos de Recetas.
- En la aplicación Editor de bases de datos de recetas , pulse Importar... y seleccione los archivos con las recetas copiadas"db".
- Se abrirá la ventana de edición de recetas.
- Cuando termine la edición, haga clic en Exportar... y guarde el archivo en su ubicación anterior.
Copia de recetas desde una memoria USB:
- Inserte el dispositivo USB en el puerto del panel táctil HMI.
- En la pantalla del panel HMI aparecerá una ventana, haga clic en Descargar.
- En la siguiente ventana, selecciona Descargar archivos del historial, introduce la contraseña: 111111 y haz clic.
- Abra la carpeta"usbdisk", seleccione la carpeta"disk_a_1" y haga clic en Aceptar.
Las recetas se cargarán en la memoria del panel táctil HMI. Apague la máquina y vuelva a encenderla.
6.6 Conexión a la fuente de alimentación
BAJO NINGUNA CIRCUNSTANCIA la máquina debe ser manejada por personal no cualificado. Los operadores de la máquina deben estar familiarizados con las normas de seguridad y salud en el trabajo.
Antes de conectar la máquina a una fuente de alimentación, deben realizarse los siguientes procedimientos:
- asegurarse de que el entorno de trabajo de la máquina (la máquina y su entorno) está limpio y en orden o no hay obstáculos que puedan influir negativamente en el ciclo de trabajo estándar de la máquina; y
- asegurarse de que se prepara la cantidad adecuada de materia prima (probetas); y
- asegurarse de que las papeleras y contenedores para los productos soldados se colocan en el lugar adecuado, pero cerca de la máquina, debido a los requisitos de Bayer aplicables al ciclo de producción, si los hubiera; y
- asegúrese de que todas las protecciones estén debidamente fijadas a la máquina y de que las puertas laterales de una caja de interruptores estén cerradas;







- Levante el electrodo hasta su posición superior.
- Gire el INTERRUPTOR PRINCIPAL a la posición 0-OFF - significa que la máquina está apagada.
- Cierre la válvula manual de cierre del aire comprimido (para realizar el procedimiento - gire la válvula hacia la derecha - posición OFF).
- Poner en orden el entorno de trabajo alrededor de la máquina.
- Tanto el enchufe de alimentación eléctrica como el del sistema de aire comprimido deben desenchufarse en caso de parada prolongada del trabajo (ambos enchufes deben extraerse de las tomas).
6.7 Procedimiento de prueba y ajuste


El procedimiento de prueba y ajuste debe ponerse en práctica cuando:
- la máquina se ha encendido por primera vez,
- la sustitución del utillaje (cuando surja la necesidad),
- se ha completado el procedimiento de mantenimiento,
- los operarios deben familiarizarse con el funcionamiento de la máquina.
Para realizar dicho procedimiento el operador deberá:
1. Vaya al panel sensible al tacto: HMI → Ajuste de potencia ventana → establecer el modo de ajuste del condensador en MANUAL → con la ayuda de "-" y "+"Asegúrese de que el procedimiento de cambio de posición del condensador se realiza sin problemas en cada nivel de potencia que va de 0 a 100%. Una vez finalizado el procedimiento de comprobación, cambie el modo de ajuste del condensador a AUTO
2. Coloque el interruptor HF OFF/ON en la posición OFF.

3. Cargue la receta adecuada desde la memoria del panel táctil: HMI → Ventana de base de datos de recetas → resalte la receta deseada en el gráfico → a continuación, pulse la tecla Cargar para producción o rellene las siguientes casillas de los parámetros del ciclo de soldadura que se encuentran en la pantalla principal:
- Potencia inicial;
- Potencia de funcionamiento;
- Tiempo de retraso;
- Tiempo de soldadura;
- Tiempo de enfriamiento;
- Nivel de potencia;
- Presión (ajuste manual),
Cuando se somete a pruebas un nuevo tipo de material, se recomienda encarecidamente introducir en el sistema los parámetros de los ciclos de soldadura de valores bajos y, a continuación, aumentar gradualmente sus valores hasta conseguir el efecto más deseable de la soldadura.
4. Ajuste el nivel de presión del electrodo que se está utilizando para el proceso de soldadura con la ayuda de la válvula reductora de presión accionada manualmente (AJUSTE DE PRESIÓN).Si el nivel de presión es demasiado alto, el material puede "salirse" por debajo del electrodo, pero cuando el nivel de presión es demasiado bajo, la resistencia de la soldadura puede ser débil.
5. Pulse en el panel HMI: HMI → Pantalla principal → Opciones → Modo de trabajo → tiempo;
6. Asegúrese de que la almohadilla aislante de la mesa de trabajo o del separador de chapa de aluminio esté limpia: no puede estar ni sucia ni dañada mecánicamente en el punto donde el electrodo se presiona contra el material soldado;ATENCIÓN La almohadilla aislante debe colocarse directamente debajo del material soldado, ya que se supone que protege al operario contra un arco eléctrico formado entre el electrodo de soldadura y la mesa de trabajo.
ATENCIÓN Si el separador se ha cubierto con la almohadilla aislante, debe adherirse firmemente a la mesa, de tal forma que no se encuentren impurezas entre el separador y la mesa de trabajo.
7. Preparar el material para la soldadura;
8. Empuje el ELECTRODO ARRIBA/ABAJO joystick hacia abajo que se encuentra en el panel de control y como resultado la máquina debería empezar a bajar el electrodo;
9. Realice el procedimiento de regulación del final de carrera (ver capítulo 0.) ya que el final de carrera indica la posición inferior del electrodo a condición de que se haya puesto en práctica el sistema de protección contra el peligro de apriete debido al cual el electrodo se ha levantado y el mensaje de alarma tal como ELECTRODO DE EMERGENCIA ARRIBA en la pantalla;
10. Empuje el ELECTRODO ARRIBA/ABAJO joystick hacia arriba que se encuentra en el panel de control y, como resultado, la máquina debería empezar a levantar el electrodo;
11. Empuje el ELECTRODO ABAJO y como resultado la máquina debe empezar a bajar el electrodo de soldadura sobre la mesa de trabajo. Cuando el operario pulsa la tecla ELECTRODO ARRIBA la máquina debe empezar a levantar el electrodo;
12. Asegúrese de que la máquina baja y sube el electrodo con suavidad y pruebe el proceso varias veces;
13. Bajar el electrodo de soldadura sobre el material y presionar HF START como resultado, la máquina realiza el ciclo de soldadura automático cuando el generador de alta frecuencia está apagado;
14. Iniciar el proceso de prueba de soldadura tan pronto como se hayan completado con éxito las etapas mencionadas del procedimiento de ajuste;
15. Ajuste el HF OFF/ON cambiar a EN posición;
16. Haga clic en el panel HMI: HMI → Pantalla principal → Opciones → Modo de trabajo → tiempo o actual;
17. Haga clic en el panel HMI: HMI → Pantalla principal → Opciones → Modo de trabajo → min o máx;Consulte el capítulo 0 para obtener más información sobre los modos de soldadura de corriente y tiempo / mín. y máx.
18. Bajar el electrodo con precisión sobre el punto de soldadura;ATENCIÓN El operario puede detener el proceso de soldadura por alta frecuencia en cualquier momento con la ayuda del pulsador HF STOP.
19. Presionar el pulsador HF START y la máquina inicia el ciclo automático de soldadura según los parámetros que se encuentran en la pantalla principal del panel HMI. 20. Controle las indicaciones del medidor de CORRIENTE ANÓDICA - deben aumentar durante el proceso de soldadura y alcanzar los valores indicados en el fondo verde de la escala del medidor;
20. Una vez completado el procedimiento, la calidad de la soldadura debe someterse a una inspección visual. El operario necesita conocimientos prácticos para llevar a cabo este procedimiento con éxito, por lo que se debe solicitar asesoramiento práctico a los técnicos de servicio del fabricante, aunque se recomienda encarecidamente que el procedimiento de puesta en marcha sea realizado por y bajo la estrecha supervisión de personal experimentado contratado por el fabricante.
21. Ajuste los siguientes parámetros de soldadura en función de la calidad de la soldadura (soldada, no soldada, sobrecalentada): - fuerza de prensado - utilizando la válvula de AJUSTE DE PRESIÓN,
- Potencia inicial
- Corriente de funcionamiento
- Tiempo de retardo
- Tiempo de soldadura
- Tiempo de enfriamiento
Nivel de potencia - 22. Asegúrese de que los siguientes parámetros se han sometido a muchas horas de pruebas en relación con: el trabajo con el mismo tipo de material, el ciclo de trabajo y la funcionalidad de la máquina, las normas de ergonomía de la máquina, que son cruciales para evitar lesiones graves durante el ciclo de producción;
- 23. Una vez alcanzados los parámetros de estética y resistencia de la soldadura, los valores deben guardarse como receta: HMI → Pantalla principal → hacer clic en el nombre de la receta → Ventana de base de datos de recetas → introducir el nombre de la receta en la fila titulada Editar receta → pulsar la tecla Crear nueva.

1. Arranque la máquina siguiendo el procedimiento descrito en el capítulo 5.9.



- Potencia inicial;
- Potencia de funcionamiento;
- Tiempo de retraso;
- Tiempo de soldadura;
- Tiempo de enfriamiento
- Nivel de potencia
El portaelectrodos de soldadura está equipado con el sistema automático de sujeción rápida controlado desde el panel táctil HMI. Permite al operario ahorrar tiempo y cambiar el electrodo sin utilizar instrumentos.
ATENCIÓN Tenga en cuenta el peso del electrodo durante el proceso de cambio. Se recomienda encarecidamente que dos personas realicen el cambio de electrodo en caso de que sea grande y pesado. Un manejo inadecuado del electrodo puede provocar que el operario se apriete las manos al extraer el electrodo pesado de la pinza.
Para llevar a cabo el procedimiento de cambio de electrodos, siga los siguientes pasos:
- conectar la máquina a la alimentación eléctrica y neumática - la máquina debe estar preparada para realizar el ciclo de trabajo rutinario (es decir, no deben aparecer los mensajes de alarma y el electrodo debe encontrarse en su posición superior),
- configurado en la pantalla principal del panel: HMI → Opciones → Electrodo → Abrir,
- mueva el electrodo hacia la izquierda o hacia la derecha (depende de la versión de la máquina) - el electrodo debe deslizarse fuera de los soportes;
- deslizar un nuevo electrodo sobre los soportes utilizados para la sujeción, desplazar el electrodo hacia la izquierda o hacia la derecha (depende de la versión de la máquina)
- configurado en la pantalla principal del panel: IHM → Opciones → electrodo →
7.0 Selección de los parámetros de soldadura
Aunque la potencia de salida, la fuerza de la presión y el paralelismo de los electrodos desempeñan un papel sustancial en el procedimiento de soldadura, no se puede pasar por alto el tipo de almohadilla aislante, ya que desempeña un papel igualmente importante en el proceso. La almohadilla aislante debe fabricarse con materiales de bajo factor de pérdida dieléctrica, como placas de vidrio-epoxi, teflón, cartón prensado, tereszpan [cartón prensado laminado con película de poliéster], láminas de fenólico-algodón (TCF), baquelita y similares. El nivel de grosor o dureza de la almohadilla depende de la lámina soldada. Por regla general, cuanto más gruesa sea la lámina, más fina deberá ser la almohadilla bajo el material soldado y viceversa, cuanto más fina sea la lámina, más gruesa deberá ser la almohadilla. Por lo general, el grosor de la almohadilla aislante puede oscilar entre 0,1 y 1,5 mm, aunque el parámetro del grosor de una almohadilla aislante debe derivarse de la propia experiencia práctica del operario, ya que depende del tipo de lámina y de las condiciones de la soldadura aplicada.
ATENCIÓN: La máquina no debe realizar el procedimiento de soldadura sin una almohadilla aislante debajo del electrodo. Debido a la almohadilla aislante aplicada adecuadamente el número de los fenómenos de sobretensión que se forman en la superficie del electrodo se reduce.
Para alcanzar el máximo nivel de productividad con un nivel relativamente bajo de soldaduras defectuosas, el operario de la máquina debe realizar el procedimiento de ajuste de potencia para cada electrodo sustituido. Dicho procedimiento se realiza con la ayuda de los mandos Ua SETTING y el parámetro Operating power.
Una vez ajustada la potencia e iniciado el proceso de soldadura, las indicaciones del amperímetro de CORRIENTE ANÓDICA están sujetas a inspección visual. Cuando las mediciones van en aumento significa que en este momento concreto se inicia el proceso de soldadura. El parámetro del tiempo de soldadura debe corresponder con el valor del parámetro debido al cual el procedimiento de soldadura de alta frecuencia se detendrá como resultado de la parada de la aguja indicadora del amperímetro.
Cuando finaliza el proceso de soldadura, la calidad de la soldadura debe someterse a una inspección visual. Si la calidad de la soldadura es insuficiente, debe aumentarse el nivel de potencia. En caso de que la solución anterior no dé resultados fructíferos, se puede aumentar el parámetro del tiempo. Sin embargo, el valor de la potencia no debe ser demasiado alto, ya que puede dar lugar a productos, aislante y el electrodo de daños causados por un arco de más.
Por regla general, el tiempo de soldadura para los materiales hechos de PVC duro no debe ser superior a 4-5 seg. Según la experiencia del fabricante, los valores más altos de dichos parámetros no influyen en la calidad del cordón obtenido, pero deterioran suficientemente la eficacia del proceso. Si el proceso de soldadura dura más tiempo durante los procedimientos de prueba, significa que es necesario regular el ajuste de potencia.
Para soldar la lámina de PVC, el material debe ser presionado por el electrodo con una fuerza de presión que oscila entre 0,5 y 3 kg/cm2. La medición de la fuerza de presión mientras se selecciona el valor más adecuado llevaría demasiado tiempo y, además, en la práctica este método resultaría inútil. Generalmente, para realizar con éxito el procedimiento de fraguado, el operario necesita notar algunas irregularidades que aparecen durante el procedimiento de soldadura y en el aspecto de la costura. Cuando la presión es demasiado baja se producen las siguientes irregularidades:
- susceptibilidad a las descargas de chispas que se producen entre dos electrodos, ya que el aire, que debería haber sido expulsado, se produce entre dos capas de lámina y, como resultado, se forma una intensidad de corriente irregular;
- aparición de burbujas de aire en la costura;
- apariencia de la resistencia de la costura que es pequeña
Si la presión es especialmente baja, puede producirse algo que suele denominarse "ebullición de la película". Cuando la película se suelda a muy baja presión, puede deformarse y convertirse en un producto espumoso de muy baja resistencia. Aplicar una presión excesiva tampoco es adecuado, ya que puede hacer que la película sea muy fina a lo largo del lugar de la soldadura y, por lo tanto, también dar lugar a una menor resistencia del material soldado. Por lo tanto, se recomienda seguir el principio que dice que el grosor de la película después de la soldadura debe ser igual al menos a la mitad del grosor inicial de ambas capas de película. La aparición y la forma adecuada de la fuga característica que suele formarse a lo largo de ambos bordes del lugar soldado también influyen significativamente en las propiedades de resistencia del material soldado. Si dicha fuga no aparece, suele indicar una resistencia insuficiente del lugar soldado, que puede comprobarse muy fácilmente. La ausencia de la fuga tras el proceso de soldadura puede deberse a la aplicación de una potencia de salida demasiado baja o de una presión insuficiente. Si utiliza electrodos con filo de corte, es muy importante colocar el filo de corte correctamente. Normalmente se supone que el filo del electrodo debe sobresalir del plano de soldadura aproximadamente la mitad del espesor de la película soldada. Para comprobar el funcionamiento del filo de corte, es necesario realizar varios ciclos de soldadura de prueba y retirar los restos de película. El resultado de las pruebas puede considerarse satisfactorio cuando retirar los restos de película a lo largo de la línea de soldadura no requiere más de un corte con tijeras.
8.0 Mantenimiento
Gracias a las soluciones constructivas aplicadas y a la estructura sin complicaciones de la máquina, las actividades de mantenimiento y control, tanto preventivas como de emergencia, son relativamente sencillas y no requieren largas interrupciones en el funcionamiento de la máquina.
La máquina de soldar requiere poco trabajo relacionado con la máquina
funcionamiento y mantenimiento, siempre que se mantengan unas condiciones de uso adecuadas. Es necesario comprobar periódicamente el estado técnico de la conexión de la máquina a la red eléctrica, en particular el estado del sistema de protección contra descargas eléctricas.
Todos los componentes del generador de alta frecuencia, en particular todos los elementos aislantes, deben mantenerse limpios. Debe limpiar a fondo el interior del sistema de salida del generador al menos una vez cada tres meses. Tras dicha limpieza, debe comprobarse el estado de los componentes del generador y de las unidades que cooperan directamente con el generador, y deben apretarse todas las conexiones.
Debido a las propiedades específicas de la máquina, se recomienda que algunas de las tareas mencionadas sean realizadas por personal de servicio técnico autorizado y debidamente cualificado del Fabricante (se aplica particularmente a situaciones de emergencia). Las tareas mencionadas requieren especial cuidado y atención.
ATENCIÓN: Durante el funcionamiento del generador, sus componentes, así como los componentes del circuito de salida, tienen una tensión de hasta 8 kV CC y una tensión de alta frecuencia de hasta 480 V (27,12 MHz ).
ATENCIÓN: Los condensadores del generador de ánodos pueden retener carga eléctrica de la tensión de hasta 8000 VDC incluso después de desconectar la máquina de soldar de la red eléctrica. Antes de tocar los componentes del generador de alta frecuencia, estos condensadores deben estar siempre descargados.
La puesta a tierra de la estructura de la máquina debe realizarse con especial cuidado. Recuerde que el generador no debe funcionar nunca cuando las pantallas de protección estén retiradas, tampoco durante las actividades de servicio técnico y mantenimiento, cuando el nivel de seguridad de la máquina puede ser inferior debido a la reparación que se está realizando.
Todas las tareas de mantenimiento y reparaciones requieren un permiso de las personas autorizadas.
Debe mantener un REGISTRO DE LA MÁQUINAque incluya las fechas y los tipos de actividades preventivas o reparaciones realizadas.
Durante las tareas de mantenimiento o cualquier otra operación manual requerida, nunca entre ni ponga ninguna parte del cuerpo en la zona expuesta a peligros potenciales y predecibles, con el fin de eliminar el riesgo de situaciones peligrosas potenciales y predecibles.
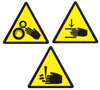
Lleve siempre ropa de protección y calzado antideslizante, para reducir el riesgo de caídas. Asegúrese siempre de llevar las mangas bien ajustadas alrededor de las muñecas o debidamente remangadas.
Utilice siempre guantes de trabajo cuando trabaje con componentes con bordes afilados.
Todo el personal responsable del funcionamiento y mantenimiento de la máquina debe estar debidamente formado e instruido.
Todas y cada una de las operaciones de mantenimiento o reparación pueden ser realizadas exclusivamente por personal autorizado y cualificado, capaz de interpretar correctamente los defectos y averías, leer los diagramas de instalación y los planos técnicos, con el fin de garantizar que todas las operaciones de desmontaje y montaje relacionadas con los procedimientos de mantenimiento estándar se realicen de forma profesional y, lo que es más importante, segura.
Todas las tareas realizadas en el área de operación de la unidad de prensado, es decir, el montaje y desmontaje del electrodo, realizadas cuando la alimentación de la máquina está encendida, pueden ser llevadas a cabo exclusivamente por el personal debidamente formado en Salud y Seguridad en el Trabajo, incluyendo particularmente el riesgo que implica la operación de la unidad de prensado.
También debe prever el posible comportamiento no estándar de la máquina, cuando el sistema neumático de la máquina de soldar o los conductos de suministro de aire comprimido estén desprecintados. Esto provocará un descenso automático lento de la unidad de prensado de la máquina de soldar.
El personal debe ser informado de dicho riesgo durante la formación en Salud y Seguridad en el Trabajo.
ATENCIÓN: Durante todas y cada una de las operaciones mencionadas debe detenerse el funcionamiento de la máquina.
8.2 Programa preventivo-Comprobaciones periódicas
AL COMIENZO DE CADA TURNO
- Compruebe si la zona de funcionamiento de la máquina está limpia y ordenada;
- Compruebe visualmente si las pantallas de protección están bloqueadas;
- Compruebe la iluminación de la zona de operaciones;
- Compruebe si el botón de PARADA DE EMERGENCIA funciona correctamente;
- Compruebe la protección principal en la instalación eléctrica;
- Comprobar el estado de los elementos conductores de cobre y latón en la zona del portaelectrodos y de los elementos de puesta a tierra de las pantallas laterales de protección.
CADA 100 HORAS DE FUNCIONAMIENTO DE LA MÁQUINA (AL MENOS UNA VEZ POR SEMANA):
- Compruebe si los tornillos portantes (incluidos, en particular, los tornillos de fijación de las herramientas) están correctamente fijados y apretados;
- Compruebe el nivel de agua de condensación en el recipiente del filtro de aire comprimido; si hay agua, vacíe el recipiente; si hay grandes cantidades de contaminantes sólidos, desmonte y lave el recipiente;
CADA 500 HORAS DE FUNCIONAMIENTO DE LA MÁQUINA (PERO AL MENOS CADA DOS SEMANAS)
- Compruebe si el radiador de la lámpara de ánodo está limpio;
- Compruebe la cantidad de contaminantes sólidos y polvo en la cámara del generador; si es necesario, limpie la cámara con un aspirador o una pistola de aire comprimido;
- Compruebe si los elementos móviles (en particular las herramientas y las guías) están limpios;
- Engrase los elementos móviles, especialmente las guías; si es necesario, utilice grasa sólida a base de litio y un engrasador;
- Compruebe y pruebe la unidad de alarma.
CADA 1000 HORAS DE FUNCIONAMIENTO DE LA MÁQUINA (PERO AL MENOS CADA SEIS MESES)
- Compruebe visualmente el estado de los elementos mecánicos;
- Apriete todos los tornillos;
- Compruebe si las medidas de protección contra descargas eléctricas funcionan correctamente;
- Comprobar la eficacia del engrase de las guías;
- Compruebe el estado de los elementos de contacto principales: deben sustituirse los contactores principales u otros elementos de contacto del sistema, como contactores o relés de superficies excesivamente desgastadas.
ATENCIÓN: Antes de cada mantenimiento, apague la máquina con el interruptor principal y desconecte la alimentación eléctrica.
ATENCIÓN: Antes de cada mantenimiento, apague la máquina con el interruptor principal y desconecte la alimentación eléctrica.
9.1 Requisitos básicos
Guías
- La máquina puede utilizarse exclusivamente de forma adecuada a su finalidad explícitamente descrita en el punto 1.
- Las soluciones constructivas aplicadas relacionadas con la seguridad reducen al mínimo tanto el comportamiento no estándar de la máquina como los peligros para los operarios y otras personas que tengan contacto con la máquina, siempre que se observen los principios del trabajo seguro. La máquina está equipada con interruptores de llave en las pantallas de protección, cuyo desmontaje requiere herramientas específicas, incluyendo el interruptor en la puerta de la cámara de soldadura, el botón de PARADA DE EMERGENCIA y las pantallas de protección móviles que encierran la zona de soldadura durante el tiempo del proceso de soldadura.
- Las cuestiones relacionadas con la seguridad y la salud en el trabajo y la evaluación de riesgos durante el contacto de una persona con la máquina se han descrito detalladamente en los capítulos anteriores de este manual.
- Como este tema es extremadamente importante, algunas instrucciones se repiten en esta sección.
- Todo nuevo empleado que tenga contacto con la máquina de soldar debe recibir formación en el campo de los principios básicos de salud y seguridad en el trabajo y familiarizarse con los tipos de riesgos que implica el funcionamiento de la máquina de soldar, a menos que el operario siga las normas y principios obligatorios.
- El personal responsable del manejo de la máquina de soldar debe tener conocimientos profundos de primeros auxilios en casos de descargas eléctricas y quemaduras. En el caso de personas que trabajen con dispositivos que utilicen ondas electromagnéticas de frecuencia en el rango de 0,1 - 300 MHz, se requieren exámenes médicos periódicos.
- Tras la instalación de la máquina de soldar, es necesario medir la emisión de campo electromagnético y establecer los límites de la zona peligrosa.
- En función de los resultados de las mediciones, se determinan el nivel de peligro y el tiempo durante el cual los operarios pueden permanecer en la zona peligrosa, de conformidad con las normas aplicables.
- Sólo podrán acceder a la zona peligrosa los operarios que dispongan de las autorizaciones pertinentes para trabajar en la zona expuesta a campos electromagnéticos, basadas en reconocimientos médicos especializados, y que hayan recibido la formación adecuada sobre el manejo seguro de los dispositivos que emiten campos electromagnéticos.
- Las mediciones mencionadas deben ser realizadas por una institución autorizada. Las instrucciones detalladas relativas a dichas mediciones se especifican en la normativa aplicable en el país en el que se utiliza la máquina.
- Los operarios de las máquinas deben llevar siempre ropa de trabajo estándar, guantes, casco y calzado antideslizante.
- El entorno de trabajo de la máquina, el suelo y los soportes y asideros manuales deben estar siempre limpios y exentos de cualquier tipo de contaminación, grasa o barro, a fin de reducir al mínimo posible el riesgo de resbalones o caídas.
- No utilice nunca la máquina en el modo de funcionamiento automático sin los elementos de protección fijos o móviles. Compruebe periódicamente si todos los interruptores de emergencia y todos los demás elementos de protección están bien montados y funcionan correctamente.
- Todo operador de la máquina debe ser instruido sobre las funciones de los elementos de protección de la máquina y su correcta utilización.
- En la zona que rodea la máquina (aproximadamente 1,5 m alrededor de la máquina) no puede haber objetos que puedan interferir en el funcionamiento de la máquina. Esta zona debe mantenerse limpia y disponer de iluminación adecuada.
- No utilice nunca los manipuladores de la máquina ni los tubos flexibles como soportes. Recuerde que cualquier movimiento accidental del manipulador de la máquina puede poner en marcha accidentalmente el funcionamiento de la máquina.
- Informe siempre al supervisor y/o al personal de tráfico sobre todos y cada uno de los casos de funcionamiento incorrecto de la máquina.
- Todas las tareas de mantenimiento y reparaciones requieren un permiso de las personas autorizadas.
- Debe llevar un Registro de máquinasque incluya las fechas y los tipos de actividades preventivas o reparaciones realizadas.
- Durante las tareas de mantenimiento o cualquier otra operación manual requerida, nunca entre ni ponga ninguna parte del cuerpo en la zona expuesta a peligros potenciales y predecibles, con el fin de eliminar el riesgo de situaciones peligrosas potenciales y predecibles.
NO UTILICE NUNCA LA MÁQUINA DE SOLDAR CUANDO LAS PANTALLAS DE PROTECCIÓN ESTÉN RETIRADAS O CUANDO LOS INTERRUPTORES DE LLAVE ESTÉN BLOQUEADOS. ESTO SE APLICA ESPECIALMENTE A LAS PANTALLAS DE PROTECCIÓN DEL GENERADOR. Dichas pantallas de protección reducen la emisión de campos electromagnéticos y evitan el contacto accidental con los elementos del circuito eléctrico con tensión de alimentación o alta tensión de hasta 8000 V.
- Lleve siempre ropa de protección y calzado antideslizante, para reducir el riesgo de caídas. Asegúrese siempre de llevar las mangas bien ajustadas alrededor de las muñecas o debidamente remangadas.
- Utilice siempre guantes de trabajo cuando trabaje con componentes calientes o con bordes afilados.
- También hay que recordar que en los componentes que no se han cubierto detrás de ninguna pantalla por razones ergonómicas, es decir, el electrodo y los componentes conductores del portaelectrodo, hay tensión de alta frecuencia. NUNCA TOQUE ESOS COMPONENTES DURANTE EL PROCESO DE SOLDADURA.
- Tocar esos componentes durante el proceso de soldadura provoca quemaduras en la piel con tensión de alta frecuencia. Sin embargo, no es peligroso para la vida ni para la salud.
- El método adoptado de alimentación eléctrica de la máquina de soldar plantea un riesgo potencial de prensado o aplastamiento de miembros en el espacio entre el prensado de los electrodos. Todos y cada uno de los trabajos en el área de operación de la unidad de prensado, es decir, el montaje y desmontaje de los electrodos o extender y retirar el material y la chatarra, que se realizan cuando la máquina de soldadura está conectada a la fuente de alimentación se pueden hacer exclusivamente por los empleados formados en el campo de la salud y seguridad en el trabajo, incluyendo la información sobre el riesgo planteado por la unidad de prensado.
- Durante el funcionamiento de la máquina, el operario debe situarse en la zona indicada a continuación
Fig. 16. ZDW-15-K - zona de trabajo de seguridad (color verde)
9.3 Condiciones de seguridad laboral del personal encargado del mantenimiento y reparación de la máquina de soldar- Estos trabajos requieren un cuidado especial. Hay que recordar siempre que los condensadores del generador anódico pueden mantener la carga eléctrica de la tensión de 8000 V incluso después de desconectar la máquina de soldar de la red eléctrica. Antes de tocar los componentes del generador de alta frecuencia, estos condensadores deben estar siempre descargados.
- Durante el funcionamiento del generador, sus componentes, así como los componentes del circuito de salida, tienen la tensión de alta frecuencia. La puesta a tierra de la estructura de la máquina debe realizarse con especial cuidado. También hay que recordar que el tiempo de funcionamiento del generador con los escudos de protección quitados debe reducirse al mínimo.
- Todas las reparaciones deben ser realizadas de acuerdo con los principios vigentes de reparación y funcionamiento de dispositivos por una persona que tenga un certificado adecuado expedido por la Asociación de Electricistas correspondiente (en Polonia: SEP).
- Todo el personal responsable del funcionamiento y mantenimiento de la máquina debe estar debidamente formado e instruido.
- Todas y cada una de las operaciones de mantenimiento o reparación pueden ser realizadas exclusivamente por personal autorizado y cualificado, capaz de interpretar correctamente los defectos y fallos y de leer los diagramas de instalación, con el fin de garantizar que todas las operaciones de desmontaje y montaje relacionadas con los procedimientos de mantenimiento estándar se realicen de forma profesional y, lo que es más importante, segura.
- Durante todas y cada una de las operaciones mencionadas debe detenerse el funcionamiento de la máquina.
TOMAR TODAS LAS MEDIDAS NECESARIAS PARA PREVENIR:
- Utilizar la máquina de forma distinta a la descrita en este Manual de Operación y Mantenimiento,
- Instalación incorrecta, no realizada de acuerdo con los procedimientos descritos en este manual,
- Manejo inadecuado de la máquina o su manejo por personal sin la formación adecuada,
- Suministro a máquina de parámetros inadecuados,
- Mantenimiento insuficiente de la máquina,
- Alteraciones no autorizadas o interferencias por parte de personas sin las licencias, permisos o formación necesarios,
- Utilizar piezas de recambio distintas de las originales,
- Cualquier acción de cualquier persona que no esté de acuerdo con los principios especificados en este Manual de Operación y Mantenimiento y cualquier información de advertencia.
10.0 Documentación eléctrica
10.1 Parámetros de la fuente de alimentación - Datos técnicos
Alimentación |
3 x 480 VCA; 50 Hz |
Protección de la cabeza |
40 A |
Capacidad instalada |
22 kVA |
Potencia de salida en HF |
15 kW |
Tensión de funcionamiento |
24 VDC |
Frecuencia de funcionamiento |
27,12 MHz |
Estabilidad de frecuencia |
+/- 0.6 % |
Lámpara generadora (triodo metalocerámico) |
ITL 12-1 |
Sistema de circuito antidescarga |
ANTIFLASH completo con filtro HF |
10.2 Lista de dispositivos eléctricos
La lista de dispositivos eléctricos incluye las últimas páginas del capítulo 0
13.3 PLANOS DE INSTALACIÓN ELÉCTRICA Si tiene alguna duda, póngase en contacto con el fabricante.
10.3 Planos de diseño del concepto de instalación eléctrica
Ver anexo
11.0 Documentación neumática
11.1 Datos técnicos
Presión de funcionamiento |
0,4 - 0,8 MPa |
Consumo de aire comprimido |
Máx. 70 nl (estándar) por ciclo |
Pureza del aire |
según ISO8573-1:4-4-4 |
Rendimiento de filtrado |
20 um (ISO8573-1 4-4-4) |
- accionamiento de los soportes neumáticos del electrodo;
- accionamiento del electrodo conectado a tierra;
- unidad de prensa;
- soportes para electrodo.
Además, el sistema neumático consta de un sistema de preparación del aire: filtro y reductor de presión, arranque progresivo, elementos de conexión, válvula de descarga y válvulas estranguladoras de retención. El aire se suministra a través de la válvula de descarga a la unidad VFRL; se filtra previamente y se reduce al volumen necesario. A continuación, se suministra a través de válvulas de distribución controladas eléctrica o electroneumáticamente a los actuadores neumáticos apropiados iniciando su movimiento. La dinámica del movimiento de los actuadores puede ajustarse mediante válvulas de estrangulación montadas en los actuadores. La secuencia del movimiento de los actuadores está controlada por el controlador de la máquina de soldar.
11.3 Manual de instrucciones
VER ANEXOS
12.0 Instrucciones generales
12.1 Instrucciones generales
Las soluciones constructivas aplicadas y los componentes de alta calidad permiten el correcto funcionamiento de la máquina durante un período de unos 30 años. Sin embargo, pueden producirse algunos cambios en las necesidades del Cliente o cambios en los principios o normas que no pueden predecirse hoy en día, lo que podría requerir una eliminación de la máquina antes de que finalice el periodo mencionado. Esto también se aplica a las piezas o componentes sustituidos o reparados de la máquina de soldar.
El Cliente está obligado a garantizar que la eliminación de la máquina o de sus componentes se realiza de conformidad con los requisitos legales aplicables vigentes en un momento y lugar determinados.
Todos los componentes de la máquina son reciclables.
La eliminación de residuos peligrosos debe correr siempre a cargo de empresas especializadas.
Los tipos de residuos producidos durante el ciclo de vida del aparato se describen a continuación en el punto 0.
12.2 Residuos
- Trozos de tela o papel saturados de sustancias utilizadas para la limpieza de los componentes de la máquina;
- Piezas de recambio usadas del generador, según el material del que estén hechas;
- Residuos de grasas líquidas o sólidas;
- Grasa sobrante tras el engrase o mantenimiento de la máquina;
- Lámpara del generador.
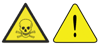
Todos los residuos producidos en el curso de actividades de sustitución o servicio técnico, que estén contaminados con grasa, no pueden eliminarse junto con los residuos industriales.

12.3 Procedimiento de desmontaje de la máquina antes de su eliminación
- Coloque la máquina de modo que permanezca inmóvil.
- Desconecte la alimentación eléctrica de la máquina.
- Desconecte el suministro de aire comprimido de la máquina.
- Retire los conductos flexibles de plástico o goma y asegúrese de que los elimina una empresa especializada.
- Desconecte y retire los cables y dispositivos eléctricos y asegúrese de que los elimina una empresa especializada.
- Separe los componentes de acero y los de metales no ferrosos y asegúrese de que los elimina una empresa especializada.
13.0 Apéndices
13.1 Etiqueta de modelo y número de serie
Cada una de las máquinas de Zemat Technology Group Ltd lleva esta pegatina situada en la parte trasera de la máquina. Identifica el modelo y el número de serie de cada soldadora.
También indicará la tensión y los hercios necesarios para el funcionamiento.
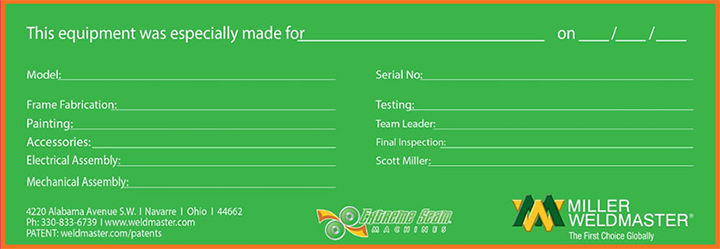