Este manual de instrucciones pretende ser una guía para el manejo de la RFlex Travel Extreme. Para garantizar un rendimiento óptimo de su soldadora, siga con precisión las recomendaciones y especificaciones.
Índice
- Capítulo 1. Uso previsto Uso previsto
- Capítulo 2: Señales de seguridad y pictogramas
- Capítulo 3. Datos técnicos Datos técnicos
- Capítulo 4. Descripción técnica Descripción técnica
- Capítulo 5. Montaje e instalación Montaje e instalación
- Capítulo 6. Funcionamiento Operación
- Capítulo 7: Selección de los parámetros de soldadura
- Capítulo 8. Mantenimiento Mantenimiento
- Capítulo 9:
Salud y seguridad en el trabajo
- Capítulo 10. Documentación eléctrica Documentación eléctrica
- Capítulo 11: Documentación neumática
- Capítulo 12: Instrucciones generales
- Capítulo 13: Apéndices
- Capítulo 14. Documentos adicionales de la máquina Documentos adicionales de la máquina
Para obtener más información técnica sobre esta máquina, llame a nuestro Centro de resoluciones al 1-855-888-WELD o envíe un correo electrónico a service@weldmaster.com.
1.0 Visión general de la máquina/uso previsto
Miller Weldmaster es una empresa líder en máquinas de soldadura de alta frecuencia de cabezal móvil. La soldadora Traveling Head RFlex está diseñada específicamente para la producción de lonas de gran formato, carpas, sistemas de sombreado, cubiertas para camiones, cubiertas para piscinas, hangares de líneas aéreas, vallas publicitarias, señales, cortinas laterales y muchas otras uniones de tejidos técnicos en general. La máquina puede equiparse con electrodos curvos especiales para soldar perfiles de ventana redondos de PVC transparente y cualquier otra forma que requiera un sellado de precisión.
RFlex El modelo Travel está equipado con un engranaje especial de movimiento lineal de alta precisión, controlado por variador de frecuencia y barandilla deslizante para lograr una costura perfecta en línea recta continua. La mesa de trabajo tiene canalón para facilitar la manipulación del material. La mesa de trabajo de vacío opcional con una longitud de hasta 12 metros y las guías láser permiten manipular materiales de gran formato y posicionar la soldadura con precisión para una rápida configuración de la producción.
Con el uso de la pantalla táctil HMI y el PLC programable, el operador puede introducir fácilmente múltiples recetas de soldadura/costura. RFlex La soldadora Travel tiene salidas de potencia RF para cargas de producción pesadas y tejidos reforzados de alta resistencia.
Ciclos de soldadura automáticos, accionados neumáticamente soldadura barra, electrónico movimiento contador controlando la longitud, recorrido distancia y soldadura ciclo número hacen de esta máquina una herramienta perfecta para producto de gama alta donde precisión, durabilidad y resistencia son la clave.
RFlex Travel puede actualizarse fácilmente y convertirse en una máquina de producción Keder con el uso de un accesorio especial y un electrodo de soldadura.
LAS CARACTERÍSTICAS MÁS IMPORTANTES DE LA MÁQUINA:
- el mantenimiento rutinario de la máquina es muy sencillo;
- el prensado puede ajustarse con precisión;
- el fabricante instaló el botón de emergencia en el panel de control;
- la máquina está equipada con la columna luminosa de señalización para aumentar la seguridad del operador cuando la máquina está encendida;
- el operador puede programar y controlar el ciclo de trabajo de la máquina gracias al panel táctil HMI;
- la herramienta de programación permite al operario introducir en el sistema parámetros como: el tiempo y la potencia de soldadura junto con el tiempo de enfriamiento;
- mediante el panel HMI instalado en la máquina, el operario puede guardar muchos programas de soldadura para distintos tipos de materiales, por no hablar de los que se utilizan para trabajar con distintos tipos de electrodos;
- Para mayor comodidad del operario, la máquina está equipada con un portaelectrodos especialmente diseñado para cambiar rápidamente el electrodo de soldadura;
- la máquina está equipada con el electrodo de puesta a tierra adicional para proteger al usuario contra el aumento del nivel de radiación HF no ionizante emitida por la máquina;
- ZTG RF AutoTuning System™: la máquina está equipada con el sistema de control automático de la potencia de salida para aumentar la seguridad del operador;
- ZTG SafeDOWN™ - la máquina se suministra con el sistema que debe proteger eficazmente al operador contra el electrodo cuando se está bajando;
- ZTG Flash™ - otro sistema de la máquina que se supone que protege el electrodo y la materia prima que se está soldando de los posibles daños causados por un paso de arco;
- Todas las máquinas han recibido los certificados de conformidad CE
TECNOLOGÍA DE ALTA FRECUENCIA:
La soldadura de alta frecuencia, conocida como soldadura por radiofrecuencia (RF) o dieléctrica, es el proceso de fusión de materiales mediante la aplicación de energía de radiofrecuencia a la zona que se va a unir. La soldadura resultante puede ser tan fuerte como los materiales originales.
La soldadura HF se basa en determinadas propiedades del material a soldar para provocar la generación de calor en un campo eléctrico que alterna rápidamente. Esto significa que sólo algunos materiales pueden soldarse con esta técnica. El proceso consiste en someter las piezas que se van a unir a un campo electromagnético de alta frecuencia (normalmente 27,12 MHz), que se aplica normalmente entre dos barras metálicas. Estas barras también actúan como aplicadores de presión durante el calentamiento y el enfriamiento. El campo eléctrico dinámico hace oscilar las moléculas de los termoplásticos polares. Dependiendo de su geometría y momento dipolar, estas moléculas pueden traducir parte de este movimiento oscilatorio en energía térmica y provocar el calentamiento del material. Una medida de esta interacción es el factor de pérdida, que depende de la temperatura y la frecuencia.
El cloruro de polivinilo (PVC) y los poliuretanos son los termoplásticos más comunes que se sueldan mediante el proceso de RF. Es posible soldar por RF otros polímeros, incluidos nylon, PET, PET-G, A-PET, EVA y algunas resinas ABS, pero se requieren condiciones especiales; por ejemplo, el nylon y el PET son soldables si se utilizan barras de soldadura precalentadas además de la potencia de RF.
La soldadura por HF no suele ser adecuada para PTFE, policarbonato, poliestireno, polietileno o polipropileno. Sin embargo, debido a las inminentes restricciones en el uso del PVC, se ha desarrollado un grado especial de poliolefina que sí puede soldarse por RF.
La función principal de la soldadura HF es formar una junta en dos o más espesores de chapa. Existen varias funciones opcionales. La herramienta de soldadura puede grabarse o perfilarse para dar a toda la zona soldada un aspecto decorativo o puede incorporar una técnica de gofrado para colocar letras, logotipos o efectos decorativos en los elementos soldados. Al incorporar un filo de corte adyacente a la superficie de soldadura, el proceso puede soldar y cortar simultáneamente un material. El filo de corte comprime el plástico caliente lo suficiente como para permitir arrancar el material sobrante, de ahí que este proceso se conozca a menudo como soldadura por desgarro.
ATENCIÓN: El fabricante no se hace responsable de los daños o lesiones derivados de un uso inadecuado de esta máquina.
ATENCIÓN: Para utilizar la máquina de forma óptima y segura, lea atentamente y siga todas las instrucciones incluidas en este Manual de Operación y Mantenimiento.
ATENCIÓN: Todos los operarios, formados en seguridad operacional, procedimientos de operación y riesgo de la máquina de soldar, así como los cualificados para operar la máquina de soldar, deberán, por parte del Contratista, firmar, con su firma legible, el formulario adjunto.
ATENCIÓN: La máquina de soldar de alta frecuencia ha sido diseñada y fabricada en una versión no apta para personas discapacitadas. Cuando la máquina vaya a ser manejada por personas discapacitadas, deberá ser adaptada adecuadamente previa consulta con el fabricante.
2.0 Señales de seguridad y pictogramas
2.1 Información general
Para utilizar la soldadora de forma óptima y segura, lea atentamente y siga todas las instrucciones incluidas en este Manual de Operación y Mantenimiento, también en particular toda la información y señales de advertencia, prohibición, restricción y orden.
Sobre la base de la información incluida en este Manual de Operación y Mantenimiento, el Cliente debe elaborar Manuales de Puesto de Trabajo para los empleados.
El Cliente es plena, legal y materialmente responsable de todos y cada uno de los sucesos que resulten de un conocimiento insuficiente de este Manual de Operación y Mantenimiento o del incumplimiento de los principios de la Seguridad y Salud en el Trabajo.

ATENCIÓN: Antes de iniciar cualquier trabajo de cualquier persona que opere la máquina de soldadura HF es obligatorio familiarizarse con el Manual de Operación y Mantenimiento subsiguiente.
ATENCIÓN: Cualquier receptor o persona autorizada por el receptor sobre la base del presente Manual de Operación y Mantenimiento y la característica adecuada de la producción-tecnología es obligatorio debido emitir MANUAL DE MANDO DE TRABAJO para los operarios.
ATENCIÓN: La máquina de soldadura de alta frecuencia puede ser operada SOLO por trabajadores que hayan sido formados en el mantenimiento del aparato y en SEGURIDAD INDUSTRIAL con especial consideración del posible riesgo procedente de la máquina.
ATENCIÓN: Durante toda la vida útil de la máquina, el Fabricante del dispositivo sugiere al Comprador utilizar el personal de servicio capacitado proporcionado por el Fabricante o cualquier equipo de servicio autorizado por el Fabricante.
ATENCIÓN: El fabricante recomienda encarecidamente instalar la máquina de soldar sólo en un entorno industrial.
ATENCIÓN: La máquina debe estar correctamente nivelada y debe tener lugar fijo de una operación.
ATENCIÓN: La manipulación descuidada de la máquina durante el transporte (traslado) puede provocar lesiones graves o accidentes.
ATENCIÓN: El generador es alimentado por la tensión peligrosa para la vida de la red eléctrica 3 x480 VAC; 50 Hz. El dispositivo tiene el alto voltaje hasta 8000 VDC. Todas las actividades de servicio o prevención sólo pueden ser ejecutadas por el personal capacitado con la autoridad requerida por la ley.
ATENCIÓN: Es necesario que el Comprador se encargue de la correcta ejecución y del control periódico de prevención de la instalación de protección contra descargas eléctricas para cada aparato que esté en uso. Toda la responsabilidad en esta materia recae sobre el Comprador.
ATENCIÓN: La tensión de la lámpara debe ser la misma que se especifica en la ficha técnica del producto - es posible ajustarla mediante derivaciones en el primario del transformador de incandescencia.
ATENCIÓN: La lámpara debe precalentarse durante aproximadamente una hora después de la instalación.
ATENCIÓN: Cualquier trabajo dentro de la zona de la unidad de prensado activo de la prensa, es decir, la sustitución del dispositivo puede ser ejecutado con medidas de precaución especiales sólo por el equipo de servicio capacitado.
ATENCIÓN: La parada de emergencia de la máquina es posible en cualquier momento pulsando la tecla EMERGENCIA Botón STOP (el botón rojo sobre fondo amarillo).
ATENCIÓN: El entorno de trabajo de la máquina, el suelo y los soportes y asideros manuales deben estar siempre limpios y libres de cualquier tipo de contaminación, grasa o barro, para reducir al mínimo posible el riesgo de resbalones o caídas.
PRECAUCIÓN: Desenchufe la máquina antes de retirar cualquier panel de acceso o abrir las puertas. Todos los protectores y paneles de acceso deben estar en su lugar antes de operar esta máquina.
ATENCIÓN: La temperatura del electrodo es de hasta 100 °C. Por lo tanto, cuando se toca uno puede ser quemado.
ATENCIÓN: La lámpara contiene metales de tierras raras y óxidos metálicos de tierras raras que son altamente tóxicos. En caso de rotura, la lámpara debe eliminarse con sumo cuidado y con la ayuda de especializado servicios.
ATENCIÓN: La máquina de soldadura de alta frecuencia es una fuente de radiación electromagnética no iónica. Después de la instalación de la máquina en el lugar del comprador, la medición de la radiación no iónica se debe hacer. Las mediciones de radiación deben ser realizadas por una empresa autorizada.
ATENCIÓN: La máquina de soldadura de alta frecuencia debe trabajar en un lugar de trabajo firme, ya que la transposición requiere una nueva medición de la intensidad de la radiación no iónica..
ATENCIÓN: Está prohibido que las personas con marcapasos implantado permanezcan en la zona de radiación activa..
ATENCIÓN: El fabricante sugiere no emplear a ninguna mujer embarazada o en período de lactancia en la zona de radiación no iónica activa..
ATENCIÓN: Limpie el filtro de aire de la instalación neumática al menos una vez al mes.
¡ATENCIÓN! Allí son láser indicadores en el dispositivo. Bajo ningún circunstancias debe el láser haz sea dirigido hacia el ojos como it puede causa temporal ceguera o, en casos extremos, permanente ver daños.


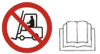

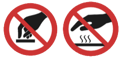



























3.0 Datos técnicos
Tipo deype |
RFlex Viajar |
Materiales de soldadura |
PVC, tejidos recubiertos de PVC |
Alimentación |
3 x 220 V; 50/60 Hz |
Controlador PLC |
Delta |
Tensión de control |
24 VDC |
Capacidad instalada |
22 kVA |
Potencia de salida RF |
15 kW |
Ajuste de la capacidad de salida |
manual/autotuner |
Frecuencia de funcionamiento |
27,12 MHz |
Estabilidad de frecuencia |
+/- 0,6 % |
Sistema antiflash, ZEMAT TG |
sensor ARC de sensibilidad ultrarrápida |
Consumo de aire comprimido |
70 nl/ciclo |
Presión de aire comprimido |
0,4-0,8 MPa |
Longitud máx. del electrodo |
1500 mm |
Tamaño de la mesa de trabajo |
1620 x 320 mm |
Carrera del actuador |
160 mm |
Accionamiento del electrodo de presión |
neumático |
Fuerza de presión (máx.) |
1900 kG |
Lámpara del generador |
ITL 12-1 |
Refrigerante |
aire |
Peso de la máquina |
~ 1600 kg |
Dimensiones |
VER ANEXOS |
4.0 Descripción técnica
Radio Frecuencia Soldador RFlex Viaje consta de los siguientes elementos básicos :
- SOLDADURA CABEZAL - con un soporte bastidor fabricado de chapas de acero soldadas y perfiles perfilados. La parte interna de la construcción puede dividirse en tres zonas:
- una parte trasera parte - donde un generador de alta frecuencia está situado con un transformador de ánodo y un armario de control . Esta parte está protegida por cubiertas desmontables equipadas con interruptores de límite;
- una zona de soldadura - con mesa de trabajo. La soldadura se realiza mediante un electrodo presionado contra la mesa por una empuñadura aislada conectada a un actuador neumático mediante una placa intermedia y aisladores. La zona de soldadura está protegida de la radiación no ionizante por el electrodo de masa móvil que se presiona contra la mesa durante el procedimiento de soldadura y como resultado se crea una especie de condensador que se supone que limita la radiación no ionizante. Debe prestarse especial atención al hecho de que la superficie del material a soldar esté distribuida uniformemente sobre la mesa de trabajo y no esté ondulada. Debe prestarse especial atención aque no haya objetos metálicos cerca del electrodo de masa y debajo de él. El incumplimiento de las condiciones de las dos advertencias anteriores puede afectar a la emisión del campo electromagnético. Sobre la zona de soldadura hay un panel de mando en el que están situados la mayoría de los controles de los dispositivos. Además, la máquina ha sido equipada con un electrodo adicional que permite soldar sin utilizar electrodo de masa. Tras instalar este tipo de electrodo en el soporte y comenzar a bajarlo, se activa un final de carrera adicional que inhibe el movimiento del electrodo de masa.
- el accionamiento de la máquina está situado en la parte inferior de la contracción . Consta de un motor asíncrono conectado con una cremallera mediante transmisión de cremallera. El motor es controlado por un inversor colocado en el armario de control en la cremallera de la máquina. La cremallera se desplaza sobre una cadena fijada a el conjunto de la mesa . La trayectoria de la máquina está controlada por raíles sobre los cuales se desplazan carros deslizantes o ruedas.
|
- MESA DE TRABAJO con artesa - fabricada con perfiles de aluminio interconectados para proporcionar la rigidez adecuada. En la parte delantera, la mesa de trabajo se fija sobre unos perfiles de acero que son la base de los patines (raíles) sobre los que se desplaza la máquina. En la parte trasera, la mesa de trabajo se apoya en postes plegables que se abaten durante el paso de la máquina por los raíles. En ambos extremos de la mesa de trabajo, hay interruptores de parachoques ajustables que activan los finales de carrera que marcan el comienzo y el final de la mesa de trabajo, así como dos topes elásticos que, en caso de avería, detienen la máquina al final de la mesa de trabajo para protegerla de posibles daños. La alimentación eléctrica y neumática del cabezal de soldadura de alta frecuencia se realiza mediante cables colocados en guías de cables flexibles. Las conexiones eléctricas y neumáticas están situadas en el centro de la parte trasera de la mesa de trabajo.
Se distinguen los siguientes sistemas de la máquina:
- EL SISTEMA DE CONTROL consiste en un PLC con un panel táctil HMI, elementos de manejo de control colocados en un panel de control y montaje eléctrico y electrónico colocado en el armario de control y dentro de la chassy de la máquina.
- EL SISTEMA DE AIRE COMPRIMIDO compuesto, entre otros, por un conjunto de preparación de aire comprimido, válvulas de distribución, válvulas de reducción y cilindros neumáticos.
- EL SISTEMA DE GENERACIÓN DE RF consiste en un generador de alta frecuencia autoactivable con constantes distribuidas con un circuito LC de alta Q orientado a una frecuencia de resonancia de 27,12MHz. El sistema también incluye un triodo, tubo generador de HF, transformadores de ánodo y filamento, así como un sistema de refrigeración del tubo generador de HF.
El portaelectrodos de soldadura está equipado con un sistema de agarre automático controlado desde el panel táctil HMI. Permite sustituir los electrodos sin necesidad de herramientas.
|
La máquina incorpora un sistema (ZTG AntiCRUSH) diseñado para proteger las manos de los operarios contra el aplastamiento. Cuando una mano o cualquier objeto con una altura diferente de la altura del material soldado se coloca debajo del electrodo de soldadura, el electrodo se tira automáticamente hacia arriba durante la fase de prensado.
|
Además, hay indicadores láser instalados en el chasis de la máquina para facilitar el posicionamiento del material soldado en la mesa de trabajo.
ATENCIÓN Evite exposición a el láser ¡Luz! En es estrictamente prohibido mirar fijamente directamente en el láser ¡Rayo! En láser seguridad clase es 3B (PN-EN 60825 1:2005).
Montaje planos, junto con las dimensiones de la soldador, están incluidas en los anexos de este manual de este manual.
Soldadura cabezal (sin el banco ) - elementos básicos de la máquina :
A - manipulación y control elementos colocados en el panel control ;
B -HMI panel táctil; C - interruptor principal ;
D - señalización columna;
E - interruptores de fin de carrera que indican la posición del electrodo ; F - electrodo de puesta a tierra ;
G - electrodo soporte;
5.1 Información y señales de restricciones e imperativos
El Fabricante proporciona un embalaje adecuado de la máquina para el momento del transporte. El tipo y la durabilidad del embalaje se adaptan a la distancia y al medio de transporte y, en consecuencia, al riesgo potencial de daños durante el transporte. El Fabricante sugiere que cada Cliente utilice los medios de transporte y el personal de servicio técnico del Fabricante.
El almacenamiento de la máquina no implica ningún requisito particular, aparte de un entorno de almacenamiento adecuado.
El local de almacenamiento debe garantizar una protección suficiente contra los factores meteorológicos, debe ser lo más seco posible y tener un nivel de humedad aceptable (inferior al 70%). También es necesario garantizar una protección adecuada contra la corrosión, sobre todo en lo que respecta a los componentes metálicos que no están pintados por razones técnicas.
Si la máquina se suministra en una caja y se envuelve en plástico que genera una atmósfera anticorrosiva, la máquina debe permanecer envuelta y embalada durante todo el periodo de almacenamiento.
A efectos de protección contra la humedad, se recomienda no almacenar la máquina directamente sobre el suelo del almacén, sino sobre palés.
La lámpara del generador (triodo) es un componente que requiere especial atención y manipulación en todas las fases, incluido el almacenamiento. La lámpara debe almacenarse en su embalaje original, en posición vertical, con el ánodo dirigido hacia arriba o hacia abajo, en una habitación seca. La lámpara es un componente de alto vacío, metálico y cerámico, que es extremadamente frágil y no se puede golpear ni dejar caer ni siquiera desde poca altura.
Golpear, dejar caer, sacudir o inclinar la lámpara durante un tiempo prolongado puede y suele provocar daños permanentes e irreversibles en la lámpara. En particular, el filamento de la lámpara - cátodo puede romperse, lo que en la mayoría de los casos extremos puede provocar cortocircuitos internos o la rotura de la lámpara.
ATENCIÓN: El fabricante sugiere no emplear a ninguna mujer embarazada o en período de lactancia en la zona de radiación no iónica activa..
Las disposiciones anteriores tienen por objeto instruir y advertir a todas las personas y servicios que puedan tener contacto con esta unidad acerca de su alta vulnerabilidad a todos los impulsos y golpes. Al mismo tiempo, no se aceptará ninguna reclamación relacionada con los daños permanentes descritos anteriormente en el curso del procedimiento de reclamación.
También hay que destacar que la lámpara del generador es un componente muy caro.
En caso de duda, se recomienda consultar al personal especializado del Fabricante.
5.2 Transporte de la máquina
El responsable del transporte y de la instalación de la máquina en la sede del ordenante deberá determinarse en el momento de la firma del contrato y, a más tardar, después de la prueba de recepción final de la máquina en la sede del fabricante, antes de la entrega del aparato al ordenante.
ATENCIÓN: Una manipulación descuidada del aparato durante el transporte / traslado puede provocar lesiones graves o accidentes.
SE PROHÍBE el montaje, desmontaje o transporte de la máquina por parte de personal sin la cualificación adecuada o sin estar familiarizado con los requisitos de seguridad descritos en el presente Manual de Operación y Mantenimiento. Tales acciones pueden causar accidentes o daños materiales.
Teniendo en cuenta el carácter específico del aparato, el Fabricante sugiere que cada Ordenante utilice los medios de transporte y el personal de servicio técnico del Fabricante.
El tubo de alimentación debe desmontarse antes de cualquier transporte o movimiento.
La lámpara debe transportarse o moverse siempre en el embalaje original del fabricante, en posición vertical, con el ánodo dirigido hacia arriba o hacia abajo, sin golpear ni sacudir la lámpara.
ATENCIÓN: La máquina debe transportarse en posición vertical.
Debido a su tamaño y estructura, la máquina requiere el desmontaje y desconexión de algunos componentes y unidades para el momento del transporte o mudanza. Es necesario desmontar componentes y herramientas frágiles y costosas (que deben transportarse en un maletín aparte). Es absolutamente necesario desmontar la lámpara del generador.
La máquina debe trasladarse utilizando dispositivos de elevación -grúas, carretillas elevadoras, transpaletas- con una capacidad de elevación suficiente que permita el transporte seguro del generador, mientras que las personas que manejen dichos dispositivos de elevación deben tener todas las licencias y cualificaciones válidas exigidas por la ley.
Todos los componentes de la máquina que puedan resultar dañados durante el transporte (si no se utiliza una caja de embalaje de alta durabilidad) o por dispositivos de elevación o desplazamiento deben asegurarse adecuadamente (siempre que se desmonten y embalen por separado).
Para garantizar una posición estable del dispositivo, es muy importante asegurar una protección adecuada de la máquina durante el tiempo de transporte largo (cinturones de seguridad, pernos de anclaje), así como protección y asistencia durante el transporte in situ.
Si la máquina no está equipada con los herrajes adecuados, es posible utilizar cualquier otro orificio o elemento disponible de suficiente durabilidad para garantizar que el generador y otras partes de la máquina estén correctamente equilibrados y estabilizados.
El peso de la máquina (unos 1.100 kg) debe tenerse muy en cuenta a la hora de planificar el transporte.
5.3 Instalación en el lugar de funcionamiento
Dependiendo del grado de complejidad de la máquina, la instalación en el lugar de operación debe ser realizada por el personal del Ordenante, habiendo leído este Manual de Operación y Mantenimiento o personal de servicio técnico del Fabricante, en cooperación con el personal del Ordenante.
Recuerde que la colocación e instalación adecuadas de la máquina de soldar son vitales para garantizar su funcionamiento óptimo, así como la comodidad y seguridad del operario en el entorno del aparato.
El Ordenante es responsable de la preparación del lugar para la instalación del dispositivo, la disponibilidad y preparación de las conexiones eléctricas y la realización de los requisitos particulares del diseño técnico y las pruebas de aceptación técnica que aprueban todo el generador para su uso.
El Fabricante proporcionará al Ordenante todas las instrucciones e información necesarias al respecto.
ATENCIÓN: Asegúrese de que el suelo / la superficie / los cimientos sobre los que se va a colocar la máquina tienen suficiente durabilidad, teniendo en cuenta el peso, la superficie y la distribución del peso de la máquina en sus puntos de apoyo (normalmente las patas).
ATENCIÓN: El dispositivo debe estar correctamente nivelado y debe tener lugar fijo de una operación.
El lugar óptimo de funcionamiento de la máquina de soldadura de alta frecuencia es la superficie de hormigón no cubierta o cubierta con una capa muy fina de material no conductor.
La superficie debe hacerse de acuerdo con el diseño particular siguiendo las normas de construcción y seguridad, así como siguiendo los requisitos relativos a las posiciones paralelas, perpendiculares y planas.
ATENCIÓN: El Ordenante es el único responsable de la realización de las condiciones mencionadas.
Tras la ubicación de la máquina de soldar en el lugar elegido, es necesario nivelar la máquina, comprobar su estado técnico y eliminar todos y cada uno de los defectos que se hayan podido producir durante el transporte. A continuación, desembalar, colocar, nivelar y fijar el generador. La lámpara del generador de alta frecuencia debe montarse al final del proceso de instalación. Esta tarea debe realizarse con especial atención, tanto al montar la lámpara en el zócalo/base como al conectar los contactos eléctricos de la lámpara. Conecte los conectores de la consola de control a las tomas debidamente marcadas de la prensa. Se recomienda que la instalación de la máquina después del transporte se realice bajo la supervisión directa de un representante del fabricante.
ATENCIÓN: Si las tareas antes mencionadas son realizadas por un representante del Cliente, las mismas deben ser realizadas estrictamente de acuerdo con la descripción contenida en este Manual de Operación y Mantenimiento y/o instrucciones proporcionadas por el fabricante durante la prueba de aceptación técnica.
Debido al campo magnético generado, no deben colocarse objetos metálicos de gran tamaño cerca de la máquina. La máquina puede afectar al funcionamiento de dispositivos electrónicos (radio, televisores, ordenadores) situados cerca de la máquina, como resultado de la alta sensibilidad de entrada de los dispositivos mencionados. El lugar óptimo de funcionamiento de la máquina es la superficie de hormigón no cubierta o cubierta con una capa muy fina de material no conductor.
5.4 Instalación en el lugar de funcionamiento
5.4.1 Información general
ATENCIÓN: El fabricante recomienda encarecidamente instalar la máquina sólo en entornos industriales.
La máquina objeto de este Manual de Operación y Mantenimiento ha sido diseñada y fabricada para trabajar en el entorno industrial para el procesamiento de cintas transportadoras.
Las condiciones específicas de funcionamiento de los dispositivos, es decir, la elevada humedad del aire, las altas temperaturas, el vapor y el polvo, han sido tenidas en cuenta por los diseñadores de la máquina y no afectan a su funcionamiento, sino que determinan requisitos más estrictos relativos a la ejecución de los programas preventivos.
La máquina no puede ser utilizada en atmósferas potencialmente explosivas, atmósferas muy polvorientas, ambientes con alta humedad y/o alta temperatura y presencia de vapores agresivos (ácidos, básicos, orgánicos o inorgánicos, con impacto potencial o factualmente corrosivo).
La temperatura del ambiente de trabajo debe oscilar entre +10º C y +40º C y la humedad relativa: entre 30% y 90%. No se permite la condensación de humedad atmosférica ni de sustancias agresivas en la superficie de la máquina (ni en ninguno de sus componentes).
Se requiere que la amplitud de temperatura a largo plazo durante el día en la sala de operaciones del generador no supere los 10º C y en el caso de humedad relativa: 10%.
La cláusula anterior no se aplica a los medios o sustancias utilizados para el engrase, conservación o sustancias no agresivas utilizadas en el curso de la producción / funcionamiento del dispositivo.
ATENCIÓN: Si existe una gran diferencia entre la temperatura exterior y la temperatura de la habitación donde está instalada la máquina, el aparato debe ponerse en marcha transcurridas 24 horas desde su montaje en la habitación.
5.4.2 Iluminación
Los requisitos relativos a la intensidad luminosa mínima establecen que, en la zona de funcionamiento horizontal, la iluminancia que puede aceptarse en las habitaciones en las que las personas permanecen durante un tiempo prolongado, independientemente de que se realicen actividades visuales, debe ser de 300 lx.
En el caso de actividades visuales cuyo nivel de dificultad sea superior a la media y cuando se requiera una gran comodidad de visión, así como cuando la mayoría de los operadores tengan más de 40 años, la intensidad luminosa requerida deberá ser superior a la mínima, es decir, al menos 500 lx.
5.4.3 Ruido
La máquina no genera ruido de un nivel que requiera el uso de medios o dispositivos de protección del personal.
No obstante, hay que tener en cuenta que cada entorno de trabajo tiene sus propias emisiones sonoras, que pueden repercutir en el nivel de ruido emitido por la máquina durante su funcionamiento.
5.5 Parámetros de conexión
5.5.1 Energía eléctrica
Conexión: 3 x 480V; 50Hz (3P+N+PE), protección contra sobrecorriente con propiedades retardadas. La instalación del Cliente debe garantizar medidas de protección contra descargas eléctricas conformes a la norma EN 60204-1:2001.
ATENCIÓN: Compruebe siempre la tensión del filamento después de instalar el tubo; consulte los datos técnicos del tubo.
5.5.2 Aire comprimido
Presión: 0,4 - 0,8 MPa, clase de limpieza exigida según ISO8573-1 4-4-4, consumo: 70 nl por ciclo.
ATENCIÓN: Si la presión en el sistema del usuario final es superior a 0,8 MPa, debe reducirse a unos 0,6 MPa con una válvula reductora montada en la conexión de la máquina de soldar.
5.6 Parámetros de conexión
Dependiendo de la complejidad del sistema y de las cualificaciones y licencias de los empleados, la conexión de la máquina de soldar en el lugar de su funcionamiento la realizan personas seleccionadas por el Ordenante o trabajadores del servicio técnico del Fabricante, en colaboración con el personal del Ordenante, por un precio adicional o de forma gratuita, lo que siempre se acuerda antes de la entrega de la máquina al Ordenante desde el lugar del Fabricante.
Siempre es necesario comprobar si todas las conexiones se han realizado de acuerdo con la documentación del aparato.
Hay que señalar que las tareas mencionadas requieren una cualificación adecuada del personal, incluidas las licencias pertinentes expedidas por los organismos competentes.
Se aplica tanto a las cualificaciones especializadas como a los cursos de formación finalizados y válidos en materia de salud y seguridad en el trabajo, incluidos en particular los riesgos que entrañan esas tareas.
6.0 Funcionamiento
6.1 Preparación de la máquina para el funcionamiento - Primera puesta en marcha
ATENCIÓN: Para utilizar la máquina de forma óptima y segura, lea atentamente y siga todas las instrucciones incluidas en este Manual de Operación y Mantenimiento.
ESTÁ PROHIBIDO ejecutar cualquier trabajo en la máquina de soldar por personas sin estar previamente formadas en el servicio de máquinas de alta frecuencia y normas de Seguridad Industrial con la especial consideración del posible riesgo procedente de la máquina.
Siempre que se hayan cumplido todos los requisitos de instalación y se hayan realizado las tareas descritas en el punto 5, estamos preparados para poner en marcha la máquina de soldar por primera vez en el entorno de producción del centro del ordenante.
ATENCIÓN: La primera puesta en marcha de la máquina debe realizarse en presencia y bajo la supervisión de los representantes del Fabricante.
6.2 Requisitos de funcionamiento - Instrucciones y directrices generales
Todos los ajustes y la calibración necesarios para el correcto funcionamiento de los parámetros del dispositivo han sido realizados por el Fabricante durante los procedimientos de montaje y pruebas internas. La conformidad general con los requisitos técnicos contractuales y el correcto funcionamiento de la máquina se confirman durante la aceptación técnica que tiene lugar en las instalaciones del Fabricante, en presencia de un representante del Ordenante y utilizando materias primas originales entregadas por el Ordenante para las pruebas.
ATENCIÓN: Debido a las propiedades específicas de los aparatos que emiten energía de alta frecuencia, es necesario realizar determinadas mediciones en el lugar de funcionamiento del aparato en el emplazamiento del Ordenante. Por la misma razón, es muy importante que el aparato tenga un lugar fijo de funcionamiento.
ANTES DE LA OPERACIÓN ES ABSOLUTAMENTE NECESARIO CONTROLAR:
- Eficacia de las medidas de protección contra descargas eléctricas;
- Tensión de alimentación - valor y corrección de la conexión de las fases;
- Sentido de giro del motor (si procede);
- Tensión de la lámpara de filamento incandescente;
ATENCIÓN: La tensión de la lámpara debe ser la misma que se especifica en la ficha técnica del producto - es posible ajustarla mediante derivaciones en el primario del transformador de incandescencia.
ATENCIÓN: Debido al carácter específico del dispositivo, siempre es necesario advertir e informar al personal sobre la alta tensión de alimentación del ánodo de la lámpara y el riesgo potencial de descarga eléctrica mortal por corriente eléctrica de la tensión de hasta 8000 VDC.
ATENCIÓN: La lámpara debe precalentarse durante aproximadamente una hora después de la instalación.
- Posición del soporte a la base de la mesa de trabajo;
- Emisión de campo electromagnético - después del ajuste de los parámetros de soldadura, durante el proceso de soldadura;
ATENCIÓN: La máquina de soldadura de alta frecuencia es una fuente de radiación electromagnética no iónica. Después de la instalación de la máquina en el lugar del comprador, la medición de la radiación no iónica se debe hacer. Las mediciones de radiación deben ser realizadas por una empresa autorizada.
ATENCIÓN: La máquina debe trabajar en un lugar de trabajo firme, ya que la transposición requiere una nueva medición de la intensidad de la radiación no iónica.
ATENCIÓN: Está prohibido que las personas con marcapasos implantado permanezcan en la zona de radiación no iónica activa.
ATENCIÓN: El Fabricante sugiere no emplear a ninguna mujer embarazada o en período de lactancia en la zona de radiación no iónica activa.
IMPORTANTE: Si los circuitos de alta tensión se han conectado accidentalmente al desconectar el ánodo o la lámpara del generador está defectuosa, los condensadores del filtro de alta tensión deben descargarse cortocircuitándolos con la carcasa durante muy poco tiempo.
ATENCIÓN: Todas las actividades durante la puesta en marcha y las mediciones, cuando el nivel de seguridad es más bajo (pantallas de protección abiertas, interruptores de llave bloqueados), deben llevar el menor tiempo posible, y el nivel de seguridad de funcionamiento completo de la máquina debe garantizarse lo más rápidamente posible.
ATENCIÓN: Todas las actividades de control y medición deben realizarse después de comprobar si los interruptores para el ajuste de la tensión anódica están en posición 0 - OFF (no se aplica a la medición de la emisión del campo electromagnético).
ATENCIÓN: Todas las actividades de control y medición deben ser realizadas exclusivamente por personal autorizado.
SIEMPRE ESTÁ PROHIBIDO iniciar el proceso de soldadura, es decir, encender la alta tensión de la lámpara, que inicia la tensión de alta frecuencia en el soporte aislado del electrodo, cuando el nivel de seguridad del funcionamiento del aparato es reducido.
La máquina está adaptada para trabajar en ciclo automático. El modo automático es el modo de funcionamiento estándar del aparato durante el proceso de producción.
La máquina de soldadura de alta frecuencia permite el funcionamiento en modo manual para realizar ajustes.
Los operarios de las máquinas deben llevar siempre ropa de trabajo estándar y calzado antideslizante.
El entorno de trabajo del aparato, el suelo y los soportes y asideros manuales deben estar siempre limpios y exentos de cualquier tipo de contaminación, grasa o barro, para reducir al mínimo posible el riesgo de resbalones o caídas.
No utilice nunca la máquina de trabajo sin los elementos de protección fijos o móviles. Compruebe periódicamente si todas las pantallas de protección y todos los demás elementos de protección están bien montados y funcionan correctamente.
Sólo las personas autorizadas, debidamente formadas en el manejo de la máquina y en Prevención de Riesgos Laborales, pueden tener contacto directo con la máquina.
Cada operador del aparato debe ser instruido sobre las funciones de los elementos de protección de la máquina y su correcta utilización.
En la zona que rodea el aparato (aproximadamente 1,5 m alrededor del generador y la prensa) no puede haber objetos que puedan interferir en el funcionamiento del aparato. Esta zona debe mantenerse limpia y disponer de una iluminación adecuada.
No utilice nunca los manipuladores de la máquina ni los tubos flexibles como soportes. Recuerde que cualquier movimiento accidental del manipulador del aparato puede iniciar accidentalmente el proceso de soldadura, cambiar parámetros o incluso provocar el fallo de la máquina o dañar sus herramientas.
ESTÁ OBLIGADO a informar al supervisor y/o al personal de tráfico sobre todos y cada uno de los casos de funcionamiento incorrecto del dispositivo.
6.3 Controles e indicadores a disposición del operador
Todos los mandos e indicadores de la soldadora se encuentran fácilmente en su construcción o en su pupitre de control. Antes de ponerse manos a la obra, el operario de la máquina debe familiarizarse con la disposición de los mandos e indicadores de la máquina, así como con las funciones que controlan.
A continuación se adjunta la lista completa de los controles e indicadores mencionados a disposición del operador:
- INTERRUPTOR PRINCIPAL - un interruptor (Fig.3) diseñado para conectar o desconectar el suministro eléctrico. 1-ON significa que el interruptor está encendido, mientras que la posición 0-OFF significa que el interruptor está apagado.
Fig.5. Disposición de los mandos e indicadores en el panel de control I: 2 - POWER; 3 - TWO-HAND CONTROL OFF/ON; 4 - HF; 5 - HF OFF/ON; 6 - USB; 7 - ETHERNET; 8 - RESTART; 9 - STOP; 10 - JOISTIC; 11 - START; 12 - electrodo arriba; 13 - giro a la izquierda; 14 - giro a la derecha; 14 - electrodo abajo.
-
POWER - indicador que parpadea en blanco cuando la máquina está conectada a la red eléctrica (Fig.5).
-
CONTROL A DOS MANOS OFF / ON - un interruptor de llave (Fig.5) para la activación del modo de control de la máquina a dos manos. El interruptor se refiere a los pulsadores situados en las empuñaduras negras y al electrodo para las funciones de subida y bajada en el joystick. El interruptor en la posición ON - significa que para activar los pulsadores se deben pulsar los dos pulsadores de la misma función, con lo que el joystick pierde la función de subida y bajada del electrodo. El interruptor en posición OFF indica la posibilidad de control mediante un solo pulsador y que la subida y bajada del electrodo se realiza mediante el joystick.
¡ATENCIÓN! Conmutación fuera de el a dos manos control modo hace que el trabajo operaciones más fácil; sin embargo it significativamente aumenta la siniestralidad riesgo. Sólo un autorizado y correctamente capacitado, persona responsable debería haber la llave del interruptor de encendido/apagado.
-
HF - cuando el indicador parpadea en amarillo significa que el proceso de soldadura HF está activado (Fig.5).
- HF OFF/ON - un interruptor con el que se puede liberar o retener la corriente de AF (cuando está en OFF significa que no se puede realizar la soldadura HF)
En lo que respecta al procedimiento de soldadura estándar, el HF OFF/ON debe estar en EN posición.Cuando el interruptor HF OFF/ON se coloca en la posición OFF significa que el ciclo de trabajo se puede realizar sin liberar la corriente HF.
-
Ranura USB - una ranura (Fig.5) en la que se puede insertar una tarjeta de memoria USB para el almacenamiento de los parámetros de soldadura y el historial de mensajes; también permite guardar las recetas almacenadas en el panel HMI.
-
RanuraETHERNET - una ranura (Fig.5) en la que se conecta el cable Ethernet cuando se requiere el diagnóstico de la máquina en línea que permite el acceso a Internet a la máquina.
-
RESTART - el pulsador azul (Fig.5), que debe utilizarse para reiniciar el sistema de control y protección de la máquina siempre que aparezca el mensaje de alarma en el panel HMI.
-
STOP - el pulsador negro (Fig.5) sirve para desconectar el proceso de soldadura de alta frecuencia.
-
JOYSTIC - joystick (Fig.5, Fig. 7) utilizado para el avance y retroceso del cabezal del electrodo de soldadura así como la conducción de la máquina hacia la izquierda o hacia la derecha con un arranque lento para facilitar el posicionamiento. Sin embargo, con el joystick sólo se puede bajar o subir el electrodo cuando está activado el modo a dos manos. Hay dos velocidades de desplazamiento:
- "lento" - (Fig. 6 - A, C, E, G) velocidad de movimiento determinada por el parámetro situado en el panel de menú Servicio HMI - Velocidad de accionamiento MANUAL - LENTO.
- "rápido" - (Fig. 6 - B, D) velocidad de movimiento determinada por el parámetro situado Menú de servicio panel HMI - Velocidad de accionamiento MANUAL - RÁPIDO.
Fig. 6. Posiciona el joystick:
A - lento mover de la cabeza a la izquierda, B - rápido mover de la cabeza a la izquierda,
C - lento mover de la cabeza a la derecha,
D - rápido mover de la cabeza a la derecha,
E - electrodo arriba,
F - electrodo abajo,
-
START - el pulsador verde (Fig.5) se utiliza para conectar el proceso de soldadura de alta frecuencia .
-
arriba flecha - dos pulsadores en el negro asas en el panel del operador (Fig. 5, Fig. 7) usado para activación de el electrodo en superior posición. Cuando el a dos manos operación modo es activado, ambos los pulsadores deben sea pulsado simultáneamente
-
izquierda flecha - dos pulsadores en el negro asas en el panel del operador (Fig. 5, Fig. 7) permitiendo el máquina a mover izquierda. En el a dos manos operación modo es activado, ambos pulsadores debe sea pulsados simultáneamente.
-
derecha flecha - dos pulsadores en el negro asas en el panel del operador (Fig. 5, Fig. 7) obligatorio permitiendo el máquina a mover Bien. Cuando el a dos manos operación modo es activado, ambos pulsadores debe simultáneamente.
-
abajo flecha - dos pulsadores en el negro asas en del operador panel (Fig. 5, Fig. 7) usado para activación de el electrodo en menor posición. En el a dos manos operación modo es activado, ambos pulsadores debe sea prensas en el mismo tiempo.
Fig. 7. La disposición de los mandos y indicadores un el panel de control :
12 - electrodo arriba;
13. gire a la izquierda; 14. gire a la derecha;
14. electrodo abajo
15. CORRIENTE DE ÁNODO;
16. TEMPERATURA DEL ELECTRODO;
17. PARADA DE EMERGENCIA;
-
CORRIENTE ANODAL - el amperímetro de panel (Fig.5) debe indicar el valor de la intensidad de corriente en el circuito anódico La y debe permitir al operador realizar la inspección visual del proceso de soldadura (Las características a plena carga del generador).
-
TEMPERATURA DEL ELECTRODO - un termorregulador (Fig.6) utilizado para el ajuste de la temperatura del electrodo . Este controla el sistema que estabiliza la temperatura del electrodo . Un botón , Temp Regulation en la pantalla principal ventana de el panel táctil se utiliza para activar la función de estabilización de la temperatura . El manual del usuario referente a la temperatura E5CC puede encontrarse en el anexo .
Fig. 8 Panel de control;
18.- PARADA DE EMERGENCIA;
19. - HMI; - EMERGENCIA STOP - el rojo cabeza de seta pulsador (Fig.5) it es a botón que debe sea pulsado sólo cuando el funciones de el máquina necesita a sea detenido inmediatamente o cuando cualquier cosa en relación con de la máquina funciones o el del operador alrededores posar a amenaza a la producción o seguridad.
En EMERGENCIA STOP botón debe no sea sobreutilizado, it es supuesto a sea usado sólo en caso de emergencia.
-
PANEL HMI - el panel sensible al tacto (Fig.5) debe utilizarse para cambiar los parámetros de ajuste de la máquina y se supone que se convierte en una fuente fiable de información sobre el estado actual de la máquina de soldar. Consulte el capítulo 6.6. para obtener más información sobre el procedimiento de mantenimiento del panel táctil.
Fig.9. EL SISTEMA DE PREPARACIÓN DE AIRE COMPRIMIDO 1 .
-
AIRE COMPRIMIDO PREPARACIÓN SISTEMA (Fig.9) - consta de:
A. El terminal de aire comprimido al que debe conectarse la manguera de aire comprimido. La manguera debe suministrar al sistema aire comprimido de 0,4 a 0,8 MPa;
B. En manualmente operado comprimido aire cierre válvula (en pedir para abrir la válvula - vuelta a la izquierda y fijar a Posición ON; a gire a la derecha - la posición OFF - la válvula está cerrada);
C. En comprimido aire terminal en que el comprimido aire manguera debe sea conectado. En manguera es supuesto a proporcionar el sistema con el rango de aire comprimido de 0,4 a 0.8 MPa; 0,6 M
El nivel de presión del sistema neumático nunca supera el nivel de presión que propulsa la máquina.
D. El filtro de aire comprimido junto con el mecanismo de liberación del agua de condensación;
E. El manómetro que indica el nivel de presión en el sistema de aire comprimido de la máquina;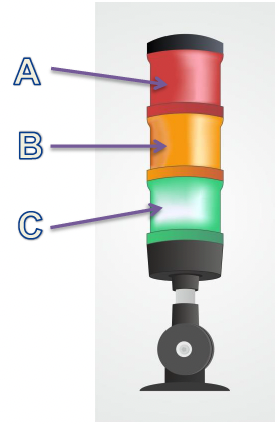
Fig.10. La columna luminosa de señalización:
A - rojo color;
B - color naranja ;
C - color verde
21.COLUMNA DE LA LUZ DE SEÑALIZACIÓN (Fig.10):
A. Color rojo indica fallo y a la misma hora el mensaje de alarma debe mostrarse en el panel táctil HMI .
En alarma masajes son suprimido y el rojo luz en el columna de luz de señalización deja de parpadear cuando el REINICIAR está pulsado.
En caso de que los esfuerzos fueran en vano y el mensaje de alarma de alarma sido borrado cuando el REINICIAR botón había sido pulsado así que podría significar que el causa de fallo ocurrencia había no aún no se había eliminado.
Véase capítulo 6.6.2. para más información en información aplicación de a la página masajes de alarma.
B. El color naranja indica que la soldadora de alta frecuencia empieza a funcionar.
C. El color verde indica que la máquina está lista para trabajar.
Fig. 11. Uno de los indicadores láser colocados en el lado derecho de el cabezal de soldadura .
22. Láseres instalados en el cabezal de soldadura (Fig. 11) utilizados para la proyección de la línea de soldadura sobre el material soldado/sellado . Útiles para colocar y posicionar el material a lo largo de la línea de soldadura . Se encienden directamente desde el panel táctil HMI.
|
|
El láser es para marcar la línea SOBRE el MATERIAL en la posición de el electrodo y su soporte arriba. El láser NO / NO DEBE brillar sobre el borde delantero o borde trasero de el electrodo xml-ph-003
Procedimiento de regulación láser:
1. Coloque el material sobre la mesa y baje el soporte con el electrodo sobre la mesa,
2. Trace con un rotulador una línea que delimite el borde delantero y, en su caso, el trasero del electrodo (si hay dos láseres montados en un mismo lado),
3. Levante el electrodo y ajuste el láser o los láseres a las líneas trazadas, posiblemente con un desplazamiento de estas líneas tal como el operario desee posicionar la lámina,
4. Tenga cuidado de que el material no se mueva.
|
|
Fig. 12 El parachoques
23. Los parachoques laterales instalados en ambos lados de el cabezal de soldadura (Fig.9 ), impiden que la máquina colisione con cualquier persona o cualquier cosa. Cualquier sacudida sobre un parachoques tendrá como resultado la desconexión instantánea del sistema de propulsión de la máquina; esto será indicado por el mensaje : OPEN xml-ph-
Fig. 13 Movimiento de emergencia
23. Emergencia mover - el interruptor se utiliza para cambiar el modo de funcionamiento . En caso de un obstáculo y detener en él. El interruptor desactiva los parachoques laterales y permite la salida de un obstáculo. Después de conmutar el interruptor a la posición I en la HMI, la "emergencia dispara" ventana aparece en que el usuario tiene la opción de utilizando las flechas de navegación para pasar la soldadura cabeza izquierda o Al conmutar el interruptor a la posición 0 se activan los parachoques laterales y se restablece el correcto funcionamiento de la máquina modo.
|
|

Finales de carrera para la altura de del electrodo:
- límite superior interruptor - cuando encendido (Fig. 14- A) indica la posición superior del electrodo . El ajuste de la corredera , que activa el interruptor , debe realizarse cuando la posición superior máxima del electrodo ha de ser modificada. Si el interruptor de límite se desplaza demasiado alto, se no no conmutará en en la posición superior del electrodo - el ciclo de soldadura no se finalizará y el ciclo de accionamiento de la máquina no se podrá realizar. Si en la otra mano, está está demasiado bajo - el electrodo no será elevado a una altura suficiente después del ciclo de soldadura y puede atrapar el material soldado durante su accionamiento, causando daños.
- Límite inferior interruptor - cuando apagado (Fig. 14-B) indica la posición inferior del electrodo por encima de la mesa de trabajo . El ajuste de la corredera en este interruptor debe realizarse cada vez que el electrodo ha sido sustituido (cuando el nuevo electrodo es de una altura diferente a la anterior ) y cuando se produce un cambio significativo en el espesor del material soldado . El final de carrera inferior interruptor es también un elemento de el sistema que protege las manos del operador de ser aplastadas. Si su ajuste no se realiza correctamente, la protección antiaplastamiento (ZTG Anti-CRUSH) función se activará provocando la elevación automática de el electrodo en su posición superior. El final de carrera debe estar colocado a una altura que haga que la rueda rodante del final de carrera sea presionada en por la corredera inferior de la altura del electrodo situado en la varilla de el momento en que el electrodo toca el material soldado. (Fig. 14- B).
Fig. 14 Finales de carrera que indican la posición del electrodo:
A - posición superior;
B - posición inferior.
Ajuste procedimiento y la determinación de el correcta altura de el final de carrera inferior:
- colocar el material a soldar sobre la mesa de trabajo,
- coloque el electrodo en el portaherramientas y bloquéelo ,
- baje el portaelectrodo con el electrodo sobre el material , de manera que el electrodo apenas lo toque sin ninguna presión (deje un espacio de máximo 5mm / 1/8inch); deje en esta posición.
- mueva el deslizador metálico inferior de la varilla hasta la posición que desconectará el final de carrera inferior (el rodillo interruptor está directamente sobre el deslizador (Fig. 14- B),
- si no es posible situar la corredera metálica a una altura adecuada debido a su ajuste escalonado (cada 15 mm), afloje los dos tornillos que sujetan el final de carrera y colóquelo en posición de bloqueo con el rodillo a la corredera metálica inferior de la altura del electrodo (Fig. 14- B), luego apriete los tornillos.
- levante el mango con el electrodo hasta su posición superior,
- si no es posible colocar el indicador a una altura adecuada debido a su ajuste escalonado (cada 15 mm), afloje los dos tornillos que fijan el interruptor y colóquelo en una posición tal que desplace su rodillo hasta el indicador inferior de la altura del electrodo (Fig. 14- B), luego apriete los tornillos.
¡ATENCIÓN! Queda terminantemente prohibida la manipulación con el final de carrera que indica la posición inferior del electrodo excluyendo la citada anteriormente. La inobservancia de la advertencia del fabricante puede provocar una avería grave de la máquina y, como consecuencia, graves lesiones corporales.
En además, la máquina ha sido equipado con un electrodo adicional adicional que permite soldar sin la uso de conexión a tierra de tierra. Después de instalar este tipo de electrodo en el soporte y iniciar a bajar a bajarlo, un adicional límite adicional que inhibe inhibe el movimiento del electrodo electrodo de puesta a tierra.
6.5 Controlador de temperatura de funcionamiento E5CC
Temperatura control unidad se utiliza para controlar la temperatura de el electrodo. Programar la temperatura correcta de el electrodo es necesario para corregir el curso de el proceso de soldadura . La temperatura debe ser seleccionada experimental. A continuación se una descripción de la pantalla y control panel unidad de control de temperatura (Fig. 15).
Fig. 15. Pantalla y panel de control termorregulador.
- Pantalla con cuatro dígitos (blanco) que muestra valor real de temperatura . En el modo de ajuste de parámetros muestra el signo actual del parámetro editado.
- Visualización con cuatro dígito (verde) que visualizado real ordenado valor de temperatura. En parámetro ajuste modo visualización actual real valor de parámetro editado.
- Botones de control:
mover botón. Pulsando este botón causa a editar siguiente dígito del número editado.
- botón "ABAJO" causa baja editado dígito por uno.
- Botón "UP" para aumentar el dígito editado por uno.
En el edición de parámetros vaya a siguiente parámetro
Largo pulse este botón (min 3seg.) causa pase a edición modo de dejar parámetro. Si sistema trabajo en edición modo, pulsando botón causa retorno a el ventana principal
AJUSTES DEL CONTROLADOR - ORDENADO VALOR DE TEMPERATURA
A cambiar pedido valor necesita a corto pulse botón (Fig. 15) o
. Provoca el paso al modo de edición de parámetros. El número disponible que se editará se señaliza mediante un parpadeo rápido. Con los botones "UP"
o "ABAJO
ajuste el valor de este número, a continuación pulse el botón "mover".
que se mueven a la siguiente posición a editar.
6.6 Programación y manejo del panel táctil HMI
¡ATENCIÓN! Cada valor del parámetro representado en los gráficos de este manual se toma al azar y debe ser ignorado por el operador de la máquina. Los valores de los parámetros deben derivarse de la experiencia práctica del usuario, ya que pueden variar profundamente en función del tipo de material soldado o de la instrumentación implementada.
En el panel HMI, todos los valores editables de los parámetros se muestran sobre un fondo de color blanco. Para visualizar un parámetro, el usuario debe pulsar su valor y, como resultado, se abrirá el teclado en pantalla. Los datos pueden guardarse pulsando la tecla Intro.
6.6.1 Conexión a la fuente de alimentación
Poco después de conectar la máquina a una fuente de alimentación, en la pantalla de la HMI aparece una ventana de alarma con el siguiente mensaje:
#A001 PARADA DE EMERGENCIA
#K001 PULSE EL BOTÓN DE REINICIO
De acuerdo con esta situación, la máquina necesita ser reiniciada por lo que se debe pulsar la tecla azul RESTART . A continuación hay que esperar 30 segundos hasta que la máquina esté lista para trabajar y entre en modo de espera que conocemos por los siguientes hechos: un indicador luminoso en la columna de señalización luminosa parpadea en verde y la barra de progreso visualizada en la ventana principal de la HMI parpadea en verde. En caso de que el mensaje de alarma no desaparezca de la pantalla de la HMI, consulte el capítulo 0.
6.6.2 Mensajes de alarma
Cuando se produce un fallo en la máquina o cuando se activa uno de los sistemas de protección o cuando se detectan otras anomalías en el funcionamiento de la máquina, se muestra uno de los mensajes de alarma en el panel táctil de la HMI. Todos los mensajes de alarma se borran con la ayuda de la tecla RESTART .
Los tipos de masajes con alarma:
#A001 EMERGENCIA STOP - este tipo de mensaje se muestra cuando:
- la máquina está conectada encendida - el circuito de seguridad de la máquina debe comprobarse siempre que se pulse la tecla RESTART ,
- el rojo cabeza de seta EMERGENCIA STOP pulsador fue pulsado y ha sido atascado. Necesita para ser desatascado girando su cabeza hacia la derecha.
#A002 TUBO TEMPERATURA - este tipo de masaje significa que o bien la onda viajera tubo refrigeración no existe o bien que el sistema de refrigeración falla y se se muestra cuando:
- los fusibles que se supone para proteger el circuito de alimentación de de el ventilador que debe enfriar el tubo de onda viajera están desconectados;
- el contactor que debe accionar el ventilador que debe enfriar el tubo está apagado o dañado;
- el tubo térmico protección sistema se pone en operación que significa que el onda viajera tubo Tengo con calefacción arriba a demasiado alta temperatura y como resultado la tubo pasador de banda pin que tenía ha sido conectado a el límite cambiar por un el cable se desoldó.
Fig.16. El sistema de protección térmica del tubo.
Se suelda una chaveta a la banda del tubo con la ayuda de una soldadura de punto de fusión mucho más bajo que aquel en el que el tubo se sobrecalentó (se dañó). Si la temperatura de la lámpara aumenta demasiado, la chaveta se saldrá de la banda y, como resultado, se disparará el interruptor de límite, al mismo tiempo que aparecerá el mensaje de alarma y se cortará el suministro de energía para el resplandor del tubo. Entonces deberá eliminarse la causa del sobrecalentamiento.
¡ATENCIÓN! El cable no debe sujetarse a ninguna otra parte de la máquina, salvo a la chaveta de la banda que se ha atornillado al tubo. La inobservancia de la advertencia citada puede ocasionar el bloqueo del final de carrera, lo que puede provocar el sobrecalentamiento del tubo de la onda viajera y, como consecuencia de ello, su deterioro.
If the cotter pin gets separated from the band than the band should be taken off from the tube, the pin should be soldered to the band with the standard solder used in electronic engineering (Melting point < 190oC) para que la pieza reparada pudiera volver a fijarse al tubo.
El sobrecalentamiento del tubo puede ser causado por:
- la suciedad encontrada en el generador o en el radiador tubular;
- el fallo del ventilador de refrigeración del tubo o el fallo del sistema de alimentación del ventilador;
- la obstrucción de los orificios de ventilación de la máquina o por la excesiva cantidad de tierra recogida por los filtros instalados en los orificios de ventilación;
- la temperatura ambiente excesiva.
#A003 ANTIFLASH - este tipo de masaje significa que el sistema de protección contra un arco-sobre durante la soldadura se disparó - debido a este mensaje asegúrese de que ni la almohadilla aislante, material soldado ni el electrodo de soldadura no habían sido dañados.
#A004 SOBRECARGA DE ÁNODO - este mensaje significa que se ha superado el límite de elevación de ánodo, por lo que es necesario ajustar los parámetros que se aplican a la potencia liberada en la soldadura.
#A005 SOBRECARGA DE RED - este mensaje significa que se ha superado el límite de subida de red, por lo que es necesario ajustar los parámetros que se aplican a la potencia liberada en soldadura.
#A006 BAJA PRESIÓN DE AIRE - este mensaje significa que hay falta de presión de aire o que el nivel de presión de aire es demasiado bajo en el sistema neumático. Asegúrese de que la manguera que suministra el aire comprimido está conectada a la máquina o de que el nivel de aire comprimido es adecuado y, a continuación, con la ayuda del regulador de la válvula reductora de presión que se puede encontrar en el sistema de preparación de aire comprimido, ajuste la presión en la máquina al nivel adecuado.
#A008 ELECTRODO NO ESTÁ EN POSICIÓN SUPERIOR -. se visualizará el mensaje si el electrodo de soldadura no está en la posición superior después de encender la máquina. Comprobar la estanqueidad de el sistema neumático y el ajuste correcto de el interruptor de fin de carrera que indica la posición superior .
#A011 TEMPERATURA DEL ELECTRODO - este mensaje señala que el punto de ajuste temperatura del electrodo en el termorregulador ha sido superado - la máquina será desactivada en modo de emergencia . Usted debería esperar hasta que el electrodo se enfríe y entonces compruebe si el ajuste de temperatura en el termorregulador es demasiado alto. Otra posible opción es que el circuito de calentamiento del electrodo se haya averiado . En tal caso, deberá ponerse en contacto con el servicio del fabricante .
#A013 SOLDADURA PARÁMETROS NO ALCANZADOS - el software de control de la máquina incluye un algoritmo que comprueba si cada soldadura parcial se ha realizado correctamente. Si, durante la soldadura , los parámetros establecidos fuera no se han alcanzado o si la soldadura se ha detenido antes de que la tarea haya finalizado, se mostrará el mensaje arriba . La calidad de la soldadura se comprobará y si no es satisfactoria, la tarea deberá repetirse .
#A019 SENSOR / ACCIONAR ERROR - ELECTRODO ABAJO - el mensaje de alarma será visualizado cuando, después de accionar la válvula bobina, el controlador no reciba confirmación de el sensor confirmando la consecución de la posición inferior en 15 segundos. Compruebe si el sensor ha no movido o compruebe que el sistema neumático está cerca de el actuador.
#A020 SENSOR / ACCIONAMIENTO ERROR - ELECTRODO ARRIBA - el mensaje de alarma se visualizará cuando, después de accionar la válvula bobina, el controlador no reciba confirmación del sensor confirmando la consecución de la posición superior en 15 segundos. Compruebe si el sensor no se ha movido o compruebe que el sistema neumático está cerca del actuador.
#A032 START POSICIÓN DEL CAPACITADOR NO ALCANZADA - se visualizará el mensaje si los condensadores no alcanzan la posición preajustada en 15 segundos. Compruebe el accionamiento del condensador .
#A034 EMERGENCIA ELECTRODO ARRIBA - este mensaje se visualiza cuando el electrodo soporte que estaba siendo bajado sobre la mesa de trabajo encontró un obstáculo obstáculo en su camino y el sistema de protección contra aprisionamiento peligro se puso en práctica. Asegúrese de que no hay nada entre el electrodo y la mesa de trabajo . Si la alarma mensaje no desaparece el ajuste de el interruptor límite indicando la posición inferior del electrodo necesita ser conducido. Véase el capítulo 6.4. para más información aplicando a el procedimiento de ajuste del interruptor límite .
#A035 COMPROBAR REINICIAR CIRCUITO EN RELÉ DE SEGURIDAD - significa que el circuito de seguridad de la máquina ha probablemente sido dañado. En tal caso deberá ponerse en contacto con el servicio del fabricante .
#A046 CORRIENTE NO EN TOLERANCIA DURANTE SOLDADURA - este mensaje se mostrará si el valor actual no puede alcanzarse durante las operaciones El algoritmo comprueba si la corriente anódica se ha alcanzado . La corriente anódica obtenida debe estar dentro +/- del rango de tolerancia de el valor de la corriente _COPY9 anódica para un porcentaje dado de el tiempo para la duración de la soldadura, especificado en la Ventana de Servicio después de elegir la opción de control delproceso de soldadura.
#A047 FUERZA ABAJO NO EN TOLERANCIA DURANTE LA SOLDADURA -este mensaje será mostrado si, durante soldadura, la corriente fuerza descendente cae fuera del rango de tolerancia especificado en la Ventana de Servicio después de elegir Proceso de soldadura control opción.
#A053 FRENODE EMERGENCIA - Este mensaje se visualiza cuando se pulsa el interruptor de seguridad . Cuando el interruptor seta se activa en caso de emergencia, el cabezal frenará repentina - y violentamente - .
#A054 SEGURIDAD VÁLVULA DAÑOS - Este mensaje se visualiza cuando el sensor (marcado con el símbolo 10B1 en el diagrama eléctrico ) de confirmación pistón válvula en la posición apropiada se activa. Este sensor está situado en la válvula de seguridad (marcada con el símbolo 1V3 en el diagrama eléctrico ). Si el pistón de válvula de seguridad no alcanza la posición correcta, ello significa que la válvula no funciona xml-ph-0030
#A055 SERVO ALARMA - esto señala un error en el accionamiento del eje Y . Reinicie la máquina y, si el mensaje no desaparece, compruebe el número de alarma visualizado en el servo y compruebe la descripción en el xml-ph-003
#A056 BAJA PRESIÓN DE AIRE EN CILINDROS DE SOPORTE - significa que presión de aire en los servomotores de soporte del electrodo es demasiado baja que puede resultar en un rápido descenso de el electrodo y lo golpeando xml-ph-0030@dee El ajuste de la presión del aire comprimido en el circuito de estos servomotores debe realizarse .
#A057 SOLDADURA POSICIÓN NO ALCANZADA - el mensaje de alarma será visualizado cuando, después de controlar la válvula bobina, el controlador no reciba confirmación de el sensor confirmando el logro de la posición ajustada en 8 segundos. Compruebe si el sensor ha no movido o compruebe la estanqueidad del sistema neumático en el actuador.
#A058 ELELECTRODO ESTÁ NO LOCALIZADO EN UNA POSICIÓN ABAJO - el mensaje de alarma será visualizado si el botón START es presionado y el electrodo está no en la posición abajo . Bajo xml-ph-0
#A059 TABLA - ERROR DE AJUSTE POSICIÓN - El mensaje alarma se visualizará si el controlador no recibe confirmación de el sensor de que la posición deseada ha sido alcanzada dentro de 8 segundos de xml-ph-0030@deepl.i Compruebe que el sensor está en posición y compruebe también la estanqueidad del actuador.
#A060 EMERGENCIA REBOTE - EJE X INICIO/ FINAL - El mensaje de alarma #A061 X-AXIS BASING ERROR se visualiza, junto con la alarma , cuando el interruptor final , situado en el cabezal , se activa. En ese momento, el cabezal se desviará y el sistema explotará.
#A061 EJE X ORIENTACIÓN ERROR - El mensaje se visualiza cuando el interruptor de fin de , situado en el cabezal , se activa. Este puede ser debido a que el operador ha introducido una incorrecta, tabla longitud va una superior que la longitud real- en el Movimientos ajustes en el servicio menú . Un error de base también puede ocurrir en el caso de un activo punto final después de la base.
#A062 SET PRESSURE HAS NOT BEEN ACHIEVED - Se visualizará el mensaje si el valor especificado de el parámetro pressure es inferior que el rango inferior de tolerancia , especificado en la ventana de servicio en los parámetros de control del proceso de soldadura.
#A063 EMERGENCIA REBOTAR - EJE Y ARRANCAR/ TERMINAR - El mensaje de alarma #A061 EJE Y BASE ERROR se visualiza, junto con la alarma , cuando el interruptor final , situado en el cabezal, se activa. En ese momento, el cabezal se desviará y el sistema explotará.
#A064 EJE Y ORIENTACIÓN ERROR - El mensaje se visualiza cuando el interruptor de fin de carrera , situado en el cabezal , está activado. Este puede deberse a que el operador ha introducido un incorrecto "Eje Y arriba xm un más alto que el valor en los ajustes Movimientos en el menú servicio . Un error basing puede ocurrir también en el caso de un punto final activo después del basing.
#A075 DRIVE ERROR - la alarma mensaje se visualiza cuando se produce una alarma en el inversor. Si la alarma no puede ser borrada, compruebe el número de alarma visualizado en el inversor visualizar y comprobar su explicación en la documentación técnica del fabricante.
#A076 OPEN GUARD - se visualiza cuando uno de los escudos se quitado - los escudos están equipados con los interruptores de llave- que se encienden se encienden sólo si los escudos están debidamente colocados y apretados.
#A077 DRIVE COMUNICACIÓN ERROR - la alarma se mostrará si no hay comunicación PLC = Variador. Compruebe que los conectores del cable no estén retirados.
#A080 INCORRECTA LONGITUD DE SOLDADURA - un mensaje de alarma se mostrará si la soldadura es imposible de realizar, porque la longitud de la soldadura es mayor que la longitud de la tabla ello significa si el operador quiere iniciar el ciclo en modo BA conducir pero introdujo la longitud de soldadura para el modo AB . Compruébelo:
- la cabeza es en el principio de la tabla, o en el final dependiendo en la elección del AB-BA modo de accionamiento ,
- pasando los parámetros se han introducido correctamente en la ventana HF HEAD DRIVE,
- la tabla real longitud está correctamente introducida en la ventanaMENÚ DE SERVICIO .
#A102 PARAGOLPE IZQUIERDO - COLISIÓN - el mensaje se visualiza cuando el paragolpes izquierdo se activa. En caso de parada en un obstáculo (parachoques activo), gire el interruptor deEMERGENCIA MOVER desactive el sistema de emergencia y utilice la HMI para mover la cabeza salir del obstáculo.
#A103 PARAGOLPE DERECHO - COLISIÓN - el mensaje se visualiza cuando el paragolpes derecho se activa. En caso de parada en un obstáculo (parachoques activo), gire el interruptor EMERGENCIA MOVER desactive el sistema de emergencia y utilice la HMI para mover la cabeza salir del obstáculo.
6.6.3 Pantalla de alarma - Movimiento de emergencia
La ventana MOVIMIENTO DE EMERGENCIA se visualiza cuando el interruptor de emergencia se conmuta a posición I (Fig. 13 Movimiento de emergencia ). En la ventana , el operador tiene la opción de pasar la soldadura cabeza derecha o izquierda a velocidad lenta . El movimiento de la cabeza se realiza por medios de navegación flechas indican
Fig. 17 Movimiento de emergencia
Operación en el máquina es sólo posible cuando el TRASLADO DE EMERGENCIA interruptor está en posición 0.
En la parte superior de la pantalla táctil de la HMI hay un menú con el que el usuario puede elegir una de las cinco ventanas virtuales principales, a saber:
- Pantalla principal
- Base de datos de recetas
- Ajuste de potencia
- Gráfico de trabajo
- Menú de servicio
6.6.5 Pantalla principal
Fig.12. Pantalla principal.
Receta - bajo este nombre se puede encontrar un grupo de parámetros que se aplican al ciclo de trabajo. Una vez establecidos los parámetros de soldadura para el tipo concreto de producto derivados de la experiencia práctica (los valores de los parámetros dependen en gran medida del tamaño de la soldadura, el tamaño del material soldado y la forma del electrodo), deben introducirse en el sistema y guardarse con el nombre de la receta.
ATENCIÓN En es importante a recuerde que en rencor de el hecho de que el sobre mencionó parámetros puede sea guardado en el recetas nombre en el HMI táctil panel allí es también otro parámetro - ELECTRODO TEMPERATURA que debe ajustarse manualmente.
Además, junto al nombre de cada parámetro aparecen dos valores en la pantalla de la HMI. El primero (sobre fondo azul) es el valor del parámetro de funcionamiento actual visualizado en tiempo real, el segundo (sobre fondo blanco) es el valor ajustado procedente de la receta de producción o de los datos del operador.
En caso de necesidad, el operador siempre puede pulsar el dígito sobre el fondo blanco y cambiar su valor. El valor del parámetro de funcionamiento actual se actualizará de inmediato, aunque el cambio no afectará a la receta ejecutada.
Para guardar en una receta los cambios realizados en la pantalla principal, pulse el botón GUARDAR RECETA para copiar los parámetros de la pantalla principal en la barra Editar receta de la ventana Base de datos de recetas. Los parámetros copiados pueden guardarse como una nueva receta utilizando el botón Crear nueva o pueden utilizarse para actualizar una receta existente utilizando el botón Actualizar.
El signo rojo en la HMI panel en la ventana principal Fig. 19 indica que la máquina no está lista para funcionamiento. Los botones en el panel HMI y en el panel del operador están inactivos hasta que el operador reinicie la máquina con el botón azul RESTART en el panel del operador. La selección del botón RESTART tiene el mismo efecto que conectar el circuito de seguridad e iniciar el proceso de subencendido de la lámpara de generación durante 30 segundos. Durante este tiempo, la barra de progreso se vuelve gradualmente verde (Fig. 20 ), y los botones permiten al cabezal pasar sobre los ejes X y Y mientras los botones que permiten al cabezal dejar caer sobre el banco de trabajo están activos; sin embargo, es no posible a cambiar a xml-ph-00 Una vez que la barra de progreso esté completamente verde, aparecerá LISTO en la barra de progreso y a partir de ese momento, todos los botones , incluidos los botones de alta frecuencia, activación , estarán activos.
Fig. 19 Información NO LISTO mostrada en panel HMI
Fig. 20 Barra de progreso llenándose gradualmente en verde tras seleccionar botón RESTART en el panel de control
Nombre: - El nombre de la receta ejecutada a efectos de producción.
Potencia inicial - este parámetro indica la posición (capacidad) del condensador de salida que se encuentra en el generador; la intensidad de la corriente anódica en la fase inicial de la soldadura de alta frecuencia depende en gran medida del valor de este parámetro. (Parámetro expresado en valores porcentuales, donde 0% indica el nivel más bajo de capacidad - el nivel más bajo de intensidad de corriente anódica y 100% indica el nivel más alto de capacidad - el nivel más alto de intensidad de corriente anódica).
El valor del parámetro Potencia inicial y el valor de la corriente anódica (potencia liberada en el material) no dependen linealmente, por lo que deben tomarse las medidas de precaución adecuadas al ajustar los valores de este parámetro.
El valor actual del parámetro Potencia inicial y el valor del parámetro Ajuste son iguales entre sí sólo en la fase inicial del procedimiento de soldadura. Cuando se inicia el procedimiento, la posición del condensador de salida se ajusta automáticamente para alcanzar la potencia de funcionamiento.
Potencia de trabajo [A] - este parámetro indica la corriente de ánodo Ia utilizada para soldar. (Parámetro expresado en valores de amperios que van de 0 a 4 A.)
Los valores en color verde en la escala del medidor de corriente anódica indican los valores aceptables de la corriente anódica Ia.
Cuando se inicia el procedimiento de soldadura, el condensador de salida (potencia inicial) se ajusta automáticamente para alcanzar la potencia de funcionamiento.
Tiempo de retardo [s] - este parámetro indica el tiempo durante el cual el electrodo se ha adherido al material soldado antes de iniciarse la soldadura. (Parámetro expresado en valores de segundos que van de 0 a 99 s.)
Tiempo de soldadura [s ] - este parámetro indica el tiempo que tarda la máquina en procesar la soldadura de alta frecuencia. (Parámetro expresado en valores de segundos que van de 0 a 99 s.)
Tiempo de enfriamiento [s] - este parámetro indica el tiempo en el que el electrodo ha sido presionado contra el material soldado tras finalizar la soldadura - el material se enfría al ser presionado contra la mesa. (Parámetro expresado en valores de segundos que van de 0 a 99 s .).
Nivel de potencia [0-6] - es el ajuste principal de la potencia de la máquina; el ajuste se realiza cambiando la tensión del ánodo Ua en el rango de 1 a 6, donde 1 es potencia baja y 6 es potencia máxima:
0 - el transformador de ánodo está desconectado;
1 - Ua = 3,4kV;
2 - Ua = 3,95kV;
3 - Ua = 4,75kV;
4 - Ua = 5,87kV;
5 - Ua = 6,85kV;
6 - Ua = 8,2kV;
Presión [bar] - el parámetro indica la presión del aire comprimido en el sistema neumático de sujeción del electrodo expresada en bares; el parámetro determina la fuerza descendente del electrodo en relación con el material durante la soldadura.
Modo de trabajo [0/1] - El parámetro que define el modo de trabajo soldadura . 0 valor indica que la máquina está trabajando en modo 'Tiempo' soldadura . 1 el valor indica que la máquina está trabajando en modo 'Corriente' soldadura . Una descripción detallada de los modos de funcionamiento "Tiempo" y "Corriente" se proporciona en páginas 71-72 de la documentación.
Regulación modo [0/1] - El parámetro que define el rango de ajuste automático modo de el condensador de salida . Tecleando 1 valor (modo MAX ) se pasa a pleno ajuste automático modo de el condensador de salida. xm valor (modo MIN) significa que durante la soldadura, el condensador de salida se ajusta sólo cuando la corriente de ánodo supera el valor introducido en el parámetro Potencia máx . Una descripción detallada de los MAX y MIN modos de funcionamiento se proporciona en página 72 de la documentación.
Opciones:
Modo de trabajo espera / trabajo
- verde botón
significa que el máquina es convertido encendido y listo a trabajo, trabajo durante funcionamiento normal.
- naranja botón
significa que el máquina es en modo de espera. Este modo es usado a Hilerado el máquina a modo dormir, que da el posibilidad de la calefacción de la electrodo antes de el turno de trabajo.
Una situación de referencia:
Un turno de trabajo dura de 7:00 am - 3:00 pm.
El Operador terminando el turno en 3 p.m. debe NO apagar la máquina en elINTERRUPTOR PRINCIPAL y debe NO pulsar el botón PARADA DEEMERGENCIA ; debe sólo poner la máquina en STANDBYxml-. ). El operador ajusta el electrodo calentamiento, encender tiempo en esta ventana, en la tabla 'ELECTRODO PARA CALENTAMIENTO AJUSTES PARA MODO DE ESPERA '; en nuestro caso, calentamiento es para estar activo desde 6:40 xml-ph-0030@deepl.inter
A continuación, el operador abandona la máquina . Este ajuste hará que el electrodo de la máquina se engrane en 7 cada día, como se indica, en orden para permitir operación eficiente desde el comienzo de el turno y facilitando así soldadura de xml-ph-0 repetible. La situación anterior se muestra en el siguiente gráfico .
Fig. 21 Ventana del modo de espera
|
Para el modo de espera a funcione correctamente: En debe sea Conmutado en en el principal ventana utilizando el naranja botón
|
|
|
Electrodo abierto / cerrado
- un abra candado en el rojo fondo indica que la soldadura electrodo fue no cerrado en su titular, cuando usted pulse el gris candado cerrado el estará cerrado.
|
Además, cuando el mensaje mensaje como como ATENCIÓN, ELECTRODO ABIERTO parpadea, se también significa que el electrodo portaelectrodos es abierto. |
- a cerrado candado en el verde fondo indica que el soldadura electrodo es cerrado en su titular, cuando usted pulse en el gris candado abierto el estará abierto.
|
|
|
|
Regulación Temp apagado / on
- pulsador
señales que el electrodo estabilizador de temperatura es Conmutado en, pulsando
el pulsador gira fuera de estabilización de la temperatura.
- pulsador
señales que el electrodo estabilizador de temperatura es Conmutado en, pulsando el
pulsador gira fuera de estabilización de la temperatura.
Girar en temperatura estabilización resultados en el mantener de a estable nivel de temperatura y un calidad de soldadura repetible.
Luz apagado/encendido
- a lámpara que hace no resplandor en el rojo fondo indica que el trabajo tabla iluminación en el soldadura zona es Conmutado off, al pulsar el gris lámpara incandescente, la iluminación se cambiar en.
- a resplandeciente lámpara en el verde fondo indica que el trabajo tabla iluminación en el soldadura zona es Conmutado en, cuando usted pulse la lámpara gris, el iluminación se cambiar off.
Láser 1 off / encendido
- pulsador
señales que el láser indicador 1 es Conmutado off, pulsando el pulsador
gira en el láser indicador 1.
- pulsador
señales que el láser indicador 1 se conmuta en, pulsando el pulsador
gira apagar el indicador láser 1.
Láser 2 off / encendido
- pulsador
señales que el láser indicador 2 es Conmutado off, pulsando el pulsador
gira en el láser indicador 2.
- pulsador
señales que el láser indicador 2 se conmuta en, pulsando el pulsador
gira apagar el indicador láser 2.
En el estándar, el láser indicador denotado como Láser 1 es situado en el izquierda lateral de el soldadura cabeza y Láser 2 en su derecha lado, mirando de el frente de el máquina, que es, de el lado del panel de control / lado del operador.
Modo de trabajo
Actual / Hora
- el eléctrico circuito en el verde fondo indica que el máquina es trabajando en 'Actual soldadura modo; pulsando el gris reloj indica que el máquina se introduzca el 'Tiempo modo de soldadura. 'Actual' modo de soldadura indica que el de la máquina contador tiene iniciado Contando alta soldadura de frecuencia tiempo, que fue entró en en el Soldadura tiempo parámetro, como pronto como la máquina reconoce el apropiado valor de el la ánodo actual que debe superar o sea igual a el valor entró en en el Trabajo actual parámetro. Para poner it de forma diferente, en Actual soldadura modo, el soldadura tiempo es igual a el suma de ambos el valor de el tiempo el máquina toma a producir el ánodo corriente- que es, el valor entró en en el Funcionamiento potencia parámetro- y el valor de tiempo entró en en el Tiempo de soldadura parámetro.
Si el máquina hace no gestionar a producir Funcionamiento potencia dentro del 25 segundos, el ciclo de trabajo se interrumpirá.
- el reloj en el verde fondo indica que la máquina es trabajando en 'Tiempo soldadura modo; pulsando el gris, eléctrico circuito indica que el máquina se entre en 'Actual' soldadura modo. En 'Tiempo soldadura modo indica que alta frecuencia soldar tiempo es igual a el valor introducido en el recetas con el nombre Tiempo de soldadura.
En es vale notando que en 'Tiempo, soldadura modo, el deber ciclo puede ser ejecutado incluso si el máquina tiene no gestionado a producir Funcionamiento poder. En resultado de este se sea que el soldar logrado puede ser de fuerza irregular.
Modo de regulación min / max
- pulsador
señales que el máquina es trabajando en limitado automático ajuste modo de el salida condensador; pulsando el pulsador
interruptores it en completo automático ajuste modo de el condensador de salida. En min modo significa que durante soldadura, el salida condensador se ajusta sólo cuando el ánodo actual supera el valor insertado en el Potencia máxima parámetro.
- pulsador
que el máquina es trabajando en completo automático ajuste modo de el salida condensador; pulsando el
pulsador interruptores it en limitado automático ajuste modo de el condensador. El máximo modo significa que durante soldadura, el salida condensador es ajustado automáticamente así que que el ánodo actual es en el nivel configure en el Potencia de funcionamiento parámetro.
Modo de conducción - el cabezal de soldadura puede trabajar en cinco modos de paso :
- operación en el sitio modo - el máquina funciona estacionario (soldaduras en el mismo Lugar sin en movimiento). Ninguno de los parámetros de paso está activo.
- trabajando modo de izquierda a derecha sin devolver - el máquina hace un soldar en el longitud configure en movimiento a el derecha y sigue siendo en el Lugar de el última soldadura cuando la tarea es terminado.
- trabajando modo de derecha a izquierda sin devolver - el máquina hace un soldar en el longitud configure en movimiento a el izquierda y sigue siendo en el Lugar de el última soldadura cuando la tarea es terminado.
- trabajando modo de izquierda a derecha con devolver - el máquina realiza soldaduras a lo largo de el longitud configure en movimiento a el derecha y devuelve automáticamente a el lugar de la primera soldadura cuando el tarea está terminada.
- trabajando modo de derecha a izquierda con devolver - el máquina realiza soldaduras a lo largo de el longitud configure en movimiento a el izquierda y devuelve automáticamente a el lugar de la primera soldadura cuando el tarea está terminada.
ajuste a base eje X - el botón inicia el proceso de homing el eje X - determinando el cero punto para el recorrido de la cabeza . Para iniciar, mantenga pulsado el botón. El xml-ph-0031@deepl.inte Cuando el botón se vuelve verde y deja de parpadear, el proceso está terminado. Durante el proceso homing, el cabezal de soldadura se desplaza a la izquierda hasta que el final de carrera accione y rebote del final de carrera por la longitud fijada en el programa .
ajuste a base eje Y - el botón inicia el proceso de homing el eje Y - determinando el cero punto para el recorrido de la cabeza. Para iniciar, mantenga pulsado el botón. El xml-ph-0031@deepl.inte Cuando el botón se pone verde y dejan de parpadear, el proceso está finalizado. Durante el proceso homing, el cabezal de soldadura se desplaza a la frontal hasta que el final de carrera acciona y va a la base
ALARMA MENSAJES INDICANDO: NO LISTO PARA INICIAR CICLO DE SOLDADURA:
ATENCIÓN, ELECTRODO ABIERTO - señala que el electrodo mango está abierto. Instale el electrodo de soldadura correctamente y cierre el mango: HMI → Pantalla principal→ Electrodo → cerrado.
NOT READY - señala que la máquina no reinició correctamente y no hubo arranque de 30 segundos. Pulse el botón RESTART en el panel de control .
Si un electrodo especial ha sido instalado en el soporte que permite soldar sin el uso de un electrodo de conexión a tierra , entonces después de pulsar el botón INICIO en el panel del operador , el electrodo de puesta a tierra permanecerá en la posición superior que no inferior. Después de instalar este tipo de electrodo, en la inferior en la pantalla principal de el panel HMI mostrará el mensaje " SOLDADURA ¡SIN PIE DE TIERRA!"
6.6.6 Base de datos de recetas
Fig. 22 ACCIONAMIENTO DE LA CABEZA HF
En la ventana HF Cabezal Accionamiento hay hay receta parámetros que se refieren al paso del cabezal durante un ciclo de soldadura automática :
|
|
|
|
|
|
|
|
SOLDADURA LONGITUD - marcada como WL denota la soldadura longitud (expresada en pulgadas o centímetros dependiendo de la posición de la unidad interruptor en el servicio menú).
ELECTRODO LONGITUD - marcado como EL denota la longitud de el electrodo montado en la soldadura (expresado en pulgadas o centímetros dependiendo de la posición de el interruptor de unidad en el menú de servicio).
SOLAPAMIENTO LONGITUD - marcado como OL denota solapamiento longitud. El solapamiento es la superficie área de el material soldado donde el soldadura parcial solapa el anterior; esto significa que el material es xml-ph-0030@deepl.int Hay dos posibles opciones para los cálculos de la superposición elegida por medios de los pulsadores desuperposición :
- el óptimo longitud de el solapamiento y el número de parcial soldaduras se calcula automáticamente en el base de el total soldar longitud y el longitud del electrodo de soldadura (soldadura parcial) entrada valores.
- el soldar longitud es insertado por el operador. Atención debe sea pagado a la entrada a longitud que se permitir soldadura de el material a lo largo de su completo longitud establecido; en caso contrario, la última soldadura necesitará a realizarse manualmente.
SOLDADURAS SECCIONALES CONTAR - el número de soldaduras parciales a ser realizadas por la máquina en el ciclo automático para soldar el material a lo largo de su longitud completa conjunto. Es no es posible para el operador a fijar este parámetro. Es siempre calculado automáticamente en la base de la longitud total de soldadura dada y la longitud de el electrodo de soldadura .
Si el máquina tiene ha sido parado durante su automático ciclo pulsando el STOP botón en el control panel para a mínimo de 3 segundos entonces el ciclo se no continuar y el número de las soldaduras parciales se reajustar.
Si el máquina tiene ha sido parado durante su automático ciclo pulsando el STOP botón en el control panel y el movimientos del operador el joystick entonces el ciclo se no continuar y el número de la soldaduras parciales se reajustar.
Si el máquina tiene ha sido parado durante su automático ciclo pulsando el STOP botón en el control panel y el cabezal de soldadura es en el soldadura posición (independientemente de si la soldadura proceso tiene no empezó, es corriendo o completado) es posible a continuar el ciclo sólo si el INICIO botón en el panel de control ser presionado.
Si el máquina tiene ha sido parado durante su automático ciclo pulsando el STOP botón en el control panel y el cabezal de soldadura es en el conducir posición es posible a continuar el pulsación de ciclo el "Vaya a a el siguiente posición" botón en el HF ventana de accionamiento del cabezal.
Modo de conducción - el cabezal de soldadura puede trabajar en cinco modos de paso :
- operación en el sitio modo - el máquina funciona estacionario (soldaduras en el mismo lugar sin en movimiento). Ninguno de los Los parámetros de paso están activos.
- trabajando modo de izquierda a derecha sin devolver - el máquina hace una soldadura en el longitud configure en movimiento a el derecha y sigue siendo en el Lugar de el última soldadura cuando la tarea es terminado.
- trabajando modo de derecha a izquierda sin devolver - el máquina hace una soldadura en el longitud configure en movimiento a el izquierda y sigue siendo en el Lugar de el última soldadura cuando la tarea es terminado.
- trabajando modo de izquierda a derecha con devolver - el máquina realiza soldaduras a lo largo de el longitud configure en movimiento a el derecha y devuelve automáticamente a el lugar de la primera soldadura cuando el tarea está terminada.
- trabajando modo de derecha a izquierda con devolver - el máquina realiza soldaduras a lo largo de el longitud configure en movimiento a el izquierda y devuelve automáticamente a el lugar de la primera soldadura cuando el tarea está terminada.
Accionamientomanual - un grupo de pulsadores que permiten el movimiento de la máquina :
El botones con un luz verde fondo se refieren a la máquina viaje en el eje X (derecha / izquierda).
Todos pulsadores para manual paso trabajo con 0.5 sec retraso para prevenir cualquier pulsación accidental.
GO TO TABLE BEGINNING - presionando este pulsador mueve el cabezal de soldadura a el principio del banco.
IR A TABLA FIN - presionando este pulsador se desplaza el cabezal de soldadura hasta el extremo del banco .
A - presionando este pulsador mueve el cabezal de soldadura hacia el sitio de la primera soldadura.
B - presionando este pulsador se desplaza el cabezal de soldadura al lugar de la última soldadura.
Posiciónrelativa - muestra la posición de la máquina relativa a la posición en la cual se ha pulsado el botón Reset situado a su lado .
Mover sobre - el operador inserta la distancia que la cabeza necesita para cubrir en este lugar. Cuando el Ir pulsador es presionado, las máquinas mueven y cubren la distancia fijada en el Mover sobre campo.
Si el entró en valor es destacado en rojo, it significa que el cabezal de soldadura no puede sea movido por el configure valor. Si el cabeza es no en el borde de el tabla y it es físicamente posible a conducir, comprobar si el tabla longitud tiene ha sido correctamente entró en en el ventana del menú de servicio.
En el Vaya a pulsador es presionado, el dirección en que la máquina mueve depende en el entró en carácter, si allí es un positivo valor (sin signo) el máquina se ir a el Bien, si el entró en valor es negativo, la máquina irá hacia la izquierda.
- Pulsando la tecla "más" desplazará el cabezal de soldadura hacia la derecha. El botón desplaza el cabezal de soldadura un milímetro (o una parte de pulgada, según la posición del interruptor de unidad en el menú de servicio) , independientemente del tiempo que se mantenga pulsado.
- Pulsando el "menos" botón se conducir el soldadura cabeza a la izquierda. En botón mueve el soldadura cabeza por a milímetro (o por a pieza de un pulgada dependiendo en la posición de unidad interruptor en el menú de servicio), independientemente del tiempo que se mantenga.
Los botones con un fondo oscuro verde remiten a la máquina se desplaza en el eje Y (adelante/ atrás).
- Pulsando el botón causa el soldadura cabeza a llegar a el posiciones finales, que es, hacia el operador, como especificado en el movimientos en el servicio menú.
- Pulsando el menos botón causa el soldadura cabeza a impulsar, que es, hacia el operador. En botón mueve el soldadura cabeza por un milímetro (o por a pieza de un pulgada dependiendo en el posición de unidad interruptor en el menú de servicio), independientemente de cuánto dura celebrada.
- Pulsando el y botón causa el soldadura cabeza a conducir atrás, que es, fuera de el operador. En botón mueve el soldadura cabeza por un milímetro (o por a pieza de un pulgada dependiendo en el posición de unidad interruptor en el menú de servicio) , independientemente de cuánto dura celebrada.
- Pulsando el botón causa el soldadura cabeza a llegar a el posiciones finales, que es, fuera de el operador, como especificado en el ajustes de movimientos en el servicio menú.
Por encima de el oscuro verde botones y a el izquierda de el luz verde botón la corriente posición de el electrodo, en el Y y eje X, respectivamente. La ubicación del visualización de el actual posición de el electrodo está marcado con flechas en Fig. 23.
Fig. 23 Posición actual del electrodo en la zona indicada por las flechas rojas.
6.6.7 Base de datos de recetas
Fig. 24 Base de datos de recetas
Todas las recetas guardadas en la memoria HMI tarjeta están listadas en la forma de un gráfico. Cada fila contiene una receta y cada columna contiene una de los parámetros de la receta. La descripción detallada de los parámetros fue citada en el capítulo anterior. El gráfico puede contener el ilimitado número de recetas. Debajo del gráfico hay hay una fila titulada Editar receta (sobre el fondo blanco ) utilizada para edición y creación de recetas.
NUEVO RECETA
En orden a crear un nuevo receta llenar en cada cuadro en el Editar receta fila y a continuación, pulse Crear nuevo clave. Sistema debe añadir la recién creado receta a la existente lista xml-ph-0031@deepl.in
En para guardar esos cambia a a receta que eran hecho utilizando el Principal pantalla, pulse el GUARDAR RECETA botón a copia los parámetros de el principal pantalla a el Editar receta bar en el Receta base de datos ventana. En parámetros copiado mayo sea guardado como a nuevo receta utilizando el Cree nuevo botón o ellos puede sea utilizado para actualización una receta existente utilizando el Actualización botón.
EDICIÓN DE RECETAS
En para editar una receta nosotros necesitamos hacer clic en el nombre de la receta que viene de la lista de recetas (la receta seleccionada debe ser resaltada en amarillo y mostrada en Editar receta fila). En lo que respecta a como como un cambio del valor del parámetro en Editar receta fila , necesitamos a hacer clic en la casilla blanca donde debería mostrarse e introducir un nuevo valor. Una vez completado el procedimiento edición , se debe pulsar la tecla Actualizar y como un resultado el introducido cambia a la receta indicada será aceptada, guardada y almacenada.
PROCEDIMIENTO DE SUPRESIÓN
En orden a realizar la receta borrado procedimiento clic en la receta nombre derivado de la recetas lista (seleccionado receta debe ser resaltado en amarillo y muestra en Editar receta fila) y entonces pulse Borrar xml-ph-0029@deepl.intern
RECETA SELECCIÓN PROCEDIMIENTO
En orden a realizar la receta selección procedimiento para producción fines elegir de la recetas' lista la receta con valores requerido para deber ciclo (seleccionado receta debe ser destacado en amarillo y mostrar fila) entonces clic en Cargar para producción clave como un resultado la receta será cargada a el sistema y preparado para uso en producción actual con sus parámetros mostrados en la pantallaprincipal ventana.
CLASIFICACIÓN PROCEDIMIENTO
Las recetas utilizadas para la producción se enumeran en un orden alfabético . La barra de desplazamiento vertical que permite al operador visualizar el el gráfico más suavemente aparecerá en el lado derecho de el gráfico cuando un mayor número de recetas entre en el sistema. El sistema permite al operador ordenar las recetas por nombre o por cada valor de un parámetro (ascendentemente o decrecientemente). En orden a realizar un procedimiento de ordenación , encontrar una fila de cajas negras que debe ser mostrada en la parte superior de el gráfico y hacer clic una vez en una caja negra situada precisamente sobre xml-ph-003 (Haga clic dos veces y la dirección de ordenación cambiará).
6.6.8 Ajuste de la potencia
Fig.25 Ajuste de potencia
En la ventana hay dos indicadores (Fig.25):
Ánodo corriente - un indicador de el ánodo corriente intensidad. El indica el La ánodo corriente intensidad que debe ser igual a la corriente intensidad de el contador analógico que se encuentra en el panel de control.
CAPACITADOR - una herramienta que indica la posición de la salida condensador (dentro de la gama de 0 a 100%). Con la ayuda de esta herramienta el ajuste de el nivel apropiado de potencia puede tomar lugar - como una regla cuanto mayor capacidad, cuanto mayor La corriente anódica es.
Fig. 26 Ajuste de potencia
Un grupo de teclas bajo el indicador (Fig.25 y Fig. 26) se utiliza para el ajuste del condensador de ánodo . El ajuste puede realizarse de dos maneras:
AUTO - antes de soldar el condensador es automáticamente ajustado a la posición correspondiente a los valores introducidos en el parámetroinicial potencia . Cuando se ejecuta el procedimiento de soldadura , la posición del condensador se ajusta automáticamente de manera como el nivel de La ánodo corriente intensidad podría subir hasta el valor inscrito en el parámetro Potencia de funcionamiento .
Elija AUTO ajuste modo durante estándar deber ciclos realizados por el máquina. MANUAL modo es usado para procedimientos de prueba.
MANUAL - todo el condensador ajuste procedimiento se realiza a mano, cuando surge la necesidad el operador puede cambiar la posición del condensador con la ayuda de las teclas "+" o "-" y al mismo tiempo se ajusta la intensidad de la corriente anódica .
6.6.9 Gráfico de trabajo
Fig. 28 Menú Servicio
Apertura el servicio pantalla es no posible durante el ciclo automático.
En esta ventana (Fig.28) se muestran las siguientes piezas de información de origen estadístico :
Ciclo recuento - es es el total número de servicio ciclos desde que la máquina ha sido encendida por primera vez.
Tiempo de trabajo - it es el tiempo total de trabajo de la máquina ,
Alarmaantiparpadeo - este valor indica cuántas veces desde el día en que la máquina fue fabricada, el sistema de protección contra arco-sobre fue conectado .
ánodo sobrecarga alarma - este valor indica cuántas veces desde el día en que la máquina fue fabricada, el nivel máximo de intensidad de corriente en ánodo circuito fue superado y como resultado cuántas veces se conectó el mecanismo de protección contra sobrecarga de ánodo .
Sobrecarga de la red alarma - este valor indica cuántas veces desde el día en que la máquina fue fabricada, se superó el nivel máximo de intensidad de corriente en circuito de red durante soldadura y como resultado cuántas veces se conectó el mecanismo de protección contra sobrecarga de red .
Temperaturadel tubo alarma - este valor indica cuántas veces desde el día en que la máquina fue fabricada , se activó automáticamente el sistema de protección térmica del tubo .
Los parámetros enumerados a continuación están disponibles para los técnicos del servicio del fabricante y para el supervisor . Por esta razón, se requiere una contraseña para poder editar los parámetros.
Control del proceso activo- este botón activa el algoritmo HF de control del proceso . Cada ciclo de soldadura es controlado. Una alarma será visualizada en la HMI si los criterios de soldadura fijados no han sido alcanzados. Los parámetros de control están en la ventana decontrol de proceso .
Estadísticas activo - el activo estadísticas botón permite los datos, en cada soldadura parcial en el ciclo, que ha sido hecho en la máquina, a ser recogido y lo guarda en el Estadísticas El estado de el proceso de soldadura , incluido en las estadísticas, se describe más adelante en el manual.
Visualización en pulgadas - el botón utilizar para cambiar entre unidades (centímetros y pulgadas ). El cambio sólo está activo para el servicio.
Adicional soldadura inicio opción - el interruptor permite iniciar el ciclo de soldadura utilizando dos pulsadores (o uno de ellos si un llave interruptor mando bimanual está en posición de apagado) en el negro mano Fig. 7). El interruptor está activo sólo para el servicio.
Luces de control que muestran el estado de los sensores de la máquina (Sensores):
electrodo arriba - la luz de control , encendida , señala que el interruptor de fin de carrera que muestra la posición superior del electrodo está encendido;
electrodo abajo - la luz de control , encendida , señala que el interruptor de fin de carrera que muestra la posición del electrodo inferior está encendido;
mesa accionamiento posición - el activado control señales el accionamiento posición de la mesa y impide así el inicio de la soldadura;
emergencia electrodo arriba - la luz de control , apagada , señala que el electrodo ha encontrado resistencia mientras bajaba (p. ej. se presiona hacia el banco ) y el interruptor de fin de carrera se apaga ;
pasando inicio - la luz de control , encendida , señala que el cabezal de soldadura se ha desplazado a el inicio de el banco y el interruptor límite está encendido;
pasando final - la luz de control , encendida , señala que el cabezal de soldadura se ha desplazado hasta el final del banco y el interruptor de fin de carrera está encendido .
El botón Alarma historial - abre la pantalla que muestra el historial guardado de alarmas que han ocurrido en la máquina dentro de el último año. El historial de alarmas se guarda en la memoria de el El historial de alarmas para cada día se guarda como un archivo bajo el nombre EL datos, p.ej. EL_20131122. Es posible copiar el historial archivos desde la memoria del panel en un USB xml-ph-0031
Alarma mensajes son guardado en el idioma seleccionado en el menú de servicio.
El botón marcado, Máquina trabajo condiciones abre una ventana (Fig. 29), en la que se ajustan los parámetros individuales de el ciclo de soldadura , tales como:
En configure valores de todos parámetros en Máquina trabajo condiciones son ejemplos.
Presión máx. = Presión + - este parámetro definido por el usuario define el valor del rango superior de fuerza descendente ; al sobrepasar el umbral , una alarma se mostrará en el panel HMI . El control de la presión se inicia cuando comienza el proceso HF .
Presión min. = Presión - - este parámetro definido por el usuario define el valor del rango inferior de descenso . Una alarma será visualizada una vez superado el umbral en el panel HMI; el control de la presión comienza cuando se inicia el proceso HF.
Tabla retardo tiempo [s] - retardo tiempo entre parar el cabezal de soldadura y poner la mesa en la posición soldadura .
Presione retardo tiempo - este valor indica la cantidad de tiempo que transcurre desde el momento el límite inferior interruptor (indicado la posición inferior de el electrodo) es accionado a el momento el electrodo es presionado contra el material con plena fuerza
Esperar tiempo para alcanzar fijar corriente (en corriente soldadura modo) - el parámetro que indica el tiempo que el sistema necesita para alcanzar un valor dado para la corriente anódica. Si la corriente no se ha alcanzado , en ese tiempo, el ciclo de soldadura se interrumpirá y aparecerá el mensaje , 'WELDING PARAMETERS NOT REACHED' . Este parámetro es importante sólo en 'corriente' soldadura .
Potencia máx = Potencia deservicio + ... - Este parámetro se utiliza únicamente para controlar el proceso de soldadura y para determinar el rango superior de tolerancia de corriente. El parámetro es ajustable en el rango de 0 - 1A.
Potencia min = Potencia deservicio - ... - Este parámetro sólo se utiliza para controlar el proceso de soldadura y para determinar el rango superior de tolerancia de corriente . El parámetro es ajustable en el rango de 0 xml-ph-0
Fig. 29 Ventana de condiciones de trabajo de la máquina
Movimientos ajustes botón abre la ventana (Fig. 30), en que los parámetros específicos para la conducción de la placa de presión, se establecen, tales como:
En configure valores de todos parámetros en Movimientos ajustes son ejemplos.
La longitud de mesa entre tapones - un parámetro a introducir la longitud de la mesa montada sobre que la soldadura cabeza mueve.La distancia introducida debe expresar la longitud de trabajo de la mesa (desde el tope izquierdo de la mesa desde el tope derecho de la mesa).
Máquina soldar cabezal anchura entre límite interruptores [cm] - a parámetro para introducir la máquina anchura del cabezal entre los límites de los interruptores.
Longitud mínima de solapamiento [mm] - la longitud mínima de solapamiento que el usuario puede ajustar en modo manual y automático solapamiento .
X - Accionamiento velocidad AUTO - el parámetro determina la velocidad de paso en eje X cuando la máquina está trabajando en el ciclo automático (expresado en porcentaje de la velocidad máxima ).
X - Accionamiento velocidad MANUAL - LENTO - el parámetro determina la velocidad de paso en eje X cuando el operador mueve la máquina manualmente - pulsando ligeramente el joystick (expresado como porcentaje del máximo spe
X - Accionamiento velocidad MANUAL - RÁPIDO - el parámetro determina la velocidad de paso en eje X cuando el operador mueve la máquina manualmente - pulsando fuertemente el joystick (expresado como porcentaje de la velocidad máxima
Y - Accionamiento velocidad AUTO - el parámetro determina la velocidad de paso en eje Y cuando la máquina está trabajando en el ciclo automático (expresado en porcentaje de la velocidad máxima ).
Y - Accionamiento velocidad MANUAL - LENTO - el parámetro determina la velocidad de paso en eje Y cuando el operador mueve la máquina manualmente - pulsando ligeramente el joystick (expresado como porcentaje del máximo spe
Y - Accionamiento velocidad MANUAL - RÁPIDO - el parámetro determina la velocidad de paso en eje Y cuando el operador mueve la máquina manualmente - pulsando fuertemente el joystick (expresado como porcentaje de la velocidad máxima
Ajustar a base eje X - el botón inicia el proceso de homing el eje X - determinar el punto cero para el recorrido de el cabezal. Para iniciar, mantener pulsado el botón. El xml-ph-0031@deepl.inte Cuando el botón se apaga , el proceso está terminado. Durante el proceso homing, el cabezal de soldadura se desplaza a la izquierda hasta que el final de carrera accione y rebote del el final de carrera por la longitud fijada en el programa.
Ajustar a base eje Y - el botón inicia el proceso de homing el eje Y - determinar el punto cero para el recorrido de el cabezal. Para iniciar, mantener pulsado el botón. El xml-ph-0031@deepl.inte Cuando el botón se apaga , el proceso está terminado. Durante el proceso homing, el cabezal de soldadura se desplaza hacia el frontal hasta que el final de carrera interruptor acciona y va a la posición de base (alrededor del medio del eje).
En el homing proceso, el soldadura cabeza mueve en la gama de el seleccionado base eje. Allí debe sea no obstáculo en el recorrido de la máquina.
Eje de referencia debe ser llevado durante:
- el primer después del servicio puesta en marcha,
- en el momento de cambiar la posición del final de carrera,
- cuando el lugar del elemento elemento / máquina es físicamente cambiado (cambio de la cadena tensora).
En el homing proceso, el soldadura cabeza mueve en la gama de la eje base.
Regulacióndel inversor ganancia - un parámetro que tiene un efecto directo sobre el control de velocidad del inversor.
Ajustar posición para distancia defrenado [cm] - El parámetro determina la distancia de frenado del cabezal de soldadura , antes de que alcance la posición deseada (expresada en pulgadas o centímetros dependiendo de la posición de el interruptor unidad en el menú servicio ).
Eje Y límiteinferior [mm] - el parámetro especifica la distancia mínima por la que el accionamiento con el cabezal puede desplazarse hacia atrás, en la dirección de el eje Y (expresado en pulgadas o centímetros dependiendo de la posición de el interruptor de unidad en el menú de servicio ).
Eje Y límitesuperior [mm] - el parámetro especifica la distancia máxima por la que el accionamiento con el cabezal puede desplazarse hacia atrás, en la dirección de el eje Y (expresado en pulgadas o centímetros dependiendo de la posición de el interruptor de unidad en el menú de servicio ).
Fig. 30 Ventana de configuración de movimientos
Botón Control del proceso - este abre la ventana (Fig. 31 ) para definir los parámetros de el proceso de soldadura . Una alarma se visualizará en el HMI si los criterios de soldadura fijados no se han alcanzado . El operador puede fijar los parámetros individuales en xml-ph-0030@deepl.inte
Potencia máx = Potencia deservicio + ... - Este parámetro se utiliza únicamente para controlar el proceso de soldadura y para determinar el rango superior de tolerancia de corriente . El parámetro es ajustable en el rango de 0 - 1A.
Potencia min = Potencia deservicio - ... - Este parámetro se utiliza únicamente para controlar el proceso de soldadura y para determinar el rango superior de tolerancia de corriente . El parámetro es ajustable en el rango de 0 - 0,5A.
Punto de consigna % para la corriente que es para estar en tolerancia - este parámetro especifica el porcentaje valor de el tiempo para que la corriente es requerido para estar dentro tolerancia. Cuando el porcentaje umbral prescrito no ha sido alcanzado, una alarma será mostrada en el panel HMI indicando que los parámetros de soldadura no han sido alcanzados . El parámetro se expresa en porcentaje, en el rango de 0-100%.
Medido total soldadura tiempo [s]: - este parámetro muestra el total tiempo empleado por la última soldadura. El tiempo se cuenta desde el momento se ha alcanzado la corriente almacenada en la receta..
Medido tiempo de soldadura cuando la corriente estaba dentro de la tolerancia [s]: - Este parámetro muestra el tiempo de la última soldadura, sin embargo, es sólo contado para la corriente dentro la tolerancia rango +/- (Potencia max/min) prescrito en los parámetros anteriores.
Valorcalculado para que la corriente estuvo dentro de latolerancia [%]: - Este parámetro muestra el porcentaje de tiempo durante el cual la corriente estuvo dentro del rango de tolerancia +/- durante todo el ciclo.
Presión máx. = Presión + - este parámetro definido por el usuario define el valor de el rango superior de fuerza descendente ; al sobrepasar el umbral, se mostrará una alarma en el panel HMI . La presión xml-ph-0030@deepl.int
Presión min. = Presión - - este parámetro definido por el usuario define el valor del rango inferior de descenso . Una alarma será visualizada una vez superado el umbral en el panel HMI; el control de la presión comienza cuando se inicia el proceso HF.
Fig. 31 Ventana de control del proceso de soldadura
Estadísticas botón - abre una ventana (Fig. 32), en la cual recoge las estadísticas del funcionamiento de la máquina . Cada fila en la tabla relaciona a una de la soldadura parcial de la máquina, mientras las columnas muestran detalles de la soldadura, tales como cuándo se hizo , qué receta se utilizó, qué operador xml-ph- La información detallada sobre cada soldadura permite el proceso completo de un solo ciclo de soldadura a ser trazado y aprender qué valores de ánodo intensidad de corriente y presión fueron alcanzados. Además, la tabla muestra datos registrados anteriormente. En la derecha se encuentra una lista desplegable de fechas con cada fecha mostrando un día de funcionamiento de la máquina . Para ver los datos para un dado
Tiempo - tiempo de la grabación del ciclo;
Fecha - fecha de el registro del ciclo;
1 - Receta- el nombre de la receta utilizada en el ciclo registrado;2 - Operador - nombre del operador conectado durante la ejecución del ciclo;
3 – Posición del condensador [%] - Inicio posición de el condensador;4 - Tiempo de retardo [ s ] - ajustar el tiempo de retardo;
5 - Tiempo de soldadura [ s ] ajustar el tiempo de soldadura;
6 - Tiempo de enfriamiento [ s ] - ajustar el tiempo de enfriamiento;
7 – Nivel de potencia [ 1 - 6 ] - configure nivel de potencia;8 – Ajustar ánodo actual [A] - corriente anódica configure durante la soldadura proceso;
9 – Ajustar presión [ bar ] - configure presión durante el proceso de soldadura;
10 – Trabajo modo [0-1] - el parámetro definición de el soldadura trabajo modo. A detallado descripción de el "Tiempo" y "Actual" funcionamiento modos es en las páginas 71-72 de la documentación;
11 – Reglamento modo 0-1] - el parámetro definición de el gama de ajuste automático modo de el salida condensador. A detallado descripción de el 1 (MAX) y 0 (MIN) funcionamiento modos en páginas 73-74 de la documentación;
12 – Conducir modo - soldadura cabeza conducir modo en el mesa de trabajo. A descripción detallada de el todos conducir modos es proporcionado en páginas 74,77 de la documentación;
13 – Auto solapamiento [0-1] - una de dos posible opciones para el cálculos del solapamiento elegido por significa de el Solapamiento pulsadores. 1 significa auto solapamiento, 0 significa manu solapamiento (véase documentación en la página 76);
14 – Longitud de soldadura - la longitud de soldadura;
15 – Longitud del electrodo - el electrodo longitud utilizado en el ciclo;
18 – Parcial número de soldadura - el número de soldaduras seccionales;
19 – Proceso control activo [0-1] - activa o desactiva el HF algoritmo de control del proceso (véase documentación en páginas 91-93);
20 – Proceso estado [0-1] - estado de el proceso, donde 0 indica un error - un interrumpido procesador o soldadura parámetros que tienen no ha sido alcanzado, 1 indica éxito - el soldadura proceso corrió según a el parámetros preestablecidos;
21 – Actual en tolerancia [0-1] - parámetro definición de si el actual valor era en o fuera de tolerancia En ánodo actual obtenido debe sea en +/- de la tolerancia gama de el ánodo actual valor para a dado porcentaje de el momento de la duración de la soldadura. 1 medio que una tolerancia ánodo corriente se obtuvo durante soldadura. 0 significa llegando a el ánodo actual fuera de el margen de tolerancia;
22 – Presión en tolerancia [0-1] - parámetro definición de si el presión era en o fuera de tolerancia En presión obtenido debe sea en +/- de el margen de tolerancia del valor de presión. 1 significa que se ha obtenido una presión de tolerancia durante la soldadura. 0 significa que se ha alcanzado la corriente anódica fuera del rango de tolerancia;
23 - Corriente anódica media [A ] - corriente anódica media durante la soldadura seccional;
24 - Presión media [bar] - presión media durante la soldadura seccional;
25 - Contador de ciclos - el contador de ciclos a partir de la primera puesta en marcha de la máquina.
El registro del proceso sólo tiene lugar en el modo.

Fig. 32 Ventana de estadísticas
Botón Modo Standby - ajustes - abre una ventana (Fig. 21) que contiene tablas Electrodo calefacción ajustes para modoStandby . Una descripción detallada de el modo Standby se proporciona en las páginas 69-70 de la documentación .
6.7 Archivos de historial y recetas
El siguiente software es necesario para leer y convertir historia archivos y recetas en un ordenador con sistema operativo Windows:
el gratis, EasyBuider Pro software, que puede sea descargado de la HMI panel de el del fabricante página web: http://www.weintek.com/ o representante en Polonia http://www.multiprojekt.pl/ftp/weintek_hmi/easy_builder_pro/Microsoft Excel u otra hoja de cálculo programa.
6.7.2 Conversión de ficheros históricos en xlsx.
Para leer datos históricos , debe debe descargarse de la memoria de del el panel táctil en el PC ; estos deben introducirse en la carpeta apropiada ; haga doble clic en el archivo que contiene la fecha en cuestión; se generará un archivo xlsx (Excel) entonces . El archivo presenta los datos históricos de interés en una manera clara y transparente .
6.7.3 Conectar el ordenador a la máquina mediante WiFi
Cada máquina está equipada con un router WiFi , que, a su vez, está conectado al panel del operador. Para conectar su ordenador a esta red siga estos pasos:
En el ordenador equipado con a inalámbrico red tarjeta, seleccione el red con a nombre correspondiente a el fábrica número de el máquina tal y como figura en su placa de características, por ejemplo: D650-QE-104.6.7.4 Lectura de la dirección IP de la máquina para copiar recetas y archivos archivos
Al panel táctil se le asigna una dirección fija IP . Para leerla, debe:
- Pulse el icono con una flecha en la esquina inferior derecha del panel táctil
- Se abre el menú contextual del panel
- Pulse el segundo icono desde la izquierda, una tarjeta con la letra 'i'. Esto abrirá la ventana 'System Information'; la dirección IP necesaria para crear una conexión de red con el panel será mostrada allí.
- Después de guardar la dirección IP , pulse OK - la ventana se cerrará .
6.7.5 Copiar el historial archivos desde el panel de la HMI utilizando la red WiFi redSi tu ordenador está conectado a una red WiFi :
- Abierto Windows Explorador en cualquier carpeta y entre en el siguiente fórmula en el dirección bar donde el IP dirección es situado, para ejemplo: 192.168.189.10; el dirección leer de el toque panel debe ser introducido:ftp://uploadhis:111111@192.168.189.10/
- A continuación, pulse "Intro".
- Se abrirá una ventana con la memoria del panel táctil
- El contenido completo de cada carpeta puede ser copiado. Es también posible copiar archivos individuales que están almacenados en las carpetas .
6.7.6 Datos archivados en la memoria del panel táctil de la IHMCopia de recetas, historial de trabajo y el historial de alarmas en a dispositivo USB:
1. Inserte un dispositivo USB de memoria en el puerto del panel táctil HMI .
2. En la pantalla del panel HMI, aparecerá una ventana . En la pantalla del panel HMI, aparecerá una ventana , pulse Cargar.
3. En la ventana siguiente , seleccione Cargar historial archivos, introduzca la contraseña: 111111 y pulse OK.
4. Abra la carpeta marcada "usbdisk" y seleccione la carpeta "disk_a_1", luego pulse OK.
En la memoria USB se guarda el"historial" , que contiene las carpetas :
- "datalog"→ "trend" - la carpeta "trend" contiene archivos con registros de los parámetros de trabajo de la máquina . Cada día, un archivo se guarda bajo la correspondiente fecha. Para leer los datos históricos , introduzca la memoria USB en el ordenador , luego en la carpeta "TREND" , hacer doble clic en el archivo requerido a generar un archivo en el formato xls (Excel) en ordenar a ver claramente el historial de el funcionamiento de la máquina o a generar un gráfico para un xml-ph-0 dado Para generar archivos xls , se requiere el software gratuito el programa EasyBuider Pro ; este debe descargarse desde la página web del fabricante del panel HMI: http://www.weintek.com/.
- "eventlog" - la carpeta "eventlog" contiene archivos con registros de el historial de alarmas que han ocurrido durante el funcionamiento de la máquina . El histórico de alarmas para cada día se guarda como un archivo llamado EL_data, por ejemplo EL_20131122. Para leer datos históricos , insertar la memoria USB en el ordenador, luego doble clic en el archivo requerido para generar un archivo en el formato xls (Excel) para a claramente ver la alarma historia xml-ph-0030@deepl.inte Para generar archivos xls , se requiere el software gratuito el programa EasyBuider Pro ; este debe descargarse de la página web del fabricante del panel HMI: http://www.weintek.com/.
- "receta" - la carpeta "receta" contiene dos archivos con recetas copiadas del panel HMI : "receta.db" y "receta_a.rcp". Los archivos pueden utilizarse como copia de seguridad para las recetas o para guardar las recetas xml-ph-0030@deepl.i También es posible editar recetas en el ordenador .
Edición de recetas copiadas desde el panel HMI:
Para editar recetas , se requiere el software gratuito programa EasyBuider Pro ; éste debe descargarse de la página web de el fabricante de el panel HMI : http://www.weintek.com/.
1. Introduzca la memoria USB - con recetas copiadas - en el ordenador y abra la aplicación Utility Manager . En la sección Conversión deDatos , elija la aplicación Editor de Base de Datos deRecetas .
2. En la aplicación Receta Base de datos Editor haga clic en Importar... y seleccione los archivos con las recetas copiadas"recipe.db".
3. Se abrirá la ventana de edición de recetas .
4. Cuando haya terminado de editar , haga clic en en Exportar... y guarde el archivo en su ubicación anterior.
Copia de recetas desde una memoria USB:
- Inserte el dispositivo USB en el puerto del panel táctil de la HMI.
- En el pantalla de el HMI panel, a ventana se aparecer, haga clic en en Descargar.
-
En la ventana siguiente , seleccione Descargar historial archivos, introduzca la contraseña: 111111 y haga clic en OK.
4. Abra la carpeta "usbdisk" y seleccione la carpeta "disk_a_1", y luego haga clic en OK.
Las recetas se cargarán en la memoria de el panel táctil HMI . Apague la máquina y y, a continuación, enciéndala .
El panel táctil puede también estar protegido contra accesos no autorizados . No es posible trabajar en la máquina sin que el usuario se registre en el panel táctil.
1. Después de encender la máquina , haga clic en el botón "Log-in" en la ventana del panel táctil , en la barra de estado en la parte inferior.
2. Se abrirá una ventana contextual para iniciar sesión.
Fig. 33 Ventana de inicio de sesión
3. Seleccione un apropiado usuario de la lista desplegable.4. Introduzca el apropiado contraseña.
5. Pulse el botón Inicio de sesión botón.
6. El nombre del usuario se aparecen en el campo Conectado usuario'.
7. Pulse OK y la ventana cerca.
En el principal ventana, siguiente a el inicio de sesión botón, el nombre de el el usuario actualmente conectado es exhibido.
En el máquina es Conmutado off, el usuario es registrado automáticamente.
Cambiar la contraseña asignada al usuario.
1. Inicie sesión como un usuario con autoridad para cambiar contraseñas.
2. Pulse el botón"Cambiar pase".
4. Introduzca el Nueva contraseña.
5. Pulse 'Cambia'.
6. Pulse OK y la ventana cerca.
Fábrica usuarios creados y su asignados contraseña(s)
NOMBRE DE USUARIO - CONTRASEÑA
SERVICIO - DESTINADO AL SERVICIO DEL FABRICANTE;
Operador - 100
Supervisor - 111 Permisos:
OPERADOR - puede trabajar en la máquina , puede seleccionar recetas, no puede editar recetas y las opciones avanzadas máquina en la ventana del Menú Servicio.
SUPERVISOR - puede trabajar en la máquina , seleccionar recetas, editar recetas, cambiar parámetros, cambiar las contraseñas de otros usuarios.
6.9 Conexión a la fuente de alimentación
BAJO NO CIRCUNSTANCIAS debe el máquina sea operado por sin reservas personal. En máquina los operadores deben sea familiar con el ocupacional seguridad y normas sanitarias.
Antes de que la máquina se conecte a una fuente de alimentación se deben realizar los siguientes procedimientos :
- Asegúrese de que el entorno de trabajo de la máquina (la máquina y su entorno) esté limpio y ponga en orden o haya no ningún obstáculo que pueda influir negativamente en el ciclo de trabajo estándar de la máquina; y
- Asegúrese de que la cantidad adecuada de materia prima (piezas de prueba ) esté preparada; y
- Asegúrese de que las papeleras y contenedores para productos soldados están colocados en el lugar adecuado pero en proximidad a la máquina debido a los requisitos de Bayer aplicando a el ciclo de producción si lo hubiera; y
- Asegúrese de que todas las protecciones estén adecuadamente fijadas a la máquina y las puertas laterales de una caja de interruptores estén cerradas; y
ATENCIÓN ! Caja de interruptores puertas debe sea siempre cerrado incluso si la máquina es se detuvo.
En de la máquina reiniciar procedimiento es imposible a sea realizado cuando el escudo es inapropiadamente adjunto a el máquina o las puertas de la caja de interruptores están abiertos
5. Asegúrese de que el botón PARADA DEEMERGENCIA esté desbloqueado. Si el botón pulsador con cabeza de seta se ha atascado gírelo hacia la derecha.
En reiniciar procedimiento no puede sea intérprete cuando el PARADA DE EMERGENCIA es el botón atascado (atascado).
7. Hacer seguro el accionamiento manual comprimido aire cierre válvula (Fig.9) está apagada, en caso de que la válvula deba encenderse - gírela a la izquierda - posición ON; y
8. Hacer seguro el nivel de presión en el neumático sistema es entre 0,4 y 0.8 MPa (el clasificado funcionamiento presión de el máquina viene a 0,6 MPa) si el necesita surge diríjase a ajuste procedimiento con el ayuda de el comprimido aire válvula de cierre (Fig.9); y
9. Hacer seguro el PRINCIPAL INTERRUPTOR es configure a 1-ON posición y como a resultado el indicador POWER comenzará a parpadear en el panel de control; y
ATENCIÓN: EMERGENCIA STOP botón puede sea pulsado en en cualquier momento de trabajo ciclo especialmente cuando el emergencia cierre se necesita con prontitud.
10. Asegúrese de que la máquina se reinicie con la ayuda de la tecla azul RESTART , entonces esperar durante 30 segundos dentro de que la máquina debe convertirse en totalmente activado y obtener listo para trabajo como el indicador en la luz señal columna empieza a parpadear verde y la barra de progreso encontrada en la pantalla principal del panel HMI está completamente verde.
ATENCIÓN ! En pulsando el REINICIAR (después de girando en la máquina) se sea base soldadura cabeza - el eje movimiento hacia atrás / adelante.
En caso el alarma mensaje es aparece incluso si el máquina fue reiniciado véase capítulo 6.6.2.
11. Asegúrese de que el electrodo esté montado en el soporte.
ATENCIÓN ! En electrodo debe sea siempre montado en el soporte cuando va a estar cerrado.
Véase capítulo 6.13. para más información aplicando a el procedimiento de utillaje Sustitución y Entorno.
- Levante el electrodo hasta su posición superior.
- Gire el INTERRUPTOR PRINCIPAL a la posición 0-OFF - significa que la máquina está apagada.
- Cierre la válvula manual de cierre del aire comprimido (para realizar el procedimiento - gire la válvula hacia la derecha - posición OFF).
- Poner en orden el entorno de trabajo alrededor de la máquina.
- Tanto el enchufe de alimentación eléctrica como el del sistema de aire comprimido deben desenchufarse en caso de parada prolongada del trabajo (ambos enchufes deben extraerse de las tomas).
6.11 Procedimiento de prueba y ajuste


El procedimiento de prueba y ajuste debe ponerse en práctica cuando:
- la máquina se ha encendido por primera vez,
- la sustitución del utillaje (cuando surja la necesidad),
- se ha completado el procedimiento de mantenimiento,
- los operarios deben familiarizarse con el funcionamiento de la máquina.
Para realizar dicho procedimiento el operador deberá:
1. Fijar la temperatura que debe ser mantenida por el electrodo durante la soldadura (por ejemplo 40oC para pruebas) utilizando ELECTRODO TEMPERATURA termorregulador.
2. Vaya al panel sensible al tacto: HMI → Ventana de ajuste de potencia → ponga el modo de ajuste del condensador en MANUAL → con la ayuda de las teclas "-" y "+" asegúrese de que el procedimiento de cambio de posición del condensador se realiza sin problemas en cada nivel de potencia que va de 0 a 100%. Una vez finalizado el procedimiento de comprobación cambie el modo de ajuste del condensador a AUTO

3. Coloque el interruptor HF OFF/ON en la posición OFF

4. Cargue la receta adecuada desde la memoria del panel táctil: HMI → Ventana de base de datos de recetas → resalte la receta deseada en el gráfico → a continuación, pulse la tecla Cargar para producción o rellene las siguientes casillas de los parámetros del ciclo de soldadura que se encuentran en la pantalla principal:
- Potencia inicial;
- Potencia de funcionamiento;
- Tiempo de retraso;
- Tiempo de soldadura;
- Tiempo de enfriamiento;
- Nivel de potencia;
6. Pulse en el panel HMI: HMI → Ventana de accionamiento del cabezal HF → Modo de accionamiento.
→ A;
7. Pulse en el panel HMI: IHM → Pantalla principal → Opciones → Regulación Temp → on;8. Pulse en el panel HMI: HMI → Pantalla principal → Modo de trabajo → 0 ;
9. Pulse en el panel HMI: HMI → Pantalla principal → Modo de regulación→ 1;
10. Asegúrese de que la almohadilla aislante de la mesa de trabajo o del separador de chapa de aluminio esté limpia: no puede estar ni sucia ni dañada mecánicamente en el punto donde el electrodo se presiona contra el material soldado;
ATENCIÓN ¡! El aislante aislante debe ser colocado directamente debajo de la material soldado material como que es supone para proteger el operador contra un eléctrico arco eléctrico formado entre el soldadura electrodo y la mesa de trabajo.
ATENCIÓN ! Si el divisor fue cubierta con el aislante almohadilla debería Adherirse a el tabla estrechamente - en tal a camino que no impurezas entre el divisor y la mesa de trabajo podría encontrar.
12. Realice la referenciación en los ejes X e Y. Durante la referenciación, el cabezal de soldadura se desplaza. El proceso de homing se señaliza mediante la retroiluminación del pulsador.
13. Para comprobar el funcionamiento del joystick

14. Para comprobar el funcionamiento del joystick

15. Utilice el botón

16. Compruebe en la ventana del menú Servicio si el electrodo abajo está encendido.
17. Si la medida de seguridad, señalada por el mensaje ELECTRODO DE EMERGENCIA UP se activa - el electrodo bajado sobre el material, subirá espontáneamente. En el caso anterior, se debe realizar el ajuste del final de carrera que indica la posición inferior del electrodo, tal y como se describe en el capítulo 6.4.
18. Utilice el botón

19. Compruebe en el Servicio menú para ver si el electrodo arriba está encendido.
20. Pruebe a subir y bajar el electrodo varias veces para asegurarse de que se mueve con suavidad.
21. Baje el electrodo de soldadura sobre el material y presione el INICIO el ciclo automático de soldadura debe realizarse con el generador de alta frecuencia apagado.
23. Coloque el interruptor HF OFF/ON en la posición ON ,
2. Pulse en el panel HMI: HMI → Pantalla principal → Modo de regulación→ 1 o 0 ;
Trabajo modo actual / tiempo (1/0) y Reglamento Modo min / máx (0/1) se han descrito en detalle en el capítulo 6.6.5.
3. Bajar el electrodo de soldadura sobre el material exactamente en el lugar de la soldadura.
ATENCIÓN: En es posible a stop el soldadura proceso repetidamente en cualquier momento utilizando la tecla STOP pulsador.
4. Pulsar el botón START - se iniciará un ciclo automático de soldadura de acuerdo con los parámetros indicados en la ventana de el panel principal HMI . Las indicaciones de el ANODO CORRIENTE manómetro deben ser observadas - durante la soldadura; la corriente debe aumentar dentro del rango marcado en verde en la escala del manómetro.
5. Cuando todo el proceso se ha completado , la calidad de la soldadura debe evaluarse . El conocimiento práctico es indispensable para la correcta evaluación; por lo tanto es es mejor buscar el consejo del personal del Contratista y realizar la primera puesta en marcha de la máquina con él.
6. Si el sellado costura producido es desigual a lo largo de la extensión entera, usted necesitará leer el capítulo 6.14.
7. Dependiendo de el efecto de la soldadura (soldada, no soldada, sobrecalentada) los parámetros de soldadura deben ajustarse en consecuencia:
- Potencia inicial;
- Potencia de funcionamiento;
- Tiempo de retraso;
- Tiempo de soldadura;
- Tiempo de enfriamiento;
- Nivel de potencia;
- Presión.
8. Asegúrese de que los siguientes parámetros se hayan sometido muchas horas de pruebas relativas a: trabajo en el mismo tipo de material, ciclo de trabajo de la máquina y funcionalidad, ergonomía de la máquina normas que son cruciales para evitar lesiones graves durante el ciclo de producción;
9. Una vez que los parámetros estética y resistencia de la soldadura 1 se hayan alcanzado los valores deben ser guardados como receta: HMI → Pantallaprincipal → haga clic en el botón GUARDAR RECETA → Recetas base de datos ventana → introduzca el nombre de la receta en la fila titulada Editar receta → pulse la tecla Crear nueva .
10. Coloque el interruptor HF OFF/ON en la posición OFF ,
11. Eleve el electrodo a su posición superior .
12. Pulse en el panel HMI: HMI → Pantalla principal → Trabajo modo → 0 ;
13. Pulse en el panel HMI : HMI → HF Cabezal Accionamiento ventana → Accionamiento Modo → AB;
14. Pulse en el panel HMI : HMI → HF Cabezal Accionamiento ventana → Superposición → auto;
15. Extienda el material a soldar sobre el banco de trabajo.
16. Inserte soldadura longitud en el panel táctil: HMI → HF Cabezal Accionamiento ventana → SOLDAR LONGITUD(WL).
17. Inserte electrodo longitud en el panel táctil: HMI → HF Cabezal Ventana deaccionamiento → LONGITUD DEL ELECTRODO (EL).
18. Utilización de el joystick mover it a el posición en que el soldadura debe comience y pulse botón
a inferior el electrodo en el soldado material. Asegurarse de que el el material se esparce correctamente;
19. Pulse el botón START en el panel del operador - se iniciará un ciclo de soldadura automático con el generador de alta frecuencia apagado .
20. La máquina soldará a lo largo de la longitud introducida y a continuación se detendrá.
21. Pulse y mantenga pulsado el botón : HMI → HF Cabezal Accionamiento ventana → Manual Accionamiento → A en el panel táctil - el cabezal de soldadura moverá a la posición por encima de la primera soldadura.
22. Pulse y mantenga pulsado el botón : HMI → HF Cabezal Accionamiento ventana → Accionamiento manual → B en el panel táctil - el cabezal de soldadura se moverá a la posición por encima de la última soldadura.
23. Pulse y mantenga pulsado el botón : HMI → HF Cabezal Accionamiento ventana→ Accionamiento manual → IR A TABLA FIN en el panel táctil - el cabezal de soldadura se moverá a el extremo del banco .
24. Compruebe si el paso final control se ha activado en la ventana del menú Servicio .
25. Pulse y mantenga pulsado pulsador: HMI → HF Cabezal Accionamiento ventana → Accionamiento manual → IR A TABLA INICIO en el táctil panel - el cabezal de soldadura se moverá a el principio del banco.
26. Compruebe si el paso inicio control luz se ha encendido en la ventana delmenú de servicio .
27. Escribe: HMI → HF Cabeza Conducir ventana → Manual Conducir → Mover acerca de , para ejemplo 100 cm (o 39 pulgadas si el unidad interruptor en el menú de servicio es en pulgadas posición) en el panel táctil y entonces pulse el Vaya a pulsador al lado ella - el cabezal de soldadura se moverá 100 cm (o 39 pulgadas si el interruptor de unidad en el menú de servicio es en posición pulgadas) a la derecha.
Si el entró en valor es destacado en rojo, it significa que el cabezal de soldadura no puede sea movido por el configure valor. Si el cabeza es no en el borde de el tabla y it es físicamente posible a conducir, comprobar si el tabla longitud tiene ha sido correctamente entró en en el ventana del menú de servicio.
En el Vaya a pulsador es presionado, el dirección en que la máquina mueve depende en el entró en carácter, si allí es un positivo valor (sin signo) el máquina se ir a el Bien, si el entró en valor es negativo, la máquina irá hacia la izquierda.
28. Escribe: HMI → HF Cabeza Conducir ventana → Manual Conducir → Mover acerca de , para ejemplo 50 mm (o 1,95 pulgadas si el unidad interruptor en el menú de servicio es en pulgadas posición) en el panel táctil y entonces pulse el Vaya a pulsador junto a it - el soldadura cabeza se mover 50 mm (o 1,95 pulgadas si el unidad encendida el menú de servicio está en posición en pulgadas) a el atrás.
29. Pulse y mantenga pulsado el botón : HMI → HF Cabezal Accionamiento ventana → Accionamiento manual → A en el panel táctil - el soldadura cabezal moverá a la posición por encima de la primera soldadura.
30. Coloque el interruptor HF OFF/ON en la posición ON ,
31. Con el botón bajar el electrodo sobre el material soldado asegurándose de que el material se extiende correctamente,32. Pulse el botón START en el panel del operador - comenzará un ciclo automático de soldadura con alta frecuencia.
Si se ha instalado un electrodo especial en el soporte que permite soldar sin utilizar un electrodo de masa, después de pulsar la tecla INICIO en el panel del operador, el electrodo de masa permanecerá en la posición superior - no bajará. Después de instalar este tipo de electrodo, en la pantalla principal aparecerá el mensaje " ¡SOLDADURA SIN PIE DE TIERRA! ".
33. Después de realizar una soldadura completa, compruebe si las soldaduras parciales se solapan en el lugar donde lo hacen correctamente.34. Una vez realizada toda la costura de soldadura, hay que comprobar si las costuras parciales se solapan correctamente en la zona de solapamiento. Si no es así, hay que ajustar la posición paralela del electrodo como se describe en el capítulo 6.14.
El primer ciclo de trabajo del operador se basa en las siguientes actividades :

1. Arranque la máquina siguiendo el procedimiento descrito en el capítulo 6.9.



- Potencia inicial;
- Potencia de funcionamiento;
- Tiempo de retraso;
- Tiempo de soldadura;
- Tiempo de enfriamiento
- Nivel de potencia
- Presión
- WELD LENGTH (WL) en la ventana RF Head Drive;
- LONGITUD ELECTRODO (EL) en la ventana RF Head Drive;
- OVERLAP LENGTH (OL) (opcional) en la ventana RF Head Drive. Seleccione el solapamiento automático (pulse
botón)
8. Pulse en el panel HMI: HMI → Pantalla principal → Modo de trabajo → 0 o 1;
9. Pulse en el panel HMI: HMI → Pantalla principal → Modo de regulación→ 1 o 0;
10. A continuación, haga clic de nuevo en el panel HMI: HMI → Ventana de ajuste de potencia → poner el modo de regulación del condensador en posición AUTO ;
11. Preparar el material para soldar en la mesa de trabajo donde se vaya a realizar el procedimiento;
12. Utilizando el joystick, colóquelo en la posición en la que debe comenzar la soldadura y utilice el botón para bajar el electrodo sobre el material soldado. Asegúrese de que el material está correctamente colocado;
13. Pulsar el botón START en el panel de control - se iniciará un ciclo automático de soldadura con alta frecuencia según los parámetros indicados en la ventana del panel HMI. Debe observarse la lectura del medidor de CORRIENTE ANÓDICA; durante la soldadura la corriente debe aumentar dentro del rango marcado en verde en la escala del medidor.
La zona de soldadura está protegida de la radiación no ionizante por el electrodo de masa móvil que se presiona contra la mesa durante el procedimiento de soldadura y, como resultado, se crea una especie de condensador que se supone que limita la radiación no ionizante. El electrodo de puesta a tierra desciende por encima del material soldado cuando se enciende la alta frecuencia, pulsando el botón START del panel del operador.
Particular atención debe ser prestar a el hecho que la superficie de la material a ser soldar es uniformemente distribuida en la trabajo de trabajo y no ondulado.
Particular atención debe ser a que en son no metal objetos cerca de la puesta a tierra electrodo y debajo de él.
Si un electrodo especial ha sido instalado en el soporte que permite soldar sin el uso de un electrodo de conexión a tierra , entonces después de pulsar el botón INICIO en el panel del operador , el electrodo de puesta a tierra permanecerá en la posición superior - lo hará no inferior. Después de instalar este tipo de electrodo, en la pantalla principal mostrará el mensaje " xml-ph-0030@deepl.
14. Cuando el trabajo esté terminado, apague la máquina de acuerdo con el procedimiento descrito en capítulo 6.10.
El portaelectrodos de soldadura está equipado con el sistema automático de sujeción rápida controlado desde el panel táctil HMI. Permite al operario ahorrar tiempo y cambiar el electrodo sin utilizar instrumentos.
¡ATENCIÓN! Tenga en cuenta el peso del electrodo durante el procedimiento de cambio del mismo. Se recomienda encarecidamente que dos personas realicen el cambio de electrodo en caso de que sea grande y pesado. Un manejo incompetente del electrodo puede provocar que el operario se apriete las manos al extraer el pesado electrodo de la pinza.
Para llevar a cabo el procedimiento de cambio de electrodos, siga los siguientes pasos:
- Conecte la máquina a las fuentes de alimentación eléctrica y neumática - la máquina debe estar lista para realizar el ciclo de trabajo rutinario (lo que significa que los mensajes de alarma no deben aparecer y el electrodo debe encontrarse en su posición superior),
- Ajuste en la pantalla principal del panel: HMI → Opciones → Electrodo → Abrir,
- Mueva el electrodo hacia la izquierda o hacia la derecha (depende de la versión de la máquina) - el electrodo debe deslizarse fuera de los soportes;
- Deslizar un nuevo electrodo sobre los soportes utilizados para la sujeción, desplazar el electrodo hacia la izquierda o hacia la derecha (depende de la versión de la máquina).
- Ajuste en la pantalla principal del panel: HMI → Opciones → Electrodo → Cerrado.
6.14 Ajuste de la posición paralela del electrodo de sellado en relación con la mesa y el eje de la costura de sellado
Fig. 34. Sujeción del electrodo
Herramientas necesarias:
Llave 30
Llave Allen 4
1. Ponga en marcha la máquina, reiníciela y prepárela para un funcionamiento normal, es decir, que no muestre mensajes de alarma en el panel táctil y que esté 'disponibilidad encendido'. Encontrará una descripción de la puesta en marcha de la máquina en este capítulo: 6.6.2. Compruebe si la superficie de sellado del electrodo es uniforme y compruebe también si el electrodo:
a. está doblada;
b. se retuerce;
c. tiene muescas;
d. tiene protuberancias.
Cada uno de los defectos mencionados dará lugar a una costura irregular, a menos que se hayan creado explícitamente, como por ejemplo para el trazado de un patrón en la superficie de sellado del electrodo.
En caso de que se produzca un defecto de este tipo, será necesario reparar el electrodo.
3. Inserte el electrodo de sellado en la empuñadura y ciérrela (véase el capítulo 6.12).4. Prepare el material a sellar en la mesa de trabajo.
5. Bajar el electrodo con el joystick de uso sobre el material a sellar.
6. Compruebe en la ventana del menú Servicio si el indicador de electrodo caído está encendido.
7. Si es seguro continuar, como indicará el mensaje ELECTRODO DE EMERGENCIA ARRIBA -queaparecerá después de soltar el electrodo sobre el material- se levantará automáticamente. A continuación, ajuste el final de carrera que apunta a la posición inferior del electrodo, tal y como se describe en el capítulo 6.4.
8. Levante el electrodo y llévelo a la posición superior.
9. Compruebe en el menú Servicio si el indicador de electrodo levantado está encendido.
10. Pruebe el electrodo varias veces bajándolo y levantándolo para asegurarse de que su movimiento es suave.

Fig. 35. Costura con un incorrectamente ajustado posición paralela de el electrodo en relación a el sellado costura eje.
- Levante el electrodo para la posición superior .
- Producir una muestra de costura hecha a partir de al menos dos costuras parciales .
- Cuando la costura esté lista, compruébelo:
- Para uniformidad a lo largo de toda la superficie - si ella es desigual, entonces uno debe ligeramente bajar el agarre con el electrodo, utilizando tuercas B y C en aquellas zonas donde el electrodo no xml-ph (primero afloje ligeramente la correspondiente tuerca en B y a continuación, apriete la correspondiente tuerca en C).

Fig. 36. Regulación de la posición paralela de el electrodo en relación a la mesa con el uso de tuercas B y C (vista frontal de el electrodo agarre).
- Compruebe si el principio de la segunda costura parcialmente se solapa con el final de la primera costura - Fig. 35. Si se no se solapan, uno debe ajustar el agarre con el electrodo, paralelo a la costura eje, xml-ph-0030@deep (aflojar ligeramente las tuercas en B y a continuación aflojar ligeramente los tornillos en A en el lado donde el electrodo no solapa con la costura y apretar los tornillos pertinentes en A en xml-ph-0031@

Fig. 37. Ajuste de el paralelo posición de el electrodo en relación a el costura eje con el uso de los tornillos en A (vertical vista de un sección de el electrodo agarre).
7.0 Selección de los parámetros de soldadura
ATENCIÓN: En máquina debe no realizar el soldadura procedimiento sin un aislante almohadilla en el electrodo. Debido a la apropiadamente aplicado aislante almohadilla el número de el formación de fenómenos de sobretensión en la superficie de el electrodo es disminuido.
7.2 Selección de la potencia de salida
Con el fin de para alcanzar el más alto nivel de productividad en el relativamente bajo nivel de soldaduras defectuosas el operador de la máquina debe realizar el procedimiento de ajuste de la potencia para cada electrodo sustituido . Dicho procedimiento se realiza con la ayuda de los controles Ua AJUSTE y del parámetro Potencia de funcionamiento .
Una vez la potencia es ajustada y el proceso de soldadura es iniciado las indicaciones de el ANODO CORRIENTE amperímetro son sujetas a inspección visual . Cuando las mediciones son en el aumento ello significa que en este particular momento comienza el proceso de soldadura . El parámetro del tiempo de soldadura debe corresponder con el valor de el parámetro debido a que la alta frecuencia procedimiento de soldadura se detendrá como resultado de la aguja indicadora del amperímetro parada.
Cuando la soldadura proceso termina la calidad de soldadura necesita someterse a la inspección visual. Si la calidad de la soldadura es insuficiente el nivel de potencia debe aumentarse. En caso de que la solución arriba mencionada no traiga ningún resultado fructífero, entonces el parámetro de tiempo puede aumentarse . Sin embargo, el valor de potencia no debe ser demasiado alto ya que puede conducir a productos, aislante pad y el electrodo daños causados por un arco-sobre.
7.3 Selección de los parámetros de tiempo de soldadura
Como regla , el tiempo de soldadura para materiales fabricados de PVC duro no debería ser superior a 4-5 seg.. Debido a la experiencia del fabricante valores más altos de los dichos parámetros no tienen ninguna influencia sobre la calidad de costura lograda pero deteriora suficientemente la eficiencia del proceso. Si la soldadura proceso dura más durante procedimientos de prueba significa que la potencia ajuste necesita ser regulada.
7.4 Ajuste de la presión del electrodo
En para soldar la lámina de PVC el material debe ser presionado por el electrodo con la presión fuerza oscila de 0,5 a 3 kg/cm2. La medición de la fuerza de presión mientras seleccionando el más apropiado valor sería sería demasiado consume tiempo y además en práctica este método resultaría inútil . Generalmente, en orden para realizar el ajuste procedimiento con éxito, el operador necesita para notar algunas irregularidades que vienen a existencia durante procedimiento de soldadura y en costura apariencia. Cuando la presión es demasiado baja las siguientes irregularidades llegan a existencia:
- susceptibilidad a chispa descargas que se producen entre dos electrodos como el aire, que debería haber sido exprimido fuera, se produce en entre dos capas de lámina y como un resultado se forma una intensidad de corriente irregular;
- aparición de aire burbujas en la costura;
- aparición de costura fuerza que es pequeño
If the pressure is particularly low, there can occur something usually called “film boiling”. When the film is welded under very low pressure, it can be deformed into a foamy product of very low resistance. Applying excessive pressure is also inappropriate, as it can make the film very thin along the place of welding and thus also result in lower resistance of the welded material. Therefore, it is recommended to follow the principle saying that the thickness of film after welding should be equal to at least half the initial thickness of both layers of film. The appearance and proper shape of characteristic leakage that is usually formed along both edges of the welded place has also significant influence on the resistance properties of the welded material. If such a leakage does not appear, it usually indicates insufficient resistance of the welded place, which can be very easily tested. The lack of the leakage after the welding process can be caused by applying too low output power or insufficient pressure. If you use electrodes with cutting edges, it is very important to position the cutting edge correctly. It is usually assumed that the cutting edge of the electrode should protrude from the welding plane by about half the thickness of welded film. In order to check the operation of the cutting edge, it is necessary to make several test welding cycles and remove the film scraps. The result of tests can be considered satisfactory when removing the film scraps along the line of welding takes no more than one cut with scissors.
8.0 Mantenimiento
Gracias a las soluciones constructivas aplicadas y a la estructura sin complicaciones de la máquina, las actividades de mantenimiento y control, tanto preventivas como de emergencia, son relativamente sencillas y no requieren largas interrupciones en el funcionamiento de la máquina.
La máquina de soldar requiere poco trabajo relacionado con la máquina
funcionamiento y mantenimiento, siempre que se mantengan unas condiciones de uso adecuadas. Es necesario comprobar periódicamente el estado técnico de la conexión de la máquina a la red eléctrica, en particular el estado del sistema de protección contra descargas eléctricas.
Todos los componentes del generador de alta frecuencia, en particular todos los elementos aislantes, deben mantenerse limpios. Debe limpiar a fondo el interior del sistema de salida del generador al menos una vez cada tres meses. Tras dicha limpieza, debe comprobarse el estado de los componentes del generador y de las unidades que cooperan directamente con el generador, y deben apretarse todas las conexiones.
Debido a las propiedades específicas de la máquina, se recomienda que algunas de las tareas mencionadas sean realizadas por personal de servicio técnico autorizado y debidamente cualificado del Fabricante (se aplica particularmente a situaciones de emergencia). Las tareas mencionadas requieren especial cuidado y atención.
ATENCIÓN: Durante el funcionamiento del generador, sus componentes, así como los componentes del circuito de salida, tienen una tensión de hasta 8 kV CC y una tensión de alta frecuencia de hasta 480 V (27,12 MHz ).
ATENCIÓN: Los condensadores del generador de ánodos pueden retener carga eléctrica de la tensión de hasta 8000 VDC incluso después de desconectar la máquina de soldar de la red eléctrica. Antes de tocar los componentes del generador de alta frecuencia, estos condensadores deben estar siempre descargados.
La puesta a tierra de la estructura de la máquina debe realizarse con especial cuidado. Recuerde que el generador no debe funcionar nunca cuando las pantallas de protección estén retiradas, tampoco durante las actividades de servicio técnico y mantenimiento, cuando el nivel de seguridad de la máquina puede ser inferior debido a la reparación que se está realizando.
Todas las tareas de mantenimiento y reparaciones requieren un permiso de las personas autorizadas.
Debe mantener un REGISTRO DE LA MÁQUINAque incluya las fechas y los tipos de actividades preventivas o reparaciones realizadas.
Durante las tareas de mantenimiento o cualquier otra operación manual requerida, nunca entre ni ponga ninguna parte del cuerpo en la zona expuesta a peligros potenciales y predecibles, con el fin de eliminar el riesgo de situaciones peligrosas potenciales y predecibles.
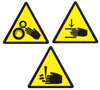
Lleve siempre ropa de protección y calzado antideslizante, para reducir el riesgo de caídas. Asegúrese siempre de llevar las mangas bien ajustadas alrededor de las muñecas o debidamente remangadas.
Utilice siempre guantes de trabajo cuando trabaje con componentes con bordes afilados.
Todo el personal responsable del funcionamiento y mantenimiento de la máquina debe estar debidamente formado e instruido.
Todas y cada una de las operaciones de mantenimiento o reparación pueden ser realizadas exclusivamente por personal autorizado y cualificado, capaz de interpretar correctamente los defectos y fallos, leer los diagramas de instalación y los planos técnicos, con el fin de garantizar que todas las operaciones de desmontaje y montaje relacionadas con los procedimientos de mantenimiento estándar se realicen de forma profesional y -lo más importante- segura.
Todas las tareas realizadas en el área de operación de la unidad de prensado, es decir, el montaje y desmontaje del electrodo, realizadas cuando la alimentación de la máquina está encendida, pueden ser llevadas a cabo exclusivamente por el personal debidamente formado en Salud y Seguridad en el Trabajo, incluyendo particularmente el riesgo que implica la operación de la unidad de prensado.
También debe prever el posible comportamiento no estándar de la máquina, cuando el sistema neumático de la máquina de soldar o los conductos de suministro de aire comprimido estén desprecintados. Esto provocará un descenso automático lento de la unidad de prensado de la máquina de soldar.
El personal debe ser informado de dicho riesgo durante la formación en Salud y Seguridad en el Trabajo.
ATENCIÓN: Durante todas y cada una de las operaciones mencionadas debe detenerse el funcionamiento de la máquina.
8.2 Programa preventivo - Revisiones periódicas
AL COMIENZO DE CADA TURNO
- Compruebe si la zona de funcionamiento de la máquina está limpia y ordenada;
- Compruebe visualmente si las pantallas de protección están bloqueadas;
- Compruebe la iluminación de la zona de operaciones;
- Compruebe si el botón de PARADA DE EMERGENCIA funciona correctamente;
- Compruebe la protección principal en la instalación eléctrica;
- Comprobar el estado de los elementos conductores de cobre y latón en la zona del portaelectrodos y de los elementos de puesta a tierra de las pantallas laterales de protección.
CADA 100 HORAS DE FUNCIONAMIENTO DE LA MÁQUINA (AL MENOS UNA VEZ POR SEMANA):
- Compruebe si los tornillos portantes (incluidos, en particular, los tornillos de fijación de las herramientas) están correctamente fijados y apretados;
- Compruebe el nivel de agua de condensación en el recipiente del filtro de aire comprimido; si hay agua, vacíe el recipiente; si hay grandes cantidades de contaminantes sólidos, desmonte y lave el recipiente;
CADA 500 HORAS DE FUNCIONAMIENTO DE LA MÁQUINA (PERO AL MENOS CADA DOS SEMANAS)
- Compruebe si el radiador de la lámpara de ánodo está limpio;
- Compruebe la cantidad de contaminantes sólidos y polvo en la cámara del generador; si es necesario, limpie la cámara con un aspirador o una pistola de aire comprimido;
- Compruebe si los elementos móviles (en particular las herramientas y las guías) están limpios;
- Engrase los elementos móviles, especialmente las guías; si es necesario, utilice grasa sólida a base de litio y un engrasador;
- Compruebe y pruebe la unidad de alarma.
CADA 1000 HORAS DE FUNCIONAMIENTO DE LA MÁQUINA (PERO AL MENOS CADA SEIS MESES)
- Compruebe visualmente el estado de los elementos mecánicos;
- Apriete todos los tornillos;
- Compruebe si las medidas de protección contra descargas eléctricas funcionan correctamente;
- Comprobar la eficacia del engrase de las guías;
- Compruebe el estado de los elementos de contacto principales: deben sustituirse los contactos principales u otros elementos de contacto del sistema, como contactos o relés de superficies excesivamente desgastadas.
CADA 5000 HORAS DE MÁQUINA FUNCIONAMIENTO (PERO EN POR LO MENOS CADA SEIS MESES)
- sustituir aceite calefacción electrodo - aceite tipo L-LH-46.
ATENCIÓN: Antes de cada mantenimiento, apague la máquina con el interruptor principal y desconecte la alimentación principal.
SE PROHÍBE lubricar la máquina durante el funcionamiento.
9.0 Salud y seguridad en el trabajo
9.1 Requisitos básicos
- La máquina puede utilizarse exclusivamente de forma adecuada a su finalidad explícitamente descrita en el punto 1.
- Las soluciones constructivas aplicadas relacionadas con la seguridad reducen al mínimo tanto el comportamiento no estándar de la máquina como los peligros para los operarios y otras personas que tengan contacto con la máquina, siempre que se observen los principios del trabajo seguro. La máquina está equipada con interruptores de llave en las pantallas de protección, cuyo desmontaje requiere herramientas específicas, incluyendo el interruptor en la puerta de la cámara de soldadura, el botón de PARADA DE EMERGENCIA y las pantallas de protección móviles que encierran la zona de soldadura durante el tiempo del proceso de soldadura.
- Las cuestiones relacionadas con la seguridad y la salud en el trabajo y la evaluación de riesgos durante el contacto de una persona con la máquina se han descrito detalladamente en los capítulos anteriores de este manual.
- Como este tema es extremadamente importante, algunas instrucciones se repiten en esta sección.
- Todo nuevo empleado que tenga contacto con la máquina de soldar debe recibir formación en el campo de los principios básicos de salud y seguridad en el trabajo y familiarizarse con los tipos de riesgos que implica el funcionamiento de la máquina de soldar, a menos que el operario siga las normas y principios obligatorios.
- El personal responsable del manejo de la máquina de soldar debe tener conocimientos profundos de primeros auxilios en casos de descargas eléctricas y quemaduras. En el caso de personas que trabajen con dispositivos que utilicen ondas electromagnéticas de frecuencia en el rango de 0,1 - 300 MHz, se requieren exámenes médicos periódicos.
- Tras la instalación de la máquina de soldar, es necesario medir la emisión de campo electromagnético y establecer los límites de la zona peligrosa.
- En función de los resultados de las mediciones, se determinan el nivel de peligro y el tiempo durante el cual los operarios pueden permanecer en la zona peligrosa, de conformidad con las normas aplicables.
- Sólo pueden acceder a la zona peligrosa los operarios que dispongan de las autorizaciones pertinentes para trabajar en la zona expuesta a campos electromagnéticos, basadas en reconocimientos médicos especializados, y que hayan recibido la formación adecuada sobre el manejo seguro de los dispositivos que emiten campos electromagnéticos.
- Las mediciones mencionadas deben ser realizadas por una institución autorizada. Las instrucciones detalladas relativas a dichas mediciones se especifican en la normativa aplicable en el país donde se utiliza la máquina.
- Los operarios de las máquinas deben llevar siempre ropa de trabajo estándar, guantes, casco y calzado antideslizante.
- El entorno de trabajo de la máquina, el suelo y los soportes y asideros manuales deben estar siempre limpios y exentos de cualquier tipo de contaminación, grasa o barro, a fin de reducir al mínimo posible el riesgo de resbalones o caídas.
- No utilice nunca la máquina en el modo de funcionamiento automático sin los elementos de protección fijos o móviles. Compruebe periódicamente si todos los interruptores de emergencia y todos los demás elementos de protección están bien montados y funcionan correctamente.
- Todo operador de la máquina debe ser instruido sobre las funciones de los elementos de protección de la máquina y su correcta utilización.
- En la zona que rodea la máquina (aproximadamente 1,5 m alrededor de la máquina) no puede haber objetos que puedan interferir en el funcionamiento de la máquina. Esta zona debe mantenerse limpia y disponer de iluminación adecuada.
- No utilice nunca los manipuladores de la máquina ni los tubos flexibles como soportes. Recuerde que cualquier movimiento accidental del manipulador de la máquina puede poner en marcha accidentalmente el funcionamiento de la máquina.
- Informe siempre al supervisor y/o al personal de tráfico sobre todos y cada uno de los casos de funcionamiento incorrecto de la máquina.
- Todas las tareas de mantenimiento y reparaciones requieren un permiso de las personas autorizadas.
- Debe llevar un Registro de máquinasque incluya las fechas y los tipos de actividades preventivas o reparaciones realizadas.
- Durante las tareas de mantenimiento o cualquier otra operación manual requerida, nunca entre ni ponga ninguna parte del cuerpo en la zona expuesta a peligros potenciales y predecibles, con el fin de eliminar el riesgo de situaciones peligrosas potenciales y predecibles.
NO UTILICE NUNCA LA MÁQUINA DE SOLDAR CUANDO LAS PANTALLAS DE PROTECCIÓN ESTÉN RETIRADAS O CUANDO LOS INTERRUPTORES DE LLAVE ESTÉN BLOQUEADOS. ESTO SE APLICA ESPECIALMENTE A LAS PANTALLAS DE PROTECCIÓN DEL GENERADOR.
Estas pantallas de protección reducen la emisión de campos electromagnéticos e impiden que se toquen accidentalmente los elementos del circuito eléctrico con tensión de alimentación o alta tensión de hasta 8000 V.
- Lleve siempre ropa de protección y calzado antideslizante, para reducir el riesgo de caídas. Asegúrese siempre de llevar las mangas bien ajustadas alrededor de las muñecas o debidamente remangadas.
- Utilice siempre guantes de trabajo cuando trabaje con componentes calientes o con bordes afilados.
- También hay que recordar que en los componentes que no se han cubierto detrás de ninguna pantalla por razones ergonómicas, es decir, el electrodo y los componentes conductores del portaelectrodo, hay tensión de alta frecuencia. NUNCA TOQUE ESOS COMPONENTES DURANTE EL PROCESO DE SOLDADURA.
- Tocar esos componentes durante el proceso de soldadura provoca quemaduras en la piel con tensión de alta frecuencia. Sin embargo, no es peligroso para la vida ni para la salud.
- El método adoptado de alimentación eléctrica de la máquina de soldar plantea un riesgo potencial de prensado o aplastamiento de miembros en el espacio entre el prensado de los electrodos. Todos y cada uno de los trabajos en el área de operación de la unidad de prensado, es decir, el montaje y desmontaje de los electrodos o extender y retirar el material y la chatarra, que se realizan cuando la máquina de soldadura está conectada a la fuente de alimentación se pueden hacer exclusivamente por los empleados formados en el campo de la salud y seguridad en el trabajo, incluyendo la información sobre el riesgo planteado por la unidad de prensado.
- Durante el funcionamiento de la máquina, el operario debe situarse en la zona indicada a continuación
Fig. 38. ZDWA-15-C-3 - zona de trabajo de seguridad (color verde )
9.3 Condiciones de seguridad laboral del personal encargado del mantenimiento y reparación de la máquina de soldar- Estos trabajos requieren un cuidado especial. Hay que recordar siempre que los condensadores del generador anódico pueden mantener la carga eléctrica de la tensión de 8000 V incluso después de desconectar la máquina de soldar de la red eléctrica. Antes de tocar los componentes del generador de alta frecuencia, estos condensadores deben estar siempre descargados.
- Durante el funcionamiento del generador, sus componentes, así como los componentes del circuito de salida, tienen la tensión de alta frecuencia. La puesta a tierra de la estructura de la máquina debe realizarse con especial cuidado. También hay que recordar que el tiempo de funcionamiento del generador con los escudos de protección quitados debe reducirse al mínimo.
- Todas las reparaciones deben ser realizadas de acuerdo con los principios vigentes de reparación y funcionamiento de dispositivos por una persona que tenga un certificado adecuado expedido por la Asociación de Electricistas correspondiente (en Polonia: SEP).
- Todo el personal responsable del funcionamiento y mantenimiento de la máquina debe estar debidamente formado e instruido.
- Todas y cada una de las operaciones de mantenimiento o reparación pueden ser realizadas exclusivamente por personal autorizado y cualificado, capaz de interpretar correctamente los defectos y fallos y de leer los diagramas de instalación, con el fin de garantizar que todas las operaciones de desmontaje y montaje relacionadas con los procedimientos de mantenimiento estándar se realicen de forma profesional y, lo que es más importante, segura.
- Durante todas y cada una de las operaciones mencionadas debe detenerse el funcionamiento de la máquina.
TOMAR TODAS LAS MEDIDAS NECESARIAS PARA PREVENIR:
- Utilizar la máquina de forma distinta a la descrita en este Manual de Operación y Mantenimiento,
- Instalación incorrecta, no realizada de acuerdo con los procedimientos descritos en este manual,
- Manejo inadecuado de la máquina o su manejo por personal sin la formación adecuada,
- Suministro a máquina de parámetros inadecuados,
- Mantenimiento insuficiente de la máquina,
- Alteraciones no autorizadas o interferencias por parte de personas sin las licencias, permisos o formación necesarios,
- Utilizar piezas de recambio distintas de las originales,
- Cualquier acción de cualquier persona que no esté de acuerdo con los principios especificados en este Manual de Operación y Mantenimiento y cualquier información de advertencia.
10.0 Documentación eléctrica
10.1 Parámetros de la fuente de alimentación - Datos técnicos
Alimentación |
3 x 220 VAC; 50/60 Hz |
Capacidad instalada |
22 kVA |
Potencia de salida en HF |
15 kW |
Tensión de funcionamiento |
24 VDC |
Frecuencia de funcionamiento |
27,12 MHz |
Protección de sobreintensidad principal |
63A |
Estabilidad de frecuencia |
+/- 0.6 % |
Lámpara generadora (triodo metalocerámico) |
ITL 12-1 |
Sistema de control PLC |
DELTA |
Sistema de circuito antidescarga |
ANTIFLASH completo con filtro HF |
10.2 Planos de diseño del concepto de instalación eléctrica
Ver apéndices
11.0 Documentación neumática
11.1 Datos técnicos
Presión de funcionamiento |
0,4 - 0,8 MPa |
Consumo de aire comprimido |
Máx. 70 nl (estándar) por ciclo |
Pureza del aire |
según ISO8573-1:4-4-4 |
Rendimiento de filtrado |
20 um (ISO8573-1 4-4-4) |
11.2 Principio de funcionamiento
- accionamiento de los soportes neumáticos del electrodo;
- accionamiento del electrodo conectado a tierra;
- unidad de prensa;
- soportes para electrodo.
Además, el sistema neumático consta de un sistema de preparación del aire: filtro y reductor de presión, arranque progresivo, elementos de conexión, válvula de descarga y válvulas estranguladoras de retención. El aire se suministra a través de la válvula de descarga a la unidad VFRL; se filtra previamente y se reduce al volumen necesario. A continuación, se suministra a través de válvulas de distribución controladas eléctrica o electroneumáticamente a los actuadores neumáticos apropiados iniciando su movimiento. La dinámica del movimiento de los actuadores puede ajustarse mediante válvulas de estrangulación montadas en los actuadores. La secuencia del movimiento de los actuadores está controlada por el controlador de la máquina de soldar.
11.3 Manual de instrucciones
VER ANEXOS
12.0 Eliminación
12.1 Instrucciones generales
Las soluciones constructivas aplicadas y los componentes de alta calidad permiten el correcto funcionamiento de la máquina durante un período de unos 30 años. Sin embargo, pueden producirse algunos cambios en las necesidades del Cliente o cambios en los principios o normas que no pueden predecirse hoy en día, lo que podría requerir una eliminación de la máquina antes de que finalice el periodo mencionado. Esto también se aplica a las piezas o componentes sustituidos o reparados de la máquina de soldar.
El Cliente está obligado a garantizar que la eliminación de la máquina o de sus componentes se realiza de conformidad con los requisitos legales aplicables vigentes en un momento y lugar determinados.
Todos los componentes de la máquina son reciclables.
La eliminación de residuos peligrosos siempre debe correr a cargo de empresas especializadas.
Los tipos de residuos producidos durante el ciclo de vida del aparato se describen a continuación en el punto 12.2.
12.2 Residuos
- Trozos de tela o papel saturados de sustancias utilizadas para la limpieza de los componentes de la máquina;
- Piezas de recambio usadas del generador, según el material del que estén hechas;
- Residuos de grasas líquidas o sólidas;
- Grasa sobrante tras el engrase o mantenimiento de la máquina;
- Lámpara del generador.
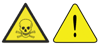
Todos los residuos producidos en el curso de actividades de sustitución o servicio técnico, que estén contaminados con grasa, no pueden eliminarse junto con los residuos industriales.

12.3 Procedimiento de desmontaje de la máquina antes de su eliminación
- Coloque la máquina de modo que permanezca inmóvil.
- Desconecte la alimentación eléctrica de la máquina.
- Desconecte el suministro de aire comprimido de la máquina.
- Retire los conductos flexibles de plástico o goma y asegúrese de que los elimina una empresa especializada.
- Desconecte y retire los cables y dispositivos eléctricos y asegúrese de su eliminación por una empresa especializada.
- Separe los componentes de acero y los de metales no ferrosos y asegúrese de que los elimina una empresa especializada.
13.0 Apéndices
13.1 Etiqueta de modelo y número de serie
Cada máquina Miller Weldmaster tiene esta pegatina situada en la parte trasera de la máquina. Identifica el modelo y el número de serie de cada soldadora.
También indicará la tensión y los hercios necesarios para el funcionamiento.
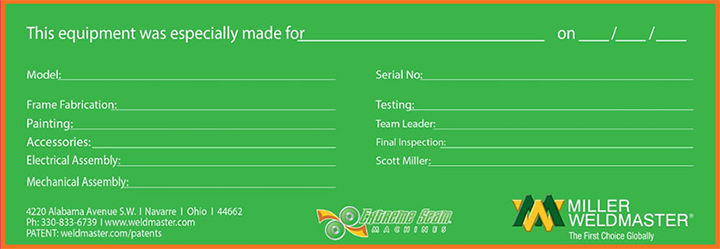